Time for a solid case study. In this Heat Treat Today Technical Tuesday feature, José P. Sanchez, part of Ceramics Business Unit in Nutec Bickley, describes the installation of several high-temperature and low-temperature ovens and kilns at one of the largest plants of a worldwide refractory product manufacturer.
Read this Original Content piece to get the details about how this project was executed and what measures were implemented for successful follow-up service.
About the Client
The client is recognized worldwide for the manufacture of refractory products used in the steel industry and on this project we worked with one of its largest plants.
This project comprised the design, manufacture and installation of 13 ovens and two kilns with temperatures ranging from 390°F to 3,000°F (200°C to 1,650°C) and retrofits to two existing kilns, as part of a major redesign at the client’s plant.
The Challenge
Nutec Bickley had to design, manufacture/modify and install 17 ovens / kilns in the space of 12 months, so we had to be especially careful organizing ourselves in the following aspects:
- Ensuring we had the required space in our plant for the pre-assembly of all these units
- Coordinating the execution of the project in which more than 80 people participated directly
- Coordinating the parallel installation of multiple pieces of equipment in the customer’s plant, where at times there were more than 30 of our personnel on site at the same time
Our Solution
One of the decisive factors in winning this contract was the fact that other suppliers only had the capacity to manufacture either low temperature ovens or high temperature kilns, with Nutec Bickley being the only one with the capacity to manufacture both.
Additionally, we demonstrated our experience and ability to design ovens/kilns in temperature ranges from 210°F right up to 3,270°F (100°C to 1,800°C).
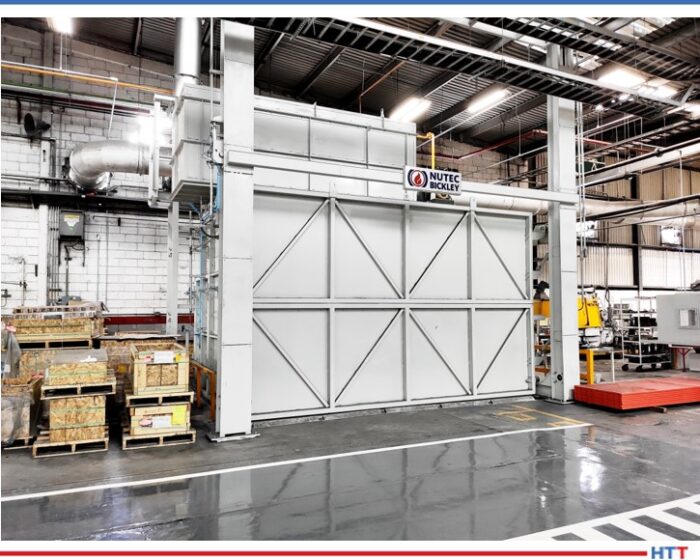
We offered an ideal option, enabling the client to take on a single supplier to supply all of this equipment and to have it delivered it as a turnkey project.
Equipment Supplied
The turnkey solution comprised the following equipment and technologies:
A high temperature convection oven (1,110°F/600°C) with nitrogen injection
- Equipped with stainless steel baffles to direct gases into the chamber and achieve the required temperature uniformity
- Equipped with a thermal incinerator to reduce VOCs
Two Carbell Kilns
- Operating temperature: 1,600°C (2,910°F)
- Maximum operating temperature of 1,700°C (3,090°F)
- Nine temperature control zones
- High alumina bubble brick insulation
- High velocity burners
- Ceramic fiber lined exhaust vent
- Incinerators in the exhaust for volatile gases
Two Retrofits of Existing Equipment
A) Modification of a Carbell kiln from another plant
- We renewed the MCC and control panels.
- We updated the PLC and display.
- The combustion system was modified to comply with the NFPA-86 standard.
B) Transfer of a kiln from another plant
- Insulation was supplied using our Jointless system.
- Updated to meet NFPA-86 standard
12 Low-Temperature Convection Ovens (390°F to 660°F/200°C to 350°C)
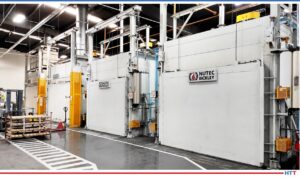
- Two of them with forced cooling using extractors
- Two of them with an incinerator to burn the volatile gases being vented to the atmosphere, greatly reducing pollution emissions
- The other equipment was adapted to install more incinerators in the future.
- Steel paneled ovens and mineral wool insulation
- Design of baffles to direct gases into the chamber and achieve the required temperature uniformity
Project Benefits
- Provided a comprehensive solution in the agreed timescale
- Optimization of the use of floor space and improvements in operational logistics
- SCADA system to monitor the uniformity of temperature in each cycle
- Alarms in the event of sub-optimal temperature or where there is some discrepancy in the heating zones
- Higher process quality and traceability in the case of rejects
- Using some equipment from other plants reduced investment costs
- Quickly service the 17 new, as well as the other, equipment
- HSE supervisors in the field to monitor the operations of our mechanics and electricians
- Knowledge to follow any type of safety standard in the design of combustion equipment. In this case it was NFPA 86-2019 (Class A oven and furnace design).
- Opened our facilities at Nutec Bickley for visits to review progress of the oven manufacture
About the Author: José P. Sanchez is part of the Ceramics Business Unit in Nutec Bickley, in charge of sales in LATAM for kilns and major retrofits in the ceramic industry. He has been an active participant of multiple projects involving kilns and ovens in numerous industrial sectors, mostly refractories for the steel & aluminum industry.