Auto Parts Manufacturer to Increase Aluminum Production Capacity with Expansion, New Equipment
A global automotive parts manufacturer recently announced its plans to invest in the expansion of its Kentucky aluminum products plant.
Kobelco Aluminum Products & Extrusions Inc. (KPEX), the U.S. subsidiary of Kobe Steel, Ltd., based in Japan, expects the expansion to increase the production capacity of its plant in Bowling Green, Kentucky, in response to the growing demand for automotive extrusions and fabricated products in the United States.
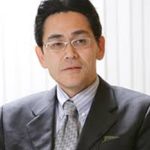
Established in April 2016, KPEX manufactures aluminum extruded products for use as bumper materials and car frame materials. In November 2018, KPEX began integrated production, ranging from melting and casting to the final manufacturing process of fabrication. Plans call for new equipment for melting, extrusion, and fabrication to go into mass production in the first half of 2020. When the expansion is completed, KPEX will have two melting furnaces and two extrusion presses. Production capacity will increase to 1,000 tons per month, from the current 500 tons per month.
“Kobelco Aluminum Products & Extrusions Inc. was established in April 2016 using our technology from Japan, and with the cooperation of Kentucky officials, our customers, and all the employees working at Kobelco, we were able to successfully begin mass production here in the US,” said Hiroaki Matsubara, Kobe Steel senior managing executive officer. “And now, supported by even more robust demand for our products, we are proud to announce that we will be making our second major investment in our operations in less than two years. With that, our aim is to continue to make our contribution to the weight reduction of automobiles and to further develop our business footprint in the Bowling Green facility.”
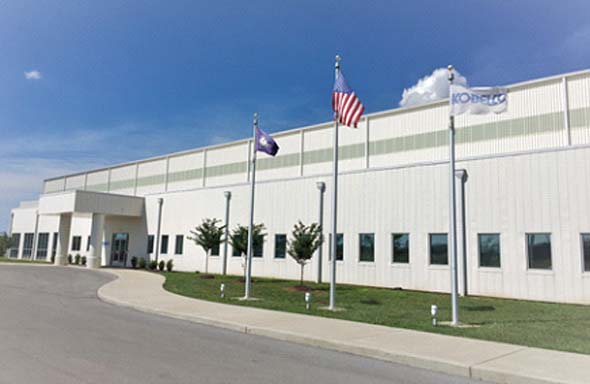
Main image PC: Forging Magazine