Heat Treat Today publishes eight print magazines a year, and included in each is a letter from the editor, Bethany Leone. This letter first appeared in the May 2023 Sustainable Heat Treat Technologies print edition.
Feel free to contact Bethany at bethany@heattreattoday.com if you have a question or comment.
In order to create a more sustainable future for heat treaters, operators may be looking to “digitalization” as an immediate step for their heat treat systems. Digitalization is an amorphous term that can describe a few things.
One definition of digitalization curated for the heat treat industry is: the integration of advanced digital technologies (like cloud technologies, 3D visualization, simulation, analytics and collaboration tools, and even robotics) with heat treat equipment and all other aspects of production (order fulfillment, certifications, communication systems, etc.) to create a “digital twin” — that is, a holistic virtual representation of heat treat operations. By transitioning analog data and manual operations to a digital system, the end goal of creating a “digital twin” of all heat treat operations can be actualized, allowing heat treaters to monitor and analyze in real-time and create simulations and predictions about equipment performance.
This term tends to be broader than just “digitization” — the act of digitizing analog technologies to digital form — though the two terms are often used interchangeably.
An interest in digitalization makes a lot of sense. For one, updating manufacturing plants with digital practices is a huge draw for young people: “People want to work for a technologically advanced company that they can feel good about,” according to Josh Hale, managing recruiter at International Search Partners, when he spoke on Heat Treat Radio . Additionally, Covid-19 labor constraints accelerated adoption of IIoT (industrial internet of things) technologies — digitalization being just one of many. But there are also several intrinsic promises that digitalization has to offer manufacturers, for example:
- Efficiency: creating efficient operations that streamline business processes
- Accuracy: increasing accuracy by achieving precise control over temperature, atmosphere, and other process parameters
- Data and Analytics: real-time monitoring/data collection and rapid data analysis
- Safety: reduced need for manual interventions, thus avoiding accidents and improving operator safety
From a sustainability perspective, digitalization means heat treaters can monitor, analyze, predict, test, and adapt energy efficiencies in their operations. This magazine features a conversation with experts in heat treat with an eye for energy, and they’ve commented on this specific topic. “With higher computational capacity on the controllers on a per furnace basis,” John Clarke, technical director at Helios Electric Corporation notes, “we have the ability to start executing real-time analysis on the furnace and potentially implement a thermodynamic model of the furnace and how it’s operating.” Several representatives from Watlow illustrate this point: “Poor thermal uniformity can lead to scrap and rework of material, which both result in excess energy consumption.” Read the eight-page conversation with six international expert contributors on page 19.
But there are drawbacks to adopting this new technology, and in the midst of all of this “good,” I do wonder how difficult this transition has been — or can be — for some in-house heat treaters. Challenges when considering this technology include:
- Initial Investment. The initial investment in new technology is always present, and so is the question of who will “dish out the dough.” Will the furnace supplier try to absorb upgrading expenses? Or does it fall to the end-user buying the furnace or upgrade?
- Operational Complexity. However easy to operate a technology is now, it was not always the case. I once thought typing at a computer was the most difficult thing in the world. Now, I’m so familiar with a keyboard that I can look over at my husband texting on his phone and know (to a degree) the message he is typing, just by watching his thumb position. What skills does your team have to learn a new system? How much time will it take to train 50%–75% of them? How long until you feel confident in the process?
- Overdependence on Technology. We depend on digital technologies for many things (thank you, alarm clocks!), but is the level of dependence compromising something valuable? And to what degree? When it comes to cybersecurity threats, for example, what type of dependence on technology exposes you to more risk versus fortifying your internal systems?
The promises and challenges of digitalization will continue to face-off in offices and plant floors. While the boundary line of digital acceptance may shift, this new frontier towards creating “a holistic virtual representation of heat treat operations” means new technologies and processes that will be tested and adopted by heat treat pioneers, possibly you.
As with any frontier, there are known and unknown dangers. Let us know how your company is considering digitalization and what opportunities are golden nuggets or simply fool’s gold: editor@heattreattoday.com.
Special thanks to Mike Löpke (head of software & digitalization at Nitrex Metal) and Jeffrey Halonen (CEO of Steelhead Technologies) for their insights.
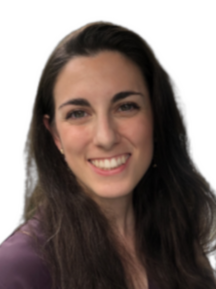
Contact Bethany Leone at bethany@heattreattoday.com.