High-Purity Alumina Calcining Processes Support Expansion
One of North America’s leading producers of ultra-high-purity alumina and associated products recently boosted its advanced manufacturing operations with a 50m-long electric tunnel kiln. This installation will support the company’s expansion into the production of a variety of high specification lines.
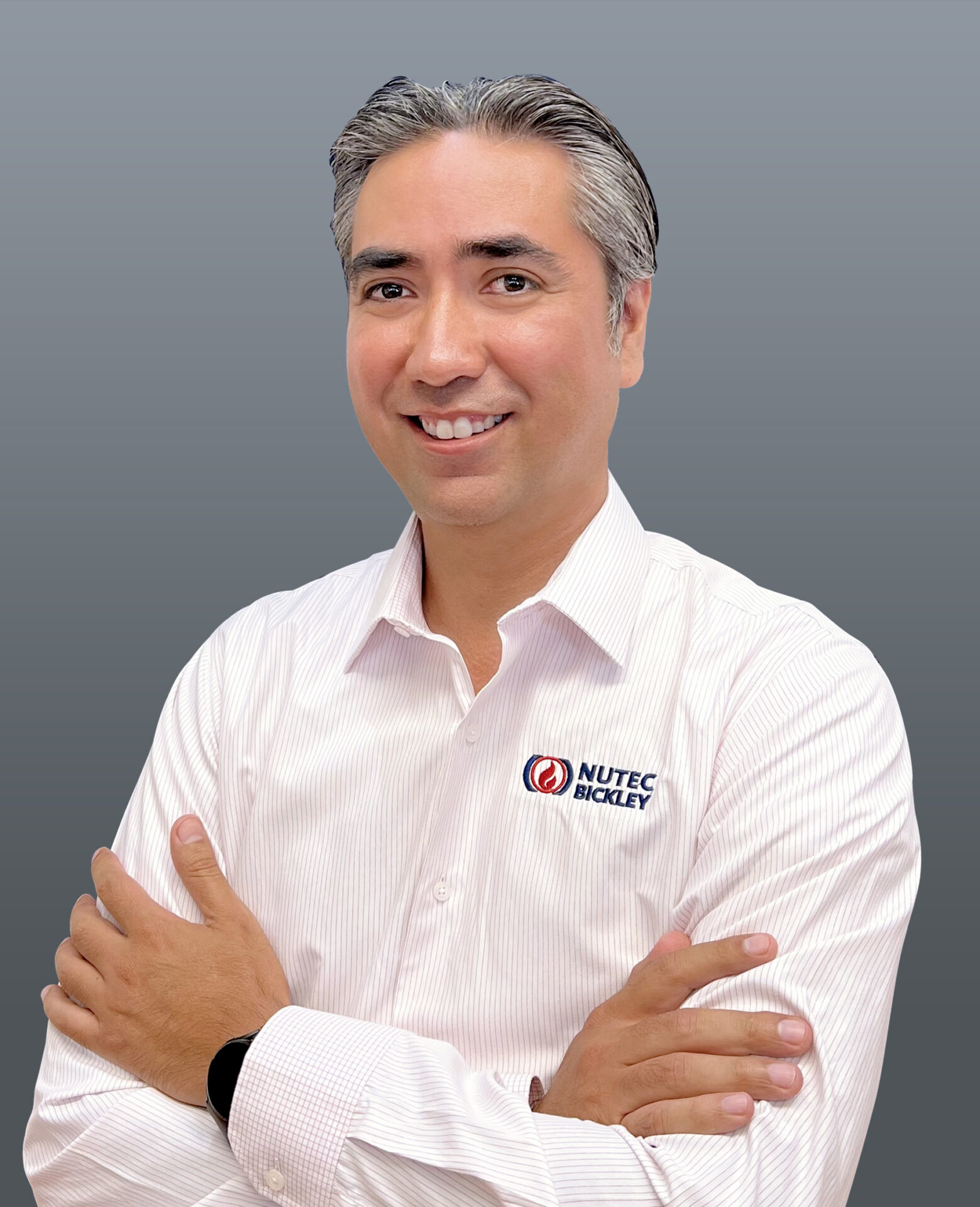
NUTEC Bickley
The calcination kiln, which was broken down into modules and transported by NUTEC Bickley, has an operating temperature of 2190°F (1200°C) and maximum temperature of 2460°F (1350°C) and processes the material in saggars sitting in six-high stacks that are loaded on to 33 cars. With a firing cycle of 23.6 hours, approximately 5000kg of calcined material is processed each day. In addition, special provisions to prevent equipment wear due to chemical attack that follows degassing of hydrochloric acid during the alumina heating process has been designed by NUTEC Bickley.
“The nature of the material being processed means that tight tolerances and demanding specifications have had to be met,” said Alberto Cantú, vice-president of ceramics at NUTEC Bickley. “[This] demonstrates once again how, when all necessary design parameters are in place, electric heating in continuous kilns can deliver for a wide range of manufacturing processes.”
The use of electric heating is increasingly in demand. Extremely tight thermal control is necessary in the kiln chamber, operating under an oxidizing atmosphere, and this particular kiln has 14 automatic control zones for heating, plus two automatic zones for cooling. To ensure maximum flexibility and management of the temperature profile, the control systems are arranged so that the exhaust, heating zones, and cooling zones are all independently regulated.
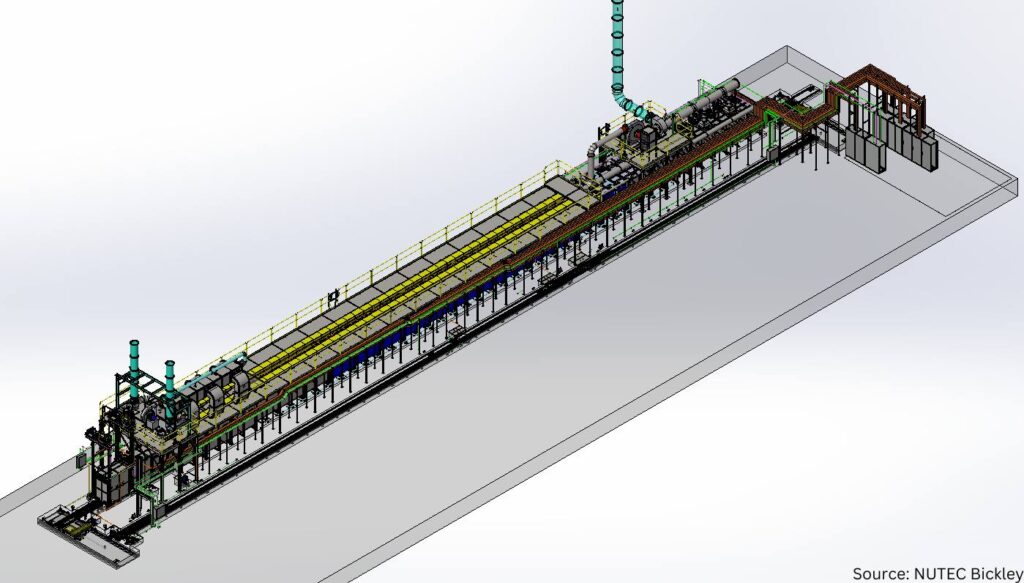
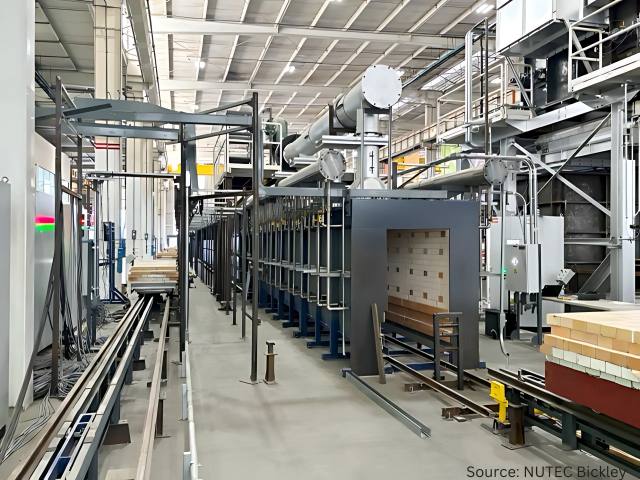
The heating system comprises a combination of silicon carbide and metal alloy elements. These hang down vertically through the roof and are sited on either side of the load, with distribution configured to deliver a well-balanced temperature uniformity throughout the kiln. The electrical connection design means that elements can be replaced while the furnace is at operating temperature.
Hot gases are drawn towards the kiln entrance and are evacuated from the tunnel through exhaust ports positioned in the kiln sidewalls, via the exhaust fan. Cooling is achieved by direct air movement in the cooling zones. The temperature set points from the cooling zones are controlled automatically with cooling nozzles positioned to blow a stream of cold air above and below the load setting. The kiln walls use lightweight insulation for rapid thermal response and fuel economy, with the lining rated for use up to 2350ºF (1290°C). The roof is lined with high thermal efficiency ceramic fiber system, and the roof insulation combines modules of polycrystalline fiber and zirconia grade fiber.
Kiln car operation is based on a semi-continuous feed electromechanical pusher with push speed adjustment. The push speed is configurable by selecting the appropriate firing schedule at the kiln control panel. A vestibule arrangement serves to reduce exchange of air and gases between the factory and the kiln. When a car is being introduced into the kiln, the door at the entry end opens, while the door at the kiln entrance is closed.
The vestibule has two sections: the first accommodates a single car and is separated by two vertical lift doors to separate the factory’s atmosphere from the kiln atmosphere. This is managed by installing an exhaust hood which is connected to the entry exhaust fan, thus ensuring a negative pressure in the vestibule to avoid any gases from the kiln from leaving the chamber. The second section functions as a transition from the vestibule door sections to the kiln’s pusher.
Press release is available in its original form here.
Find heat treating products and services when you search on Heat Treat Buyers Guide.Com
High-Purity Alumina Calcining Processes Support Expansion Read More »