Who’s Winning the Steel v. Aluminum Battle? Both, in the Form of Mixed Materials, per Auto Industry Watchers
Source: SME Media
It wasn’t long ago that auto industry watchers were casting votes for either steel or aluminum in what was to be a big competition in what metals would be used in automotive lightweighting.
Would it be the heavy-weight champion steel which was ramping up its development of high-strength, lower-weight steels? Or would the new contender on the block, aluminum, gather more adherents to lightweighting in the wake of Ford Motor Company choosing aluminum for its F-150 and Super Duty pickup bodies?
An excerpt:
“A consensus has emerged. The future for the industry is a mix of materials, a mix that will vary from vehicle to vehicle. It’s also likely to be a more complex future, with composite materials making inroads in the long run.”
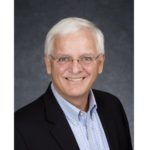
“You have to take into account all sorts of factors,” said Jay Baron, retired president of the Center for Automotive Research (CAR), Ann Arbor, Michigan. Vibration and stiffness figure into the equation, he said. And there’s cost. “It’s much more than weight and strength.”
Designing and building vehicles with a patchwork quilt approach to materials is how some brands are tackling the lightweighting challenge. Most are also exploring advanced technological processes such as a combination of 3D printing and artificial intelligence, friction welding technology, and rethinking other automotive systems, e.g., braking.
Read more: “Lightweighting’s New Phase”
Main image credit / caption: Manufacturing Technology Inc. (MTI) / The MTI-built LF35-75 at Lightweight Innovations for Tomorrow is ideal for unique part geometries, near-net shapes and full-size part development for all industries, according to MTI.