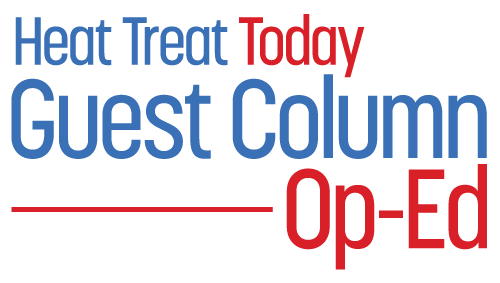
As heat treaters strive for a sustainable future, pressure mounts to make the right choices while running commercially viable operations. In this Technical Tuesday installment of a continuing series, guest columnist Michael Mouilleseaux, general manager at Erie Steel, Ltd., explores the potential ramifications of the DOE effort for industrial decarbonization in the heat treating industry. The first installment, “US DOE Strategy Affects Heat Treaters”, appeared on April 10, 2024, in Heat Treat Today, as well as in Heat TreatToday’s March 2024 Aerospace print edition.
This informative piece was first released in Heat Treat Today’s May 2024 Sustainability Heat Treat print edition.
As regulatory agencies set industrial decarbonization goals aimed at achieving net zero greenhouse gas emissions (GHGE) by 2050, heat treaters should prepare for action. But where do heat treatment technologies stand today, and what is the path going forward?
Background
President Biden’s 2021 executive order calling for a “clean energy economy” led the U.S. Department of Energy (DOE) and the Environmental Protection Agency (EPA) to develop “The Industrial Decarbonization Roadmap,” a strategic plan for reducing industrial emissions. The plan identified five sectors — chemical, petroleum, iron and steel, cement, and food and beverage production — as targets for mitigation efforts. According to “The Roadmap,” process heating operations within these five industries represent the greatest opportunity to apply what were established as four pillar technologies:
- Energy efficiency
- Low carbon fuels, feedstocks, and energy sources (LCFFES)
- Carbon capture, utilization, and storage (CCUS)
- Industrial electrification using green electricity
In May 2023, heat treating was specifically named as a target process for reducing GHGE during the DOE’s Office of Energy Efficiency & Renewable Energy’s Low Carbon Process Heating Forum.
A Closer Look at the Technology Pillars
To determine the path forward, it’s important to understand where heat treatment technology stands today regarding the four pillars.
Energy Efficiency: Among energy efficiency opportunities are furnace insulation, controls, and burner design. According to furnace and controls manufacturers that I have spoken with, advancements in insulation and heating system controls offer less than a 20% opportunity in efficiency improvement over
LCFFES: In the U.S., the primary hydrocarbon fuel for heat treating is natural gas, which has an average (commodity) cost of $2.57/MMBTU. Hydrogen has been endorsed as the preferred replacement. Hydrogen manufacturing and distribution issues aside, hydrogen has a 2023 (commodity) cost ranging from $14.00 to $40.00 per MMBTU, and a carbon footprint of 30–130% that of natural gas. “Green hydrogen” is “under development.”
CCUS: Carbon capture, utilization, and storage is currently relegated to natural gas production operations where the captured CO2 is injected into existing wells to “enhance” production. Although the DOE suggests development of advanced CO2 capture technologies are still underway, a 2023 Congressional Budget Office report states there are “fifteen CCS facilities . . . operating in the United States . . . [with] an additional 121 . . . in development.” It is fair to state there are no CCS (carbon capture and storage) facilities currently operating on the scale of a heat treating operation.
Electrification: For electrification to be impactful, electricity must be generated via green sources. Currently, 40% of the electricity generated in the U.S. comes from natural gas, 20% from coal, 19% from nuclear, 10% from wind, and 3% from solar. It is my opinion that, regardless of the incentives federal and state governments offer wind and solar energy operations, they will not reach the scale — and most certainly not the reliability — necessary to achieve the stated 2035 GHGE goals.
Cost also must be considered. The average U.S. cost for electricity was $0.086/KWH in 2023. In California, however, the cost for electricity generated with 40% renewables was $0.1819/KWH. In Germany, it was $0.289/KWH with 55% renewables. To put this into perspective, today the differential in (industrial) electricity (commodity) costs demonstrably increase as the percentage of that electricity is generated by “green” sources. To think that this trend is going to be reversed by federal mandate is paradoxical.
A Realistic Look at the “Road Map”
While industrial decarbonization targets called for an 85% reduction in GHGE by 2023 and net zero by 2050, the goals seem unreachable using currently available technology. Replacing natural gas with hydrogen will result in significant cost increases as the commodity is 5–15 times more expensive, the equipment will require retrofitting to accommodate hydrogen, and the national infrastructure will need to be modified for hydrogen.
Electrification of existing gas-fired processes will result in a cost increase of four times, according to DOE estimates; however, based on today’s cost trends, 7–9 times higher is more likely. Additionally, the cost of converting equipment to electric operation must be considered. Mitigation efforts suggested by the DOE include improvements in efficiency that rely on yet-to-be-developed technologies and cost reductions in electricity facilitated by the wholesale use of renewable energy.
Overall, decarbonization efforts are noble. The timeframe and methodology, however, are unrealistic as they are based on the use of still-conceptual technologies.
What Can Heat Treaters Do?
Following the lead of the automotive industry may be key. This sector reacted to the government mandates for GHGE reductions by going all in for electrification — with projections of 50% electric vehicles by 2030. A funny thing happened; these vehicles were not wholly accepted by the American public. The auto industry, led by the dealers, with the support of the UAW, and the car manufacturers petitioned their U.S. Representatives to “pause” these requirements. This political pressure caused the EPA to roll-back the implementation schedule.
Heat treaters must act now with a similar effort, but it must be aimed at preventing the promulgation of regulations that rely on still-conceptual technologies within an unachievable timeframe. Contact your local government leaders; let them know what we do means jobs and tax revenues. Contact your U.S. Representatives and Senators to let them know heat treaters are critical to our national security, the transportation system, and, in fact, the infrastructure of this country. What we do should not be outsourced, and we need to be given all the considerations of a critical industry.
The next column in this series will address the role of process heating in GHGE, analyze DOE assessments of GHGE for industry and process heating operations, and propose a fact sheet intended for use in our effort to set a realistic timeline for decarbonization goals In the next column, we’ll address potential ramifications of the DOE effort for industrial decarbonization in the heat treating industry to help you be better informed and prepared.
About the Author:

Michael Mouilleseaux is general manager at Erie Steel, Ltd. He has been at Erie Steel in Toledo, OH since 2006 with previous metallurgical experience at New Process Gear in Syracuse, NY, and as the director of Technology in Marketing at FPM Heat Treating LLC in Elk Grove, IL. Michael attended the stakeholder meetings at the May 2023 symposium hosted by the U.S. DOE’s Office of Energy Efficiency & Renewable Energy.
For more information: Contact Michael at mmouilleseaux@erie.com.
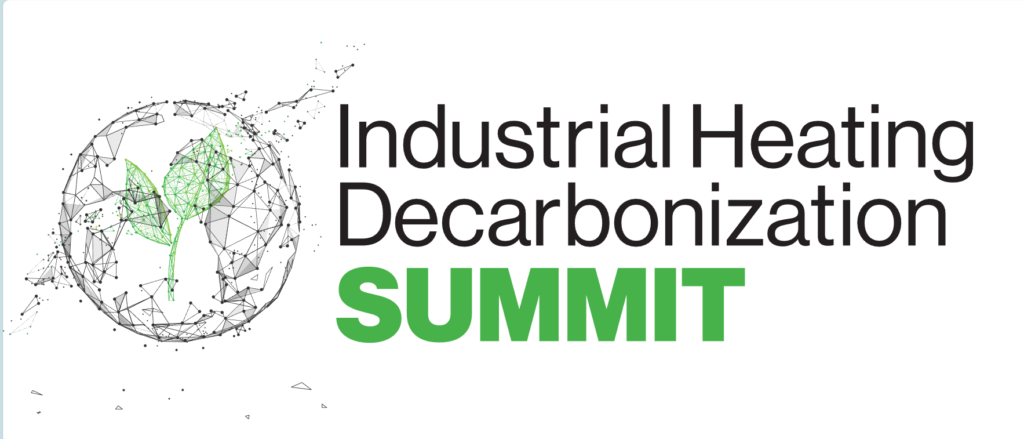