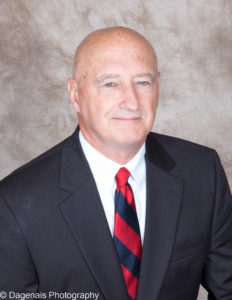
(Photo courtesy of Dagenais Photography)
Jack Titus has managed a R&D metallurgical laboratory with all manner of scientific instrumentation as well as transferred plasma nitriding, LPC and HPGQ (high pressure gas quench) technology from around the world to the U.S. He holds patents on vacuum furnace and vacuum carburizing technology.
In this article for Heat Treat Today, Jack shares his experience as a member of a team whose task was to transfer the nitriding process known as ion nitriding. The lessons he learned are valuable to heat treaters today.

One of the ways companies advance their technology offering is by transferring technology from other sources, primarily offshore entities that have developed a process that has been successful in their home market. However, there are associated risks because what has been accepted in one market may not be as popular in another. One major variable is the different design culture: an intangible that is easy to overlook. An analogy I often use when explaining this cultural difference deals with race cars. European Formulae One race cars have a sleek-looking, open-wheel design that’s easy on the eye. In contrast, the NASCAR grand-national series of race cars appears bulky and rugged—more like our passenger cars—and look crude compared to Formulae One, but they have huge engines and are fully capable of reaching speeds of well over 200 mph.
European—especially German—engineered furnaces often appear as sleek looking as Formulae One cars and are very capable of successful heat treating, but they are fragile and require more attention to maintenance than their U.S.-based counterparts. This was certainly the case with Degussa and their 20-bar vacuum furnaces and sinter–hip systems, as well as ALD’s low-pressure carburizing (LPC) and high pressure gas quench (HPGQ) systems. The following discussion documents my experience as part of the team that endeavored to transfer the nitriding process known as ion nitriding, developed by Kloeckner Ionon GmbH, a German company that advanced the process in the mid-1970s. The process and events are accurate as far as my memory from that era can muster. I’ll use initials for the names of the companies or the individuals and substitute “The Company” for the U.S. transferee.
The transferee team consisted of a manager, a marketing director, and others tasked with “Americanizing” the product—a big mistake. My task was to spend about a month at a Kloeckner commercial heat treat facility learning how the process was controlled and the do’s and don’ts for preparing loads so I could train potential users on the technology. To further the effort, company S purchased a smaller production unit from Kloeckner with all of the current state-of-the-art (German) controls to be installed in the R&D section of The Company for conducting sales tests.
At that time in the mid-1970s, other U.S.-based companies were just putting their toes in the water to see if the process was real, but Kloeckner was the perceived expert in the field.
The unit placed in R&D was a fully capable vertical unit with a hearth plate 24-in. (609 mm) diameter by 48 in. (1219 mm) high, the result of years of development by Kloeckner. The Company was just entering the digital age, upgrading from analog controls, so the decision was made to develop their own process control for discrete logic and temperature control. All of the voltage, ampere, and temperature controls in the Kloeckner unit were analog with dampening features that made for very smooth outputs. Again, at the time, Allen-Bradley was the primary manufacturer of PLCs used by company S for furnace motion control, but the nitriding unit had no material handling requirements, therefore, all of the controls were process variables, making a full blown PLC unnecessary. Barber Coleman was the other digital controller company that specialized in plastic injection molding process control using their EDAC programmable logic controller, which made it the logical choice for the primary controller. It employed EPROMS that could be programmed and erased at will, making logic changes much easier. The EDAC was also used on The Company’s vacuum furnaces successfully, so using it seemed a wise course.
For those unfamiliar with plasma nitriding, the following is the Reader’s Digest version of the process:
A DC voltage converted from AC via a series of diodes with a maximum of 1000 volts is applied to a work piece and is the cathode of the circuit. Radiation shields and the vessel proper are the anode with a positive ground. When the power is applied to the parts and nitrogen and dissociated ammonia are used, it produces a purple glow. The learning curve associated with plasma nitriding is pretty complex, and dealing with holes—especially blind holes—can be problematic.
When power is first applied to the work piece after evacuation the moisture and/or residue left on parts causes a long delay in heating as an arcing phenomenon begins. Specialized circuitry in the logic measures the voltage drop as arcs occur and “crowbars” the power to a choke, a transformer that absorbs the current and allows it to dissipate to ground. In doing so, a huge magnetic field is created that must be accounted for, and that is one of the reasons the EDAC was used. It was intrinsically hardened against such severe interferences so much that, with the choke side of the cabinet door opened, the image on the EDAC CRT was pulled off the screen momentarily without any damage to the processor.
The glow produced by the energy is referred to as the glow seam: as the partial pressure in the vessel increases, the glow seam becomes thinner and power is concentrated. It could then create a seam overlap resulting in very intense and localized power within holes of a certain size, enough to locally melt the metal. When processing parts of various sizes and shapes, care must be taken to avoid these circumstances.
One of the disadvantages of the process is the very long time it takes for the sparking and arcing to subside and allow enough continuous power to heat the parts. Pre-process degreasing and/or thorough washing was mandatory to reduce the sparking and arcing time. We eventually learned that preheating parts, even in air, to 400°F (204°C) dramatically improved heating time. Part of Kloeckner’s control logic embedded within the solid-state circuitry counted the arcs per second. If the arcing reached a certain level, power was reduced, which allowed a more sustained applied energy—improving the heating time but not nearly the same positive effect as preheating.
During my initial visit to a Kloekner heat treat, I was astounded at the amount of hands-on experience required to control the process. Since nitriding takes place between 900°F (482°C) and 1000°F (537°C)—which is below the visible color range—when viewing through a sight glass, the operator would cover himself and the sight glass with a black photographer’s cape so as to shield out ambient light, allowing him to easily see the dull red of the relative temperature of the parts in the load. Along the way of transferring the process learning curve, it became obvious why Kloeckner only employed pit vessels for plasma nitriding. Since there was no additional heat source other than the energy produced by the glow seam, parts located in the center of the part array would heat much faster than parts positioned around the perimeter of the circular base plate. Therefore, when processing multipart loads, parts expected to take longer to heat would always be placed in the center of the arrangement.
As a typical load was coming up to heat, the operator would visually inspect the parts for color variation and, if detected, pause heating until all parts became uniform before continuing to heat. A thermocouple was used for temperature control; however, placing it required some experience. The end of the TC was protected by an alumina tube to isolate the high voltage and prevent it from shorting to the TC and damaging the analog to digital input board.
I recall that in the mid-1970s, furnace OEMs were just beginning to find ways to relieve the operator from having to make process decisions by incorporating more intelligence into controllers, yet here was a process that required more human intervention not less.
One of the major mistakes The Company made during the learning curve transfer was selling the Kloeckner sales unit to a commercial heat treat in Fort Worth that already had a U.S.-developed (but larger) nitrider. I strongly opposed this move because it would compare Kloeckner’s mature product with years of development behind it and its fluid operation to our new larger unit where development was in its infancy. The Company’s nitrider design reflected the same engineering as their pusher furnaces—over-designed, bulky, and lacking the mature engineering that flows from an evolved design. As a result, the news spread that The Company’s product was not equal to the German unit. Compounding that error in judgment, our marketing director, affectionately known as “Wild Bill”, was promoting plasma nitriding as the end all process before we knew all of the process’s benefits and shortcomings.
Traditional nitriding is still an atmosphere process where little care is required in making up part loads, while plasma nitriding requires careful planning to avoid overlapping the glow seam when parts are placed on the base plate or positioned on racks. As word spread throughout the industry about the special attention and loading complexities required, the honeymoon was short-lived.
A classic example of loading issues arose when I was asked to assist in creating a loading arrangement for synchronizer rings for Chevy Muncie, where the first horizontal vessel was sold. It consisted of two vessels sharing one vacuum system; however, each had its own power supply. Those involved had designed a flat horizontal base plate with vertical posts where rings were placed with spacers between each to avoid the expected overlapping glow seam. The main problem was nonuniform heating from the center to the perimeter, since all parts were the same mass and size. The solution was to orient the load horizontally to align it with the horizontal radiation shields. The rack supporting the rings was circular with an open center. The main support allowed for horizontal posts projecting out on opposite sides of the center support so rings could be slid over the posts while retaining the spacers.
I recall a funny story early in the development when a small laboratory-size ionitrider was designed for experimentation and was sold to two gentlemen who planned on building a commercial enterprise for nitriding. In a rented garage in Iowa with a garden hose supplying cooling water in the evening after normal working hours, I was instructing the two guys and their wives on the operation using the EDAC. Three of the four looking over my shoulder were completely perplexed as I was populating the screen with temperature inputs, pressure, and so on. Suddenly one of the wives blurted out, “Hey! There’s nothing to this! It’s just like my microwave.” And from that beginning we have the rest of the story: Advanced Heat Treat in Waterloo, Iowa.
The moral of this story is this: When transferring technology, change as little as possible, because if do, you are doomed to repeat the evolutionary mistakes that the original design team experienced.