Magnesium Supplier Expansion Includes Heat Treating Capabilities
A leading manufacturer of magnesium dissolvable metals and dissolvable elastomers recently broke ground on a 12,000 sq. ft. expansion to its magnesium foundry, which will increase its metal processing, heat treatment, machining, and storage capabilities.
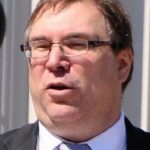
Terves Inc announced that the H3-classified magnesium metal processing facility at its site in Euclid, Ohio, will include additional permanent mold and materials handling and storage space, and the addition of sand casting, squeeze casting, and diecasting capabilities for custom magnesium and magnesium alloys and composites, and allows for further expansion of build-to-print component CNC machining services. These additions enable the company to support aerospace and defense magnesium applications in addition to Terves’ leading position in the dissolvable oilfield tool market.
“Dissolvable Metals are the New Composites as far as oilfield tools are concerned,” said Andrew Sherman, CEO of Terves. “Oilfield tools made from composite materials were adopted in the industry about two decades ago and today occupy a sizable market share. We are seeing a major adoption and growth trajectory for oilfield tools made from dissolvable magnesium materials. At the end of 2017, roughly 2% of all frac plugs deployed in the field were being made using dissolvable metals and the market is expected to grow to 5% of all frac plugs deployed in the field by the end of 2018 – a 250% growth in one year, with adoption and use increasing through 2025.”
Terves products are used for making frac balls, plugs, slips, seals and several other components used in oil and gas well completion and production and have been used for completing tens of thousands of stages in North America, Europe, South America, Asia, and MENA regions.
Magnesium Supplier Expansion Includes Heat Treating Capabilities Read More »