Maintaining clear communication for high precision processing, critical with medical component heat treating, requires sophisticated operations. In today’s Technical Tuesday, Mike Grande, vice president of Sales at Wisconsin Oven Corporation, provides an overview of how the industrial internet of things (IIoT) advances heat treat performance capabilities and ensures accurate, repeatable results.
This informative piece was first released in Heat Treat Today’s December 2024 Medical & Energy Heat Treat print edition.
Today’s technology is evolving at an exponential rate. Over the last several years, digital technology has provided more and more connectivity between devices and processes. One of the most impactful is IoT technology. From smartphones to virtual assistants, touchscreen refrigerators to thermostats and interconnected home management systems, these products are quickly changing the way people interact and connect.
In addition to consumer products, the industrial world is also seeing increased reliance on this technology to improve throughput, decrease energy use, and increase equipment longevity by capturing and analyzing the data generated by their machines.
What Is IoT and IIoT Technology?
IoT (internet of things) refers to everyday items that have been equipped with sensors that transfer data over a network. Refrigerators, lights, thermostats, smart speakers, and entire homes are now available with IoT technology. Devices equipped with IoT options provide conveniences like remote monitoring, advanced programming, and smart learning, which make daily and household tasks easier. What seemed like science fiction just a few years ago has become reality.
This impressive technology does not only apply to the consumer world. The application of IoT to the manufacturing sector is even more impactful. Industrial internet of things (IIoT) is the term used to describe the application of connected IoT technology to industrial machinery. These systems collect and analyze data, learn from that data (“machine learning”), perform predictive maintenance, and then share that information with personnel, manufacturers, including manufacturers of the machines being monitored, and even other devices. This type of data collection and analysis gives valuable insight into the facilities, processes, and equipment to ensure that everything from energy usage in a facility to equipment performance for a process is optimized.

Source: Wisconsin Oven Corporation
How Is IIoT Used in Industrial Ovens and Furnaces?
IIoT technology tracks the performance and health of the most critical components and conditions in the ovens and furnaces they are monitoring. The system utilizes an IoT gateway (Figure 1), which collects information from predictive maintenance sensors that gathers performance data and stores it over time. The gateway also wirelessly transmits the data to a cloud platform where it can be displayed in dashboards, designed for easy viewing and monitoring. Thresholds are set at warning or alarm conditions. When exceeded, the system alerts the user or the oven manufacturer that there is a problem. This type of system predicts component failures before they occur, allowing time to schedule maintenance and minimize unplanned downtime.

Source: Wisconsin Oven Corporation
The data is displayed in a dashboard format (Figure 2) which permits visual analysis of the information, and intuitive understanding of the process being performed in the oven. In the example of an oven used to process parts in an inert atmosphere, the x-axis represents the elapsed time, which can be expanded or collapsed by the user in order to provide a more (or less) detailed view of the process. The y-axis tracks variables such as temperature, pressure, oxygen level, nitrogen flow rate, and humidity level.
A few examples of the oven data gathered and analyzed by an IIoT system are as follows:
- The output of the temperature controller is monitored. If, for example, the controller output is normally running at 30% for a specific oven (meaning the oven is using 30% of its full heat capacity), and for no apparent reason it increases to 60% output, this indicates either an exhaust damper is stuck open and causing the oven to exhaust too much of its heat, there is a heater failure, or a door is not closing fully, or something else.
- Vibration sensors installed on recirculation blowers can monitor the health of the oven. Since blowers are rotating machines, they have a predictable vibration frequency and amplitude. As the blower bearings wear over time, these vibration parameters change. The IIoT system uses proprietary algorithms to determine acceptable vibration levels at different temperatures and RPMs. As the vibration values change over time, the system can predict when blower failure is likely, prior to it occurring. This allows replacement parts to be ordered before a “hair on fire” situation where the equipment suddenly stops working, interrupting production and workflow.
- In order to monitor the burners on gas-fired ovens, the flame safety system is wired to the IIoT system. This allows remote evaluation of the flame sensor, purge timer, and other components that are critical to safe and proper burner operation. On older ovens, nuisance shutdowns can occur due to a dirty combustion blower, dirty flame rod, faulty airflow switch, or other reasons. An IIoT system allows the oven manufacturer to remotely diagnose this type of issue without ever sending a service technician to the job site, saving time and money.
- An oven IIoT system is often used to measure the oven chamber pressure. Ovens can be intentionally operated at a neutral pressure, a slightly negative, or slightly positive pressure, for various process-related reasons. A pressure sensor measures this value and, via the IIoT gateway, delivers it to the dashboard in real time. If the chamber pressure strays outside of a predetermined range, this indicates a failure such as an improper damper setting or a malfunctioning exhaust blower.
The Benefits of IIoT Technology
Predictive maintenance is one of the most important benefits of IIoT. The ability to prevent potential equipment breakdowns and resulting process bottlenecks is invaluable. Not only does IIoT allow plant managers and operators to schedule maintenance ahead of time, it also reduces maintenance hours by knowing exactly what the issue is that needs to be serviced. This reduction in unplanned downtime increases productivity, which translates to higher profits.
The quantity of detailed, relevant data available (real time and retroactive) via the IIoT system exceeds the information a service technician can gather oven side, especially if the oven has stopped working. Using IIoT to remotely gain information to service the equipment, the problem can often be resolved the same day.
Perhaps the most impressive benefit of IIoT is remote diagnostics. Whether a furnace or oven is experiencing occasional unexplained shutdowns, or is completely out of commission, it typically takes days or weeks to schedule a service technician to inspect the equipment and diagnose the problem. However, if the oven is equipped with IIoT, a call can be made to the oven manufacturer who can remotely log into the system dashboard. They will be able to view and analyze the data gathered by all the sensors going back over time, without sending a service technician to the job site. Also, the quantity of detailed, relevant data available (real time and retroactive) via the IIoT system exceeds the information a service technician can gather oven-side, especially if the oven has stopped working. Using IIoT to remotely gain information to service the equipment, the problem can often be resolved the same day. Further, the IIoT system gathers and records the data going back in time for months, which is invaluable when trying to diagnose a chronic or intermittent failure.
Another use of IIoT technology is energy management. Through IIoT monitoring, facilities and equipment can be set to optimize energy efficiency. By ensuring the oven uses only the amount of heat energy necessary, and no more, its energy consumption is minimized. The system can reveal, for example, that a second shift oven operator opens the oven doors for five minutes to unload the parts and then load the next batch, while the first shift operator takes ten minutes to do the same process, wasting a great deal of energy as heated air spills out of the oven for an extra five minutes with every batch.
Data Security
IIoT devices use encryption to protect against unauthorized access to the oven operational data. Data transmitted between IIoT devices and the cloud is encrypted using protocols like Transport Layer Security (TLS). This provides confidence that only approved parties can access the information, safeguarding it from those with malicious intent. This ensures that even if data is intercepted, it will appear as jumbled information that cannot be read without the decryption key.
Because the data collected relates to the oven or furnace being monitored, and is not descriptive of the parts being processed, it would be of limited use to anyone who gained unauthorized access. If a malicious actor discovered, for example, the vibration levels, temperature controller output, or the status of the burner system while the oven is processing a load, it would be of limited proprietary value and would not directly reveal information about the parts being processed since no information about the load is included in the data.
In considering the security risk of an IIoT system collecting and transmitting data to the cloud, it must be compared to the alternative, which is bringing a service technician to the job site to perform the required maintenance or troubleshooting. When a service technician is invited on site, they have the opportunity to view the parts being processed, which temperature profiles apply to which parts, material handling methods, ancillary processes performed before or after heating, and even unrelated proprietary processes performed in the facility. This level of intrusion is much greater than simply sending the oven IIoT data to the cloud and avoiding the service technician entirely.
The Future of IIoT
Since the introduction of IIoT to the industrial oven market, it has gained acceptance by a wide range of manufacturers, and it is expected to continue to grow. Artificial intelligence (AI) is becoming a part of IIoT, as it can optimize the algorithms used in predictive maintenance. Also, IIoT can incorporate AI’s cognitive capabilities to better be able to learn at what thresholds of vibration, pressure, etc., to send alert notifications.
To Summarize
Consider purchasing an IIoT system with your next industrial oven. The successful implementation and use of IIoT provides a competitive advantage to the owner of the equipment. In today’s world of “doing more with less,” IIoT can increase productivity, reduce maintenance costs and unplanned downtime, and decrease energy use, all at minimal cost, and with no additional personnel required.
About the Author:
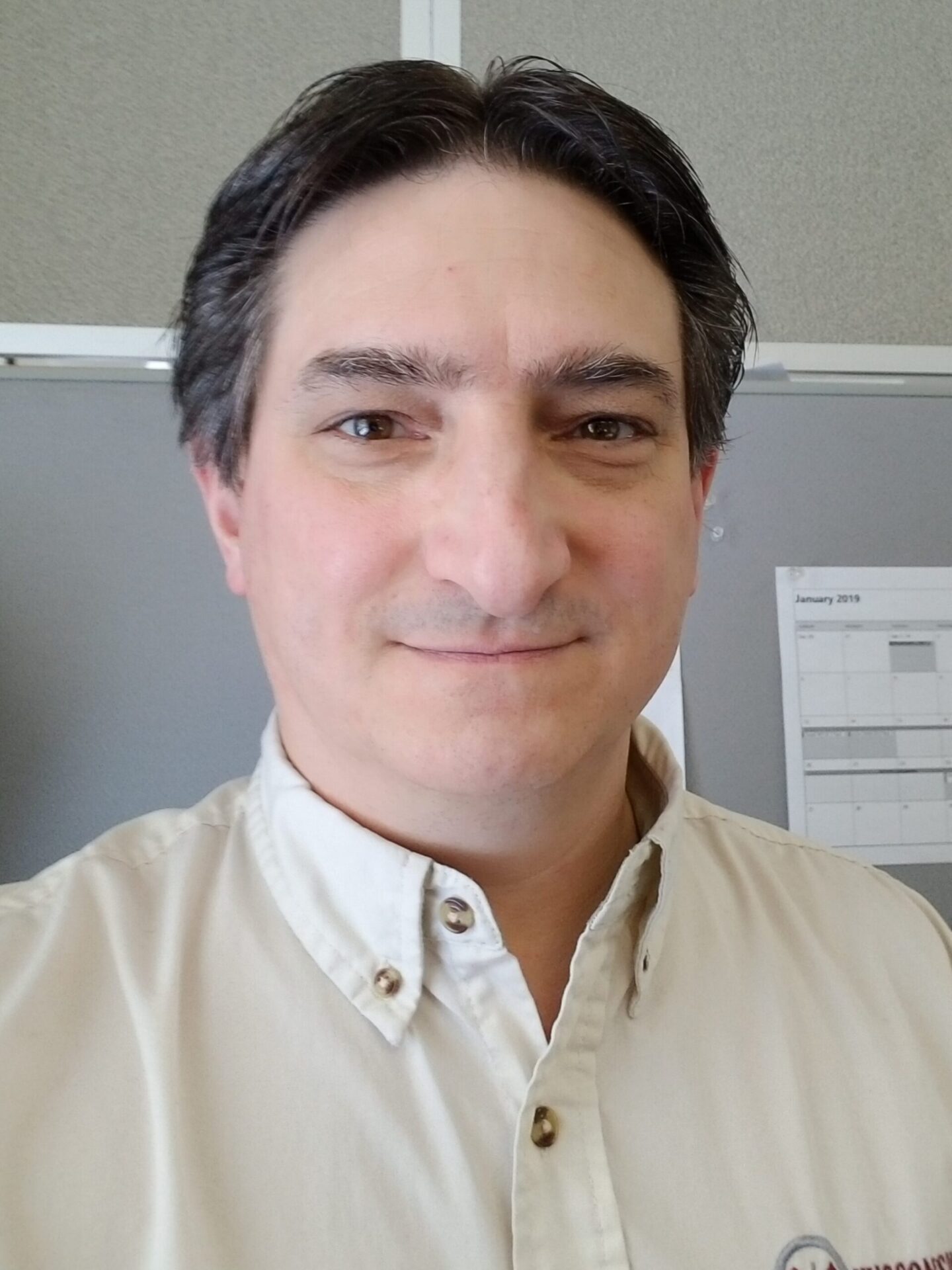
Vice President of Sales
Wisconsin Oven Corporation
Mike Grande has a 30+ year background in the heat processing industry, including ovens, furnaces, and infrared equipment. He has a BS in Mechanical Engineering from University of Wisconsin-Milwaukee and received his certification as an Energy Manager (CEM) from the Association of Energy Engineers in 2009. Mike is the vice president of Sales at Wisconsin Oven Corporation.
For more information: Contact sales@wisoven.com.