Climate change and fossil fuels are topics that can spur many lively conversations. In today’s Heat Treat Today Technical Tuesday feature, explore their connection as it relates to heating industrial furnaces in the future with Dr. Joachim G. Wüenning, president, WS Inc. and an expert in clean efficient combustion.
This article originally appeared in Heat Treat Today’s March 2020 Aerospace print edition.
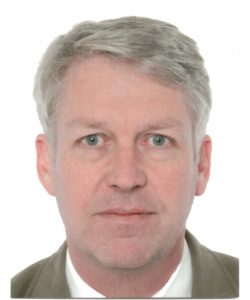
Many people view climate change as the biggest threat to mankind. Technical and social efforts will be required to meet the goals, formulated in the “Paris Climate Agreement,” to limit global warming to less than 35.6° F (2° C).
Combustion of fossil fuels is by far the largest human contribution to global warming. Fossil fuel-fired power plants and internal combustion engines are already in the public focus. The transformation to alternative drives for vehicles has just started, and the days of coal-fired power plants are numbered.
Combustion of fossil fuels for industrial furnaces is also a large contributor to greenhouse gases and air pollution. The industrial heating sector is not in the public focus yet, but that will change soon; therefore the topic should be addressed proactively.
For mid- to long-term future industrial process heating, there are three main scenarios:
- heating with renewable electricity, or
- heating with non-fossil fuels, or
- a combination of both.
Humans used non-fossil fuels for hundreds of thousands of years and are returning to that habit after a short period of about 250 years where fossil fuels were primarily used.
Reducing CO2 Now and In the Future
Heating a furnace using electricity is locally CO2 free, but an even greater amount of CO2 is emitted at power plants since the majority of electricity is generated by burning fossil fuels. For every kilowatt hour (kWh) produced, roughly one pound (~0.45kg) of CO2 is emitted into the atmosphere [1]. This is true for Germany, and the figures for the United States are in the same range.
Heating an industrial furnace with a typical temperature of around 1832°F (1000°C) with natural gas produces about 0.4kg CO2 for every kWh of available heat for a cold air burner, and less than 0.25kg/kWh CO2 when using a recuperative or regenerative burner where waste heat is recovered using a heat exchanger.
So, the short-term measure to reduce CO2 emissions is to use an efficient burner with heat recovery or to switch from electric to natural gas heating, which can cut CO2 emissions by 50% or more.
For a further reduction, we have to wait until electricity generation becomes predominantly regenerative, or we have to use green, non-fossil fuels. The possible paths to non-fossil heating of industrial furnaces are drafted in Figure 1. It shows that the short-term action should be improving the efficiency of burner systems or a switch from electric to gas heating. In the mid- to long-term future, there should be a healthy competition between non-fossil fuel gas and electricity, driving the prices for non-fossil energy down.
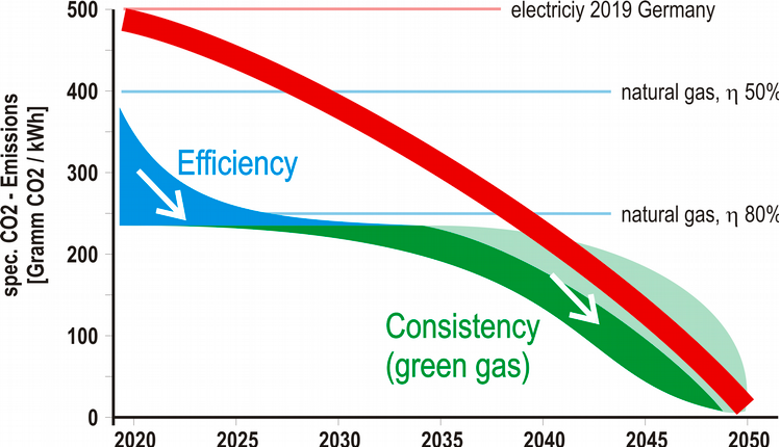
Changing Fuel Compositions
The most relevant characteristic for the interchangeability of fuel gases is the Wobbe Index (Figure 2), with the lower or upper heating value (Hi, Hs), the density of the fuel gas (r) and the density of dry air (r0). Fuel gases with the same temperature, pressure, and the same Wobbe Index will provide the same energy output from a burner. If the Wobbe Index is changing, the flow must be corrected by changing the fuel gas pressure or a flow throttle device to keep the burner power constant.

In most cases, the air does not need to be corrected since the ratio between stoichiometric air ratio and lower heating value is about 0.95 m3/kWh for common hydrocarbons. That means that a burner with a given heating power needs the same amount of air even when different fuel gases are used. A good rule of thumb is that one cubic meter per hour of air is required for every kilowatt of heating power.
If hydrogen is used as a fuel, about 15% less air is required. So, when hydrogen is added to natural gas and the fuel gas flow is corrected but the air flow is left unchanged, the system would be operated with somewhat more excess air, slightly less efficient but safe.
If gas fluctuations will occur in the future, adjusting the burners with more excess air would be an easy measure to ensure safe operation. With an effective heat recovery system and low exhaust gas temperatures, efficiency losses would be minimal.
Fuel Gases With High Hydrogen Content or Pure Hydrogen
The flame speed of hydrogen is much faster compared to hydrocarbons. That can cause some problems, especially in premixed burners where a flashback can occur. Another challenge resulting from faster combustion could be higher flame peak temperature leading to higher thermal NOx emissions. Modern low NOx methods are available to address this problem.
A positive effect of hydrogen can be a more reliable and easier ignition of burner systems. Many industrial burner systems can be operated with high percentages of hydrogen or with pure hydrogen with little or reasonable modifications.
Fuel Gases Containing Fuel Bound Nitrogen
Using ammonia or bio-gases with fuel bound nitrogen will produce excessive amounts of NOx-emissions when burned in most burner systems. There are a number of options to achieve low NOx-combustion with fuel bound nitrogen.
One method is fuel conditioning where fuel bound nitrogen is broken up into molecular nitrogen. This was successfully demonstrated using a stainless steel reactor in combination with a flameless oxidation burner system.[2] Another method would be exhaust gas cleaning by selective (SCR) or non-selective (SNCR) catalytic exhaust gas cleaning. Both processes require large investments and operating costs and should only be used if other options are not available.
The development of combustion systems with integrated treatment of fuel bound nitrogen would be the preferred method and will be an important topic for combustion research in the coming years. One approach is multi-stage flameless oxidation [3].
Fuel Conditioning
Fuel conditioning might be required to keep fuel gas properties within regulated limits inside the gas transport and distribution grid or for certain customers with special requirements. Fuel conditioning can be performed by blending different gases or by changing their compositions by using reformers or gas separation units like pressure swing adsorption (PSA) or membrane technology.
If future regulations propose a certain hydrogen content in the fuel gas grid, strategically placed steam reformers could keep the hydrogen content within certain ranges, even if there is no regenerative electricity available to operate electrolysers.
Reformers could also crack ammonia, ethanol, or methanol before being used as fuel gas to heat processes.
Outlook
There are several options towards non-electric, fossil-free industrial process heating. All these options have to be thoroughly investigated to keep a number of options open for future energy systems. The energy system of the future will be based on regenerative power generation but it will involve additional energy carriers to store and transport the energy. There are some challenges for combustion but there is no doubt that these can be overcome.
A fair and open competition between the different energy options will create the best solutions for society and the planet. A planned economy will not provide the fertile soil for innovations and entrepreneurship necessary to meet the challenges.
References
[1] German Environment Agency, CO2 Grid Emission Factors from 1990 – 2018 for the German Energy Mix, March 2019
[2] Domschke T., Becker C., Wüenning J.G., Thermal Use of Off‐Gases with High Ammonia Content – a Combination of Catalytic Cracking and Combustion, Chem. Eng. Technol., 21: 726-730
[3] Wüenning J., Multistage Flameless Oxidation, AFRC Combustion Symposium, Waikoloa, HI, September 2019
About the Author: Joachim G. Wüenning is president of WS Wärmeprozesstechnik GmbH and his area of expertise is in clean efficient combustion, FLOX—flameless oxidation, heat recovery, radiant tubes, and recuperative, regenerative burners. This article originally appeared in Heat Treat Today’s March 2020 Aerospace print edition.
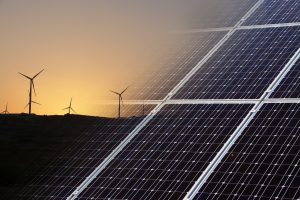