What is the path forward for thermal loop systems, and how is “sustainability” at the forefront of this technology? The following article is co-authored by Peter Sherwin, global business development manager of Heat Treatment, and Thomas Ruecker, senior development manager, at Watlow. They examine four scopes to take into consideration when assessing thermal loop systems in the context of greenhouse gas emissions and their environmental impact.
This article is a continuation from the introduction of this topic released in Heat Treat Today’s January/February 2024 Air & Atmospheres print edition and published at Heat Treat Today on February 27, 2024, titled “Thermal Loop Solutions, Part 1: A Path to Improved Performance and Compliance in Heat Treatment”.
Sustainability
Heat treatment thermal loop solutions provide several sustainability benefits, including reduced energy consumption and waste. The power controller regulates the power output to minimize energy waste, and the possible integration with renewable energy sources and circular economy principles provides a complete power solution that spans from element design to recycling and renewables. The thermal loop solutions, in combination with insulation design and materials, provide energy-efficient solutions that contribute to sustainability and reduce the environmental impact of heat treatment processes.
When discussing these systems in the context of greenhouse gas emissions and their environmental impact, it is essential to consider Scopes 1, 2, and 3, as well as the less common Scope 4:
- Scope 1 (Direct Emissions): Heat treatment processes often involve the combustion of fossil fuels like natural gas, propane, or oil to generate heat. These direct emissions are attributed to the equipment used in the heat treatment process, such as furnaces and ovens. Efforts to reduce Scope 1 emissions include upgrading to more efficient equipment or adopting alternative heating technologies, like induction or electric heating systems.
- Scope 2 (Indirect Emissions from Energy): In heat treatment processes and thermal loop systems, electricity is often used to power various components, such as pumps, fans, and control systems. The emissions associated with generating this electricity are considered Scope 2 emissions. To reduce Scope 2 emissions, companies can improve energy efficiency, invest in renewable energy sources, or purchase green energy from their utility provider.
- Scope 3 (Other Indirect Emissions): These emissions are associated with activities throughout the value chain of heat treatment applications and thermal loop systems, such as the manufacturing and transporting of raw materials, equipment, and waste management. Companies can work to reduce Scope 3 emissions by collaborating with suppliers to improve the environmental performance of their products and services, optimizing transportation and logistics, and implementing waste reduction strategies.
- Scope 4 (Avoided Emissions): In heat treatment applications and thermal loop systems, avoided emissions may come from implementing energy-efficient technologies, waste heat recovery systems, or other innovative solutions that reduce overall energy consumption and associated emissions. By quantifying these avoided emissions, companies can showcase the positive impact of their sustainability efforts on reducing their carbon footprint. Avoided emissions can also be highlighted when subcontracting heat treatment requirements to a more energy-efficient source rather than running an in-house operation. In this approach, the heat treatment process is outsourced to an external, specialized heat treatment service provider, especially if the in-house equipment is due to be lightly utilized. These service providers operate independent heat treatment facilities and offer services to multiple clients across various industries and generally run 24/7 with high utilization.
At the component level, energy savings can be realized using current technology. Advanced SCRs provide predictive load management functions and hybrid firing algorithms and contribute to sustainability by optimizing the energy usage of heat treatment processes. These SCRs offer real-time monitoring and control of energy consumption, while predictive load management systems use specific algorithms to manage peak power loads and adjust to optimize for local conditions (load shedding or load sharing). Hybrid firing systems use a combination of firing methods to control power factors and reduce the negative impact on the electrical infrastructure.
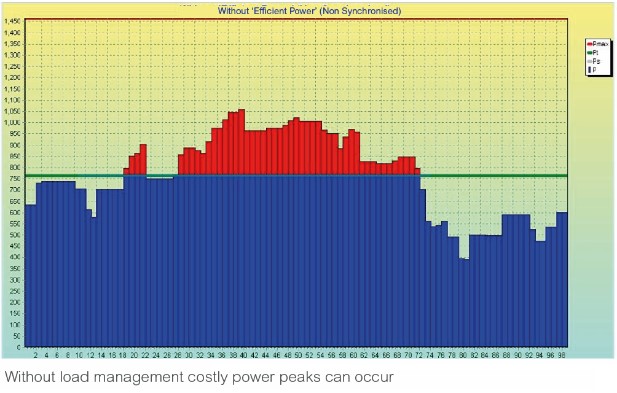

Heater design is also essential. Switching time impacts heater life with fast, modern switching modes (hybrid firing) significantly extending heater life compared to slower switching from conventional mechanical contactors.
Systems can be rapidly tested, simulated, and modeled through computational engineering. Several thermal loop systems today have improved temperature uniformity due to these methods.
Adaptive thermal system (ATS) solutions are the next frontier of thermal loop solutions. Rather than selecting the best-of-breed components — sometimes with overlapping functionality and kitting a complete solution — ATS provides a merged design between heater and control systems. ATS is already in place in several semiconductor applications, and this type of technology is looking to scale into heat treatment applications shortly.

Source: Watlow
Challenges and Limitations
The initial investment in heat treatment thermal loop solutions can sometimes be higher than in traditional methods. However, this investment often leads to a significantly lower total cost of ownership and improved return on investment due to the thermal loop solutions’ increased efficiency, improved quality control, and extended life.
Ensuring regulatory compliance is complex and time-consuming, requiring organizations to have the right people, processes, and equipment.
Future Trends
As Industry 4.0 and digital transformation continue to gain momentum and Industry 5.0 practices are implemented, heat treatment thermal loop solutions will become increasingly important. Integrating digital technology and machine learning algorithms will provide even greater control, traceability, and transparency, enabling organizations to make informed decisions based on real-time data and predictive analytics. In addition, as new materials and manufacturing processes are developed, adaptive and flexible heat treatment thermal loop solutions will need to evolve to meet these challenges and provide the necessary level of control and efficiency for these new applications.
Conclusion
Heat treatment thermal loop solutions provide several benefits over traditional heat treatment methods, including improved temperature control, increased efficiency, and improved sustainability outcomes. The integration with Industry 4.0 and data management systems, as well as the use of FMEA and OEE metrics, further help enhance the performance of heat treatment processes. As Industry 4.0 digital transformation and Industry 5.0 practices continue to evolve, heat treatment thermal loop solutions will play an increasingly important role in the future of heat treatment.
About the Authors:

Global Business Development Manager of Heat Treatment
Watlow

Senior Business Development Manager
of Heat Treatment
Eurotherm, a Watlow company
Peter Sherwin, global business development manager of Heat Treatment at Watlow, is passionate about offering best-in-class solutions to the heat treatment industry. He is a chartered engineer and a recognized expert in heat treatment control and data solutions.
Thomas Ruecker is the business development manager of Heat Treatment at Eurotherm Germany, a Watlow company. His expertise includes concept development for the automation of heat treatment plants, with a focus on aerospace and automotive industry according to existing regulations (AMS2750, CQI-9).
For more information: Contact peter.sherwin@watlow.com or thomas.ruecker@watlow.com.
This article content is used with permission by Heat Treat Today’s media partner heat processing, which published this article in 2023.