ZDT Glimag Leverages Vacuum Furnace for Mining Machines
Vacuum heat treat operations expand for ZDT Glimag, an entity providing services in the field of vacuum heat treatment, laboratory tests, and production of parts for mining machines.
The addition of this Vector® vacuum furnace will be the third vacuum furnace from SECO/WARWICK. The current design has an operating space of 600 x 600 x 900 mm and will be equipped with numerous options to allow a wide range of heat treatment processes for various steel grades. Main processes will include vacuum brazing, FineCarb® vacuum carburizing, and high-pressure hardening. The design of the chamber size will enable efficient heat treatment of large packages of test and research elements.
The efficiency of processes is also influenced by the ability to cool at 15 bar (which, unlike the old furnaces, eliminates the need to wash the parts after the process). In combination with inverter control, the system also helps reduce power consumption peaks, which are so problematic today. Another big advantage is low heat losses and appropriate temperature uniformity in the heating chamber, which is resistant to rapid wear and is easy to use and service.
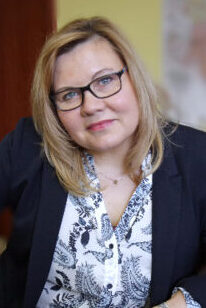
President of the Management Board – Financial Director of ZDT Glimag
Source: LinkedIn
Beata Kowalewska, president of the Management Board – Financial Director of ZDT Glimag, comments: “Since the 1960s, we have been designing prototypes, conducting research and technological tests, and implementing new technologies for mining. We are currently in the process of materializing the project titled ‘Implementation of an innovative product resulting from research and development work: a brake pad with a composite friction layer with increased abrasion resistance,’ implemented under the European Funds for a Modern Economy (FENG) 2021-2027 Program. FENG is a program supporting entrepreneurs in the area of broadly understood innovation. It places great emphasis on R&D activities.”
He continues, “The new SECO/WARWICK furnace fits perfectly into the policy of broadly understood modernity implemented in this project. It will streamline and expand the scope of heat treatment processes and improve their economics, taking into account energy savings and the graphite chamber efficiency. It will also ensure the process cleanliness and velocity. With the FineCarb® vacuum carburizing option, the technology also increases our flexibility and research capabilities. Additionally, this technology will allow us to perform more difficult processes requiring extremely low contamination levels, thanks to the ability to obtain the appropriate vacuum needed for these processes.”
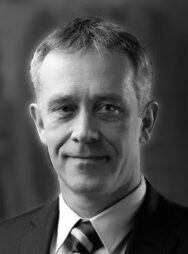
VP of the Vacuum Furnace Segment
SECO/WARWICK
Source: SECO/WARWICK
Maciej Korecki, VP of the Vacuum Furnace Segment in the SECO/WARWICK Group, comments on ZDT Glimag saying, “It is a center very well oriented in the metal heat treatment industry, constantly testing new, innovative solutions that in turn make the mining industry more efficient. The new Vector will introduce revolutionary changes in the hardening plant, introducing innovation and a very wide range of precise processes.”
The Vector® line vacuum furnaces can be used in most standard vacuum carburizing, hardening, tempering, annealing, supersaturation, and brazing processes. At the same time, the solution can be adapted to the recipient’s individual requirements, and therefore to a specific industry, an attribute necessary for research centers that test innovative solutions for external customers.
The solution‘s characteristic features are convection heating, i.e., a system improving the heat transfer efficiency when heating at lower temperatures, and directional cooling, which allows complex, flimsy, and long elements to be cooled in various ways, minimizing their deformations. An additional advantage is the vacuum carburizing option, which allows users to carry out precise processes to increase the steel surface hardness (carburizing) during the entire thermal process.
The original press release from SECO/WARWICK Group is available here.
Find Heat Treating Products And Services When You Search On Heat Treat Buyers Guide.Com
ZDT Glimag Leverages Vacuum Furnace for Mining Machines Read More »