Despite years of research and development that resulted in several important technological innovations, the constraints of high-pressure gas quenching are ever more evident. In today’s Technical Tuesday, Robert Hill, FASM president of Solar Atmospheres of Western PA, addresses the creation of a new, robust style of vacuum oil quench furnace. The results challenge the schematics in how the next generation of oil quench furnaces should be designed, built, and operated.
This informative piece was first released in Heat Treat Today’s November 2024 Vacuum print edition.
Introduction
After decades of research and development that resulted in several important technological innovations, the constraints of high-pressure gas quenching are ever more evident. Gas cooling runs into efficacy issues when compared to liquid quenchant cooling, chiefly for heavier cross sections. This stays true even when using specialized inert gas blends and heightened gas pressures.
Additionally, it is undeniable that stringent liquid quench Aerospace Material Specifications (AMS) standards for certain aerospace alloy steels will never change. In fact, many industry standards (e.g., SAE/AMS and U.S. defense standards) and client specifications often mandate oil quenching of alloys or component parts.
To meet the demand for an effective, sustainable liquid quench solution, Solar Manufacturing with Solar Atmospheres engineers worked through the tumultuous period of the pandemic to create a new, robust style of vacuum oil quench furnace. Their work culminated in a vacuum oil quench furnace with a 36″ x 36″ x 48″ hot zone that operates up to 2000°F and can accommodate a weight capacity of 2000 lbs. With high uptime reliability and excellent metallurgical results, the NEO™ represents a paradigm shift in how the next generation of oil quench furnaces should be designed, built, and operated.

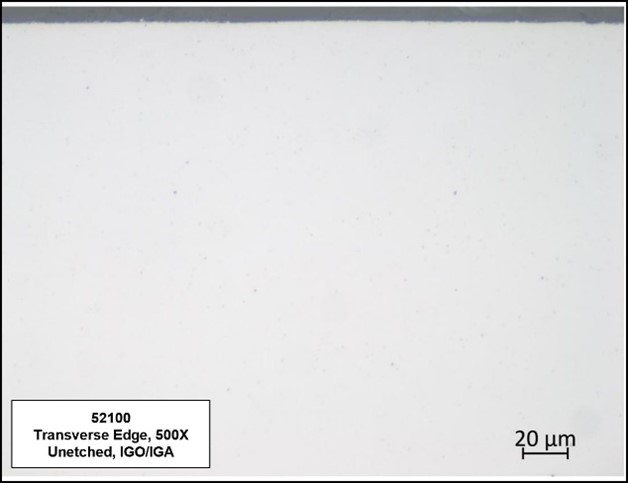
Rigorous Design for Metallurgical Excellence
The next generation of oil quench furnaces heralds an era of metallurgical excellence. This is made apparent across three key measures: control over surface contamination, prevention of parts cracking, and flexible processing of dissimilar materials.
No Surface Contamination
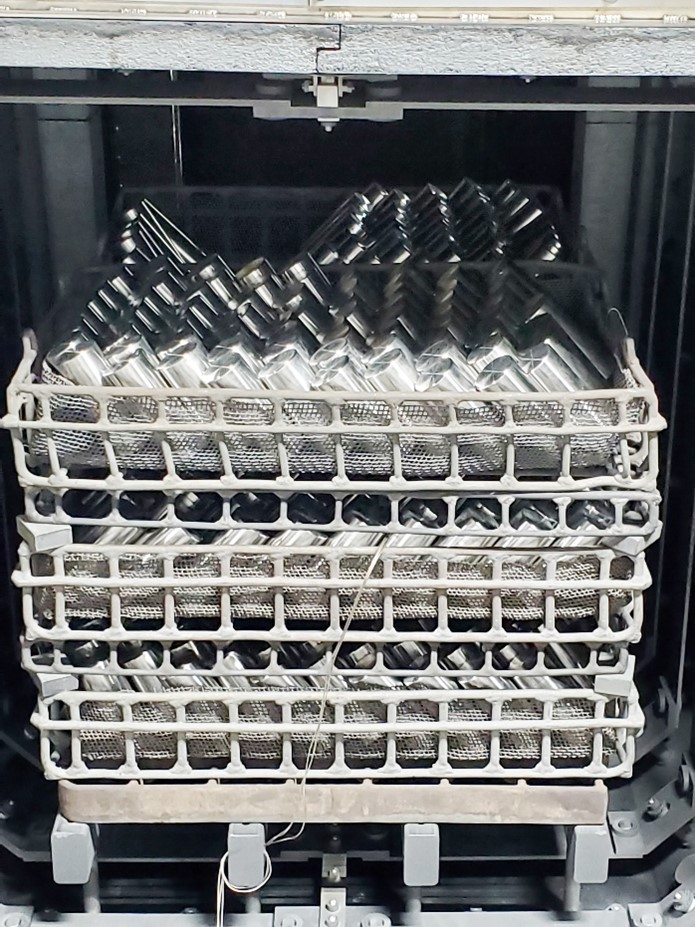
Source: Solar Atmospheres of Western PA
By implementing a vacuum design to the oil quench furnace, the research team avoided issues faced by traditional atmosphere oil quench furnaces, such as surface contamination and intergranular oxidation/intergranular attack (IGO/IGA). Additionally, they meticulously addressed design concerns regarding oil backstreaming in the new multichambered vacuum system. After two years of usage, the hot zone has remained pristine and oil-free.
By effectively removing the possibility of any surface contamination, both IGO and decarburized or carburized surfaces on oil quenched components are eliminated. These critical metallurgical features are unattainable in traditional gas-fired Endothermic batch furnace equipment.
Precision Prevents Part Cracking
To eliminate the potential of part cracking, quench oil temperatures should be able to be maintained between 140°F to 180°F ±5°F, which enhances consistent and repeatable metallurgical results. Furthermore, having the furnace designed so that quench oil recirculates within a closed loop oil to air cooling system keeps water contamination from infiltrating the oil.
No Carbon Content Matching
The next generation of vacuum oil quench furnaces should also have highly controllable atmospheres, devoid of oxygen, which will remove the need to mechanism, which has demonstrated flawless performance for over two years.
Additionally, it is imperative that these furnaces be capable of using more conventional quench oil. A good quench needs excellent vapor pressure, powerful enough to allow the oil to vaporize. Furnaces can be designed with this in mind, allowing operators to save costs by using more conventional quench oils. For example, after rigorous laboratory experimentation into the vaporization of various quench oils at different pressures and temperatures, it was decided to purchase 3000 gallons of Houghton G quench oil, versus the “vacuum only” quench oils that are currently on the market today.
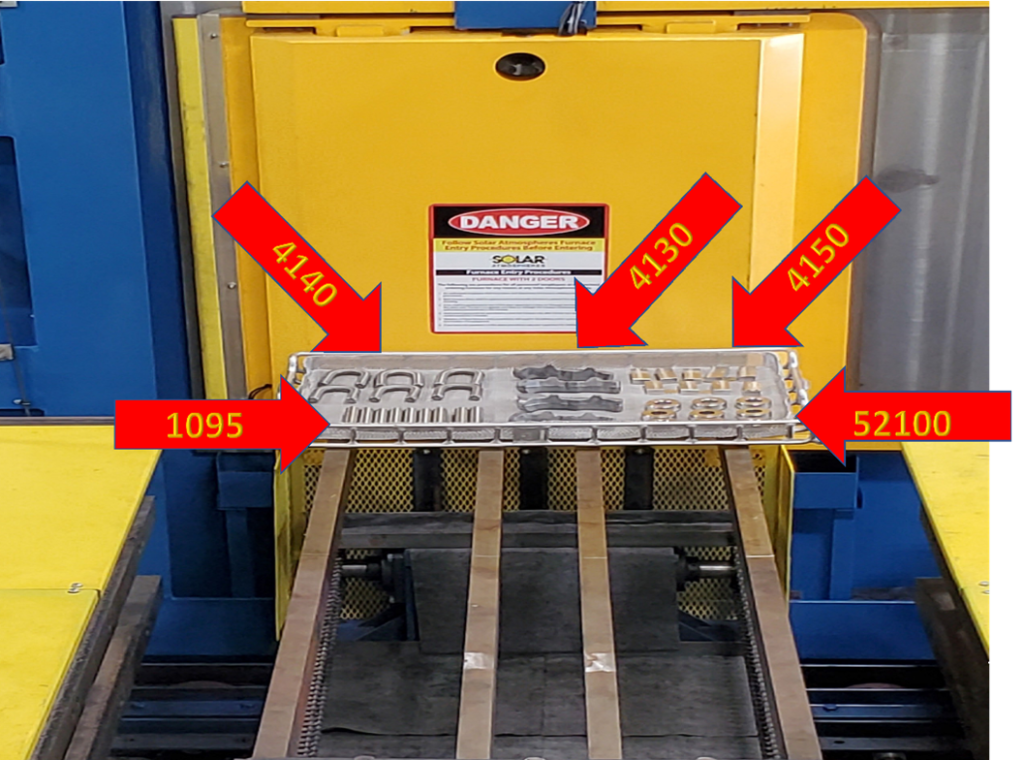
Source: Solar Atmospheres of Western PA
The next generation of oil quench furnaces should also finally provide metallurgical and quality engineers the ability to thermocouple the oil quenched parts in accordance with AMS2750 Rev H standards. Being able to monitor part temperature with up to twelve (12) data points, as defined by the latest AMS2750 revision, ensures thorough and precise thermocouple monitoring, bolstering control and repeatability.
Lastly, in a hermetically sealed furnace, another layer of control should be established through installing an internal camera. With “eyes” into the furnace, the operator will be able to watch the load transfer in real time from a control panel.
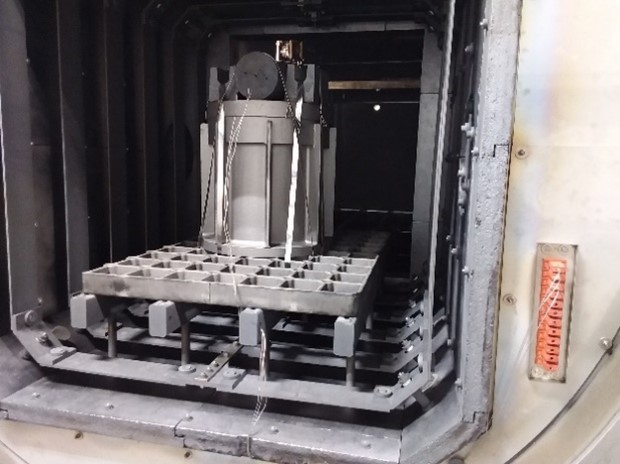
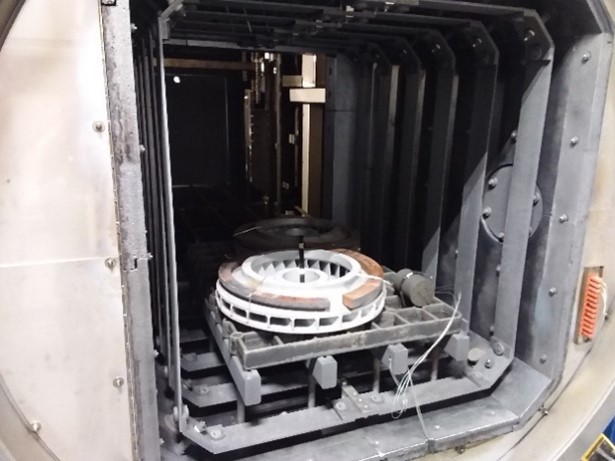
These operational attributes are on full display in the example of an automated austenitized cycle: At the completion of the cycle, the specially-designed transfer mechanism delivers precisely heated parts from the hot zone to the 3000-gallon oil quench chamber consistently within 20 seconds — all without the expulsion of flames and the discharge of smoke.
Oil flames and smoke are no longer acceptable realities in heat treatment operations. Unfortunately, the heat treating industry has been misled in the belief that a catastrophic disaster will never happen to them. There have been multiple “total losses,” mostly due to oil quench fires and explosions. Recently, it is well known that if an insurance adjuster sights a flame or smoke within a plant, they are reluctant or may even refuse to write the policy.
Vacuum furnaces offer a safe, contained alternative to the harmful open emissions and dangerous working conditions. For operations where the safety and the well being of the workforce are paramount, vacuum furnaces eliminate the risks associated with open flame exposure, explosivity, and skin burns.
Yet the next generation of vacuum oil quench furnaces should also open at both ends at the end of a cycle to expose it to atmosphere. Full air exchange mitigates the potential hazards of confined spaces.
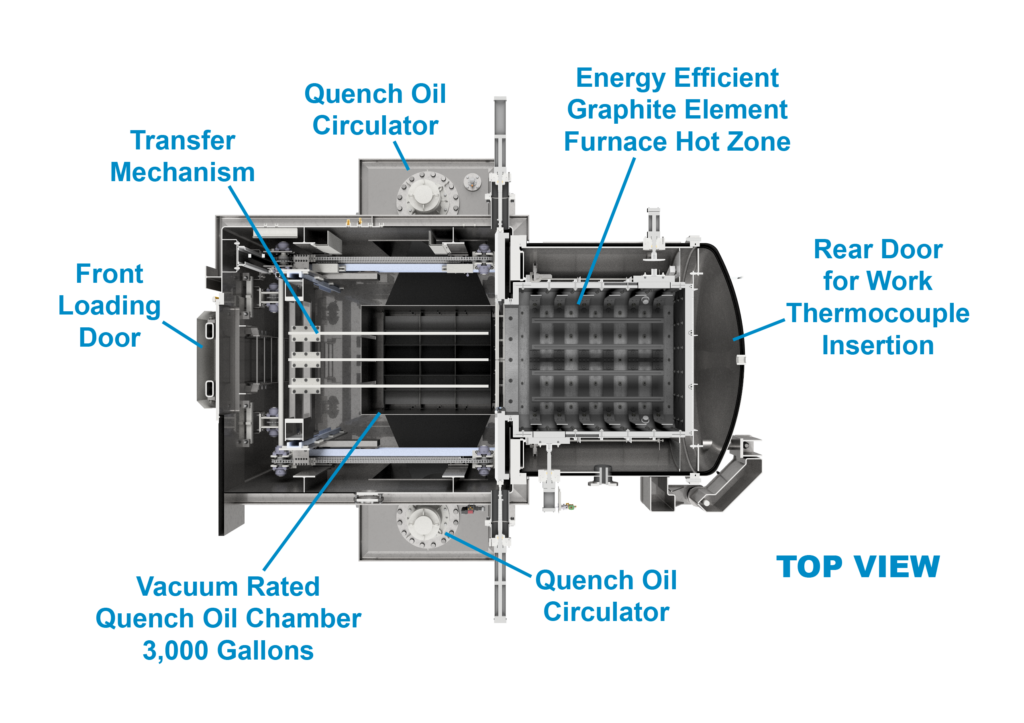
Source: Solar Atmospheres of Western PA
Meeting Environmental Demands
With ever more stringent environmental regulations, the next generation of vacuum oil quench furnaces will play a pivotal role in reducing the carbon footprint of the heat treating industry. It has been estimated that 80% of fuel used for heat treatment could be replaced by electricity, thus drastically reducing CO2 emissions: “When you burn something that contains carbon, you get carbon dioxide that you either must take care of or release into the atmosphere. With electric heating, you do not have any exhaust.”
The second column in the chart on page 30 addresses the multiple environmental concerns associated with traditional batch IQ gas-fired oil quenching furnaces. The third column outlines the advantages of the design for the next generation of oil quench furnaces, which embraces electric heating as a sustainable alternative to fossil fuels. As sustainability pressures continue to mount, governments, clients, and primes alike will continue to flow down requirements on how heat treaters plan to reduce their carbon footprints.

Source: The Monty
Conclusion
As the demands for metallurgical precision, safety, and environmental sustainability continue to mount, Solar’s new vacuum oil quench furnace emerges as a representative of the next generation of vacuum oil quenching technology. Characterized by unparalleled efficiency, precision, and sustainability, such furnaces will continue to lead the industry toward a future defined by cleanliness, safety, and environmental stewardship.

Source: Solar Atmospheres of Western PA
References
Kanthal, “Heat Treatment CO2 Emissions cut by 50 percent by using electricity” (April 2019), https://www.kanthal.com/en/knowledge-hub/inspiring-stories/heat-treatment-co2-emissions-cut-by-50-percent-by-using-electricity/.
Aichelin Group, “CO2 Footprints and the Heat Treat Industry,” The Monty (January 2024).
About the Author:
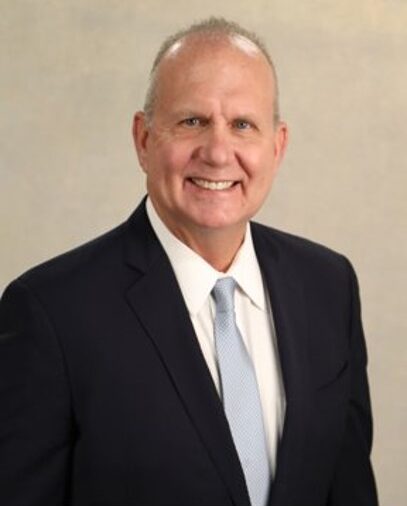
President
Solar Atmospheres of Western PA
Solar Atmospheres of Western PA
Robert Hill, FASM, began his career with Solar Atmospheres in 1995 at the headquarters plant in Souderton, PA. In 2000, Hill was assigned the responsibility of starting the second plant in Hermitage, PA, where he has specialized in the development of large furnace technology and titanium processing capabilities. Additionally, he was awarded the prestigious Titanium Achievement Award in 2009 by the International Titanium Association.
For more information: Contact Robert at bob@solaratm.com.