Source: Lindbergh/MPH
Reactive maintenance is expensive and usually requires downtime, holding up production. In contrast, preventive maintenance keeps these failures from occurring, which results in cost savings for manufacturers. Research shows that preventive maintenance can produce a 12 to 18 percent cost savings as opposed to other reactive maintenance programs.
In this Heat Treat Today Best of the Web feature, Lindbergh/MPH offers important preventative maintenance tips for heat treat furnaces.
Preventive maintenance is a list of regularly performed procedures that decreases the likelihood of a piece of equipment failing. It is performed by operators while the machine is in good working order. Regular maintenance also keeps equipment running at top performance and extends its life.
5 Preventive Maintenance Items for your Heat Treat Furnace
Heat treat furnaces are used in many manufacturing processes, including tempering, preheating, quenching, stress relieving, annealing, and more. Many factors, including high temperatures, place considerable wear and tear on the furnace components. Eventually this can cause bearings to flake, leaks to develop, and other problems to come up. Small issues can lead to mechanical failures over time that in turn lead to reactive maintenance.
Some common preventative maintenance services for heat treat furnaces include:
- Tuning Combustion Systems – Component wear, high temperatures, and other factors lead to burner settings drifting over time. This ultimately affects efficiency, fuel usage, emissions, and product quality. Tuning the combustion system maintains optimal performance and efficiency rates, limits excess emissions, and improves product quality.
- Bearing Inspections – Functional bearings are crucial to any machine, but even properly installed and operated bearings wear down over the course of time. The contact surfaces of bearings repeatedly withstand compressive loads, which eventually causes the surfaces to flake. Inadequate lubricant, improper lubricant type, breakage, wear, corrosion, and other factors can lead to bearing failure. A broken or seized bearing can stop equipment, potentially bringing the entire production line to a halt.
- Leak Testing – Even the smallest leak can reduce production performance and possibly result in system failure. Preventive maintenance for leaks includes testing gas shutoff valves and gas train piping for leakage.
- Lining Inspections – Gradually the lining of a heat treat furnace may succumb to chipping, cracking, or bubbling. Disruptions to the integrity of the lining, left unchecked, can lead to contamination that harms the quality of the product. Lining inspections prevent contamination.
- Safety and NFPA Testing – Safety and National Fire Protection Association (NFPA) testing protects clients from potential damage. It also ensures that preventive measures against workplace accidents are in place.
Read more, The Benefits of Preventive Maintenance
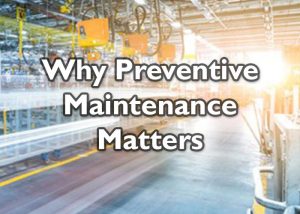