Nadcap Audit Accreditation Firsthand: Learning from the Process
Heat Treat Today’s regular contributor Jason Schulze of Conrad Kacsik (“Jason Schulze on AMS2750E” series) interviewed Shaun Kim from Byington Heat Treating, located in Santa Clara, California, about the company’s experience preparing for and working through the Nadcap accreditation process. Shaun is the quality director at Byington Heat Treating.

As a quality director at a commercial heat treat facility, I’ve been presented with some challenging situations. I take each challenge and examine it in any way I can, or at least, in any way that I know how. I like to think I’m a detail-oriented, evidence-based thinker with the ability to, at the very least, recognize gaps even if I’m not sure how to fill them. In short, the challenges drive me to learn more, and in the end, that is what I’m after. That is what I got out of the Nadcap process: a learning experience that has since prepared me for the next round.
My name is Shaun Kim. I’m the Director of Quality at Byington Steel Treating located in the California Bay Area. In fact, we are now the only Nadcap-approved commercial heat treat facility in the area. Byington Steel Treating has been around since 1952, heat-treating materials from carbon steels to aluminum allows to superalloys. Our capabilities have grown through the years and include hardness and conductivity testing. As we heat treat to AMS2759 (and family), AMS2770, and AMS2771, as well as material specifications, Nadcap accreditation was inevitable.

The vision of Nadcap accreditation in heat treat was initiated and fully supported by our CEO Sean Byington. I know that, for many in the field, management may not supply the full resources needed to achieve Nadcap approval, but for me, that was not the case. Our CEO offered all the necessary resources to achieve accreditation. My challenge, once I first gained access to the eAudit.net website, was the new requirements within the checklist. As I stated, I’m detail-oriented, so I examined the checklists closely and, in the process, realized that in order to achieve Nadcap accreditation, simply conforming to an AMS specification wouldn’t be enough.
My biggest challenge was pyrometry. At the time I didn’t understand AMS2750E very well, so I intently read the specification until it started to make sense. I must have read that specification 10-plus times. Our initial Nadcap audit did not go well. It wasn’t that we were not doing what was required; it was that we did not have those requirements documented. We ended up going through the risk-mitigation process, otherwise, we would have had to wait two years to re-apply for Nadcap heat treat accreditation—something our team and CEO was not willing to do. If I had to point out some things I would have done differently pre-risk mitigation, I would have a) given myself more time to prepare, b) hired an industry expert to perform a gap-analysis using the AC7102 checklists, and c) hired an industry expert to facilitate the audit.
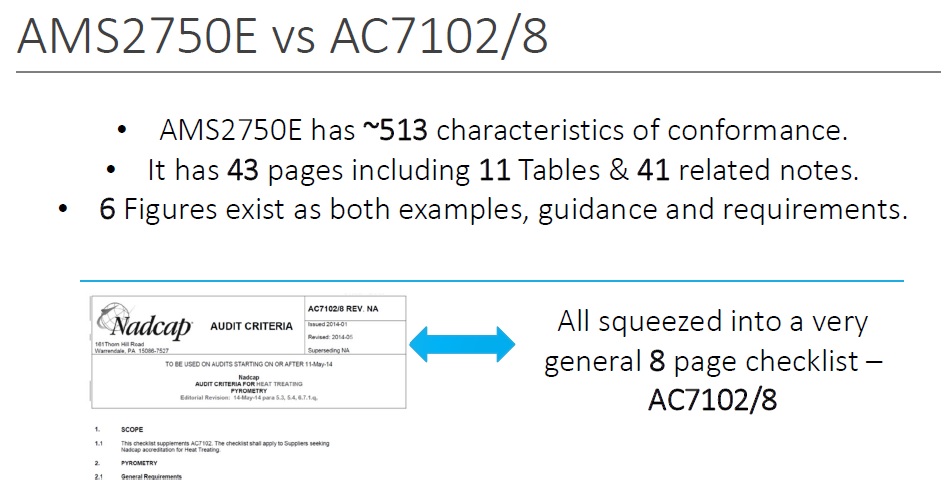
Back to the risk mitigation process. The Nadcap risk mitigation process essentially consists of addressing all findings received from the eAudit.net system. PRI Staff Engineers will review root cause and corrective actions as they normally would during a reaccreditation audit. Prior to the risk mitigation process, we engaged an industry expert to help us review the findings to ensure that what we were capturing would improve our process and get the findings closed. Even though the risk mitigation process, we learned a lot about the response expectations and just how far we had to dive into our process to find the root cause and take corrective action. In the end, I must admit, I wouldn’t have changed anything. Going through the pains of risk mitigation prepared our company for the stringent requirements that come when processing aerospace parts to the requirements of Nadcap. Nadcap is a serious thing, and we wanted to learn as much as we could even if it meant putting a lot of time and effort into risk mitigation, which we did.
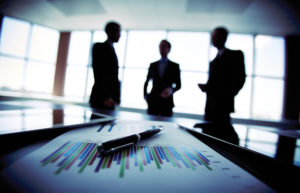
Post-risk-mitigation, my experience was completely different and so was our approach. We retained our consultant who walked us through a gap analysis and supplied us with a close-out letter, laying out each gap for each checklist and how to close the gap. Once we had this information, and with an open line of communication to our consultant, we modified our procedures/forms and re-trained our staff in line with changes and requirements. At that point, my understanding of the Nadcap requirements, as well as AMS2750E, had improved greatly, which helped us through the process.
The time came for us to have our initial Nadcap heat treat audit. This process was tough. We had worked hard to close all the gaps we could think of. The auditor did not necessarily contribute to the tough process; it was more about the under-the-gun feeling. We had worked hard and invested the time and money to ensure a successful audit, and we were eager to experience the reward. Of course, there were several times we did not see eye-to-eye with the auditor, but in the end, we had a very successful audit. We passed with room to spare.

In the end, I learned a lot through the process of Nadcap accreditation in heat treat. I’m a strong believer that you will never learn anything unless you make mistakes along the way and identify why it happened. There is no way for us to learn unless someone points it out or an event forces us to recognize the gap and we then address it.
Almost immediately, we began receiving RFQs which required Nadcap accreditation in heat treat. We have been processing quite a bit of work which requires Nadcap approval and aim to get more. If I could share any advice it would be the following:
- Start from the beginning. Get the checklist and fill it out honestly—be honest with yourself about your capabilities.
- It will not help you to ignore the gaps. Identify the gaps and start with those areas for improvement.
- I recommend getting a consultant familiar with the Nadcap process of audits. The more you learn, the better off you will be.
If you would like to contact me for questions regarding my experience in our Nadcap heat treat accreditation process, please feel free to email me at skim@byingtonsteel.com. I look forward to sharing my experience and learning from yours.

Written by Jason Schulze from questions presented by Jason Schulze using responses submitted by Shaun Kim from Byington Heat Treating.
Nadcap Audit Accreditation Firsthand: Learning from the Process Read More »