New VW Crafter Van to Sport Axle Designed for Heavy Payloads
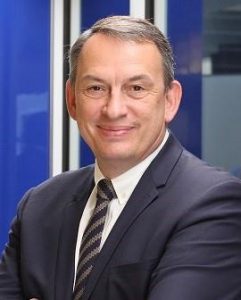
An engineering solutions company based in Maumee, Ohio, recently announced it will be supplying all-wheel-drive axle to the new, award-winning Volkswagen Crafter 4 Motion panel van.
Dana Incorporated manufactures the compactly designed Spicer® AdvanTEK®M180 axle at its Birmingham, England, facility. A key feature of the axle is its advanced electronic-locking differential. As part of the complete system design, the four-pinion rear-locking differential incorporates an electric solenoid with an electronic position sensor to lock the wheels together for improved traction and stability. Dana was responsible for ensuring the locking differential application software met Volkswagen’s stringent performance and demanding functional safety requirements.
“Our team worked closely with Volkswagen from start to finish to develop and launch the best solution for the all-new Crafter 4 Motion. We are proud to be part of this vehicle, the 2017 International Van of the Year,” said Christophe Dominiak, senior vice president and chief technology officer of Dana. “The new axle on the Volkswagen Crafter is a great example of Dana’s leadership in efficient all-wheel-drive integration technologies and our ability to partner with our customers to provide them the solution they need to meet ever-changing market demands.”
The company also launched its Spicer® AdvanTEK® M250 rear axle – also manufactured in Birmingham, England – for rear-wheel-drive versions of the VW Crafter. This axle is designed to handle heavier payloads while providing optimal traction and power density, even when the vehicle is fully loaded.
Dana supports the passenger vehicle, commercial truck, and off-highway markets, as well as industrial and stationary equipment applications.
New VW Crafter Van to Sport Axle Designed for Heavy Payloads Read More »