Pittsburgh-based Providers Merge, Strengthen Heat Treatment Capabilities
A global supplier of equipment, systems, and digital solutions for several manufacturing sectors recently announced that it has acquired Bloom Engineering, Inc, a provider in industrial heating applications. The company will join the Freight & Industrial Components Group at Wabtec Corporation, which serves the freight and transit rail industries and is a worldwide leader in the decarbonization of freight rail.
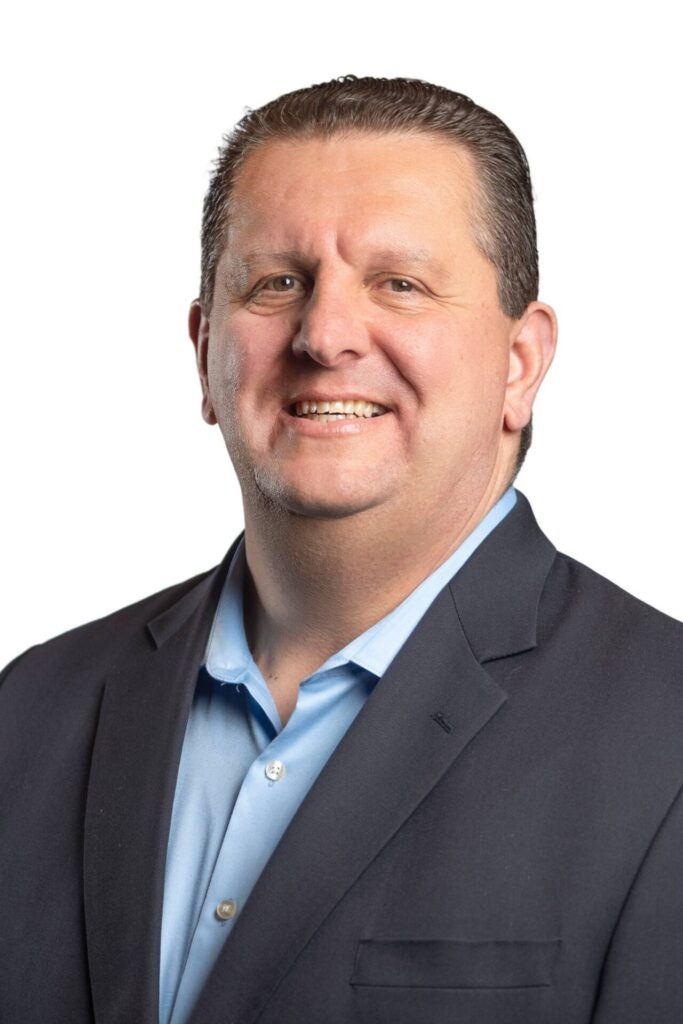
President
Freight & Industrial Components Group
Wabtec Corporation
This acquisition strengthens Wabtec’s heat transfer and energy solutions, integrating Bloom’s advanced technologies in burners, combustion systems, and overall services for industrial and process heating applications. Both companies are headquartered in Pittsburgh, PA.
“This is another exciting addition to Wabtec,” said Mike Fetsko, president of Wabtec’s Freight & Industrial Components Group. “Bloom Engineering is a great fit within our heat transfer and energy solutions business, and we already serve many of the same customers. Our shared vision toward driving customer productivity within their industrial processes will enable us to deliver a more comprehensive portfolio for our customers to operate more efficiently and sustainably.”
In addition to supplying solutions for the freight and transit rail industries, Wabtec also serves the mining, marine and industrial sectors. The acquisition is expected to provide increased value to its worldwide customer base.
The press release is available in its original form here.
Find heat treating products and services when you search on Heat Treat Buyers Guide.Com
Pittsburgh-based Providers Merge, Strengthen Heat Treatment Capabilities Read More »