HIP Innovation Maximizes AM Medical Potential
The appeal of additive manufacturing (AM) for producing orthopedic implants lies in the “ability to design and manufacture complex and customized structures for surgical patients in a short amount of time.” To complement speed of production, learn how an innovative hot isostatic pressing (HIP) application is confronting the challenges of post-processing heat treatments when creating high quality AM medical parts.
Today’s Technical Tuesday article, written by Andrew Cassese, applications engineer; Anders Magnusson, manager of Business Development; and Chad Beamer, senior applications engineer, all from Quintus Technologies, was originally published in Heat Treat Today’s December 2023’s Medical and Energy Heat Treat magazine.
AM is playing a significant role in the medical industry. It gives manufacturers the ability to create customized and complex structures for surgical implants and medical devices. Additionally, medical device manufacturers have different material factors to consider – such as biocompatibility, corrosion resistance, strength, and fatigue – when selecting a material for a given application. Each of these factors plays a significant role. It’s no wonder that the most common metallic biomaterials in today’s industry are stainless steels, cobalt-chrome alloys, and titanium alloys (Trevisan et al., 2018).
In this article, learn about the application of Ti6Al4V in the medical industry, as well as ways to address some of the challenges when producing AM medical components.
The Future Demands Orthopedic Implants
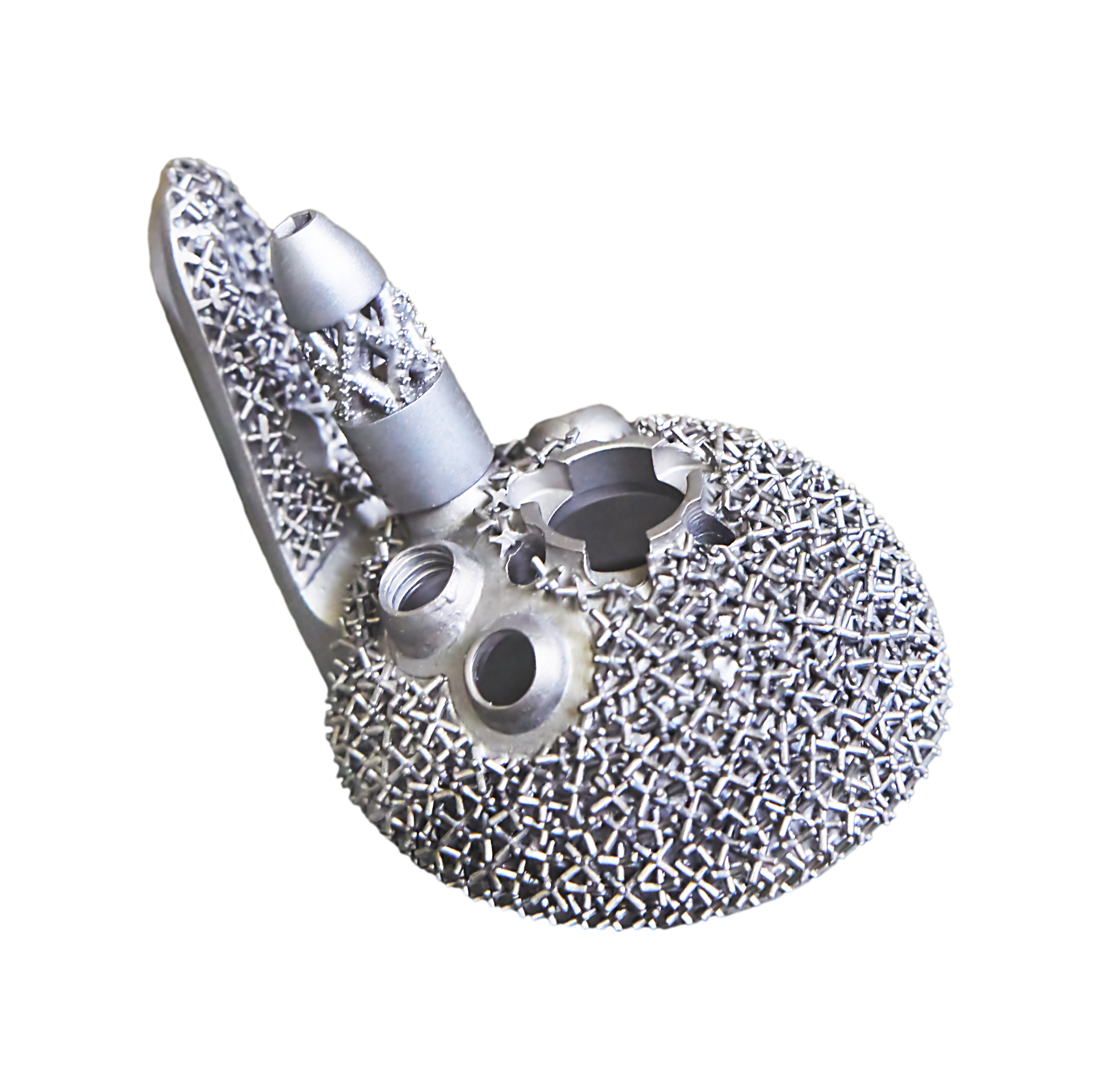
acetabular cup (Source: Quintus Technologies)
The medical market for orthopedic implants is predicted to grow annually by approximately 4% where joint replacement, spine, and trauma sectors are reported to account for more than two-thirds of the market. The largest portion is joint replacement with over a third of global turnover, reaching in excess of 20 million U.S. dollars in 2022 (ORTHOWORLD® Inc., 2023). This confirms an earlier study by Allied Market Research where spine, knee, and hip implants made up over 66% of the entire market, with knee implants leading the way at 26% (Allied Market Research Study, 2022). This fact, combined with the expectation that the global population aged 60+ is predicted to double between 2020 and 2050, adds to the increasing demand on manufacturers to produce better quality and longer lasting orthopedic implants (Koju et al., 2022).
These factors have increased the predicted medical implant market for Ti6Al4V and other common orthopedic materials. Using AM processes such as electron beam melting (EBM) and laser powder beam fusion (L-PBF), manufacturers can produce thin-walled trabecular structures that are fabricated to promote bone ingrowth in a growing market that is in competition with traditional production methods.
Titanium-based alloys have been increasingly used in orthopedic applications due to their high corrosion resistance and a Young’s modulus similar to that of human cortical bone (Kelly et al., 2021). The high strength-to-weight ratio and bioinert-ness of Ti6Al4V has proven it to be an ideal candidate for orthopedic and dental implants. It is a titanium alloy with 6% aluminum and 4% vanadium that has low density, high weldability, and is heat treatable. Ti6Al4V demonstrates good osteointegration properties, which is defined as the structural and functional connection between living bone and the surface of a load carrying medical implant.
Many manufacturers are using L-PBF to create thin-walled complex structures on the surface of the implant. This makes use of the osteointegration properties as the implant integrates itself into the body over time without the need for bone cement (Kelly et al., 2021). Introducing a large metallic foreign body leads to challenges such as promotion of chronic inflammation, infection, and biofilm formation. Instead, porous AM Ti6Al4V implants have a biomimetic design attempt towards natural bone morphology (Koju et al., 2022).
AM Yields Production Solutions for Medical Alloys
The medical industry has been increasing the use of AM over traditional processing methods. AM facilitates weight reduction, material savings, and shortened lead-time due to reduced machining, but these are only a few of the benefits. Improved functionality and patient satisfaction are also key aspects through tailoring of designs to take advantage of AM over traditional forging and casting techniques. Additionally, the costs of machining a strong alloy like Ti6Al4V can be expensive, and any wasted material and time in turn lead to higher cost.
One of the main reasons for the interest in AM is the ability to design and manufacture complex and customized structures for surgical patients in a short amount of time. For example, if a patient needs an implant for surgery, an MRI scan can help reverse engineer a customized implant. Engineers prepare a design of a patient-specific implant according to the patient’s anatomy that is then printed, HIPed, and finished for surgery with a reduced lead time. This is especially important for trauma victims, where the speed of repair can mean the difference between losing a limb or returning to a fully functional life. Cancer victims and those requiring aesthetic surgery to the skull, nose, jaw, etc., can also benefit from this (Benady et al., 2023).
Some of the current challenges with AM titanium in the medical industry are related to the post-processing heat treatments that are required. These treatments can leave an oxide layer on thin-walled structures that is hard to remove by machining or chemical milling. Quintus Purus®, a unique clean-HIP solution, has proven to overcome this challenge and provide clients with a robust solution that both densifies and maintains a clean surface.
When HIP Meets AM

HIP is important in the AM world as a post-process that closes porosity and increases fatigue life. For medical implants, high and low cycle fatigue life properties are key as they affect the longevity of the repair. The mechanical strength and integrity are improved significantly by HIPing the implants, reducing the need for further surgery on the same patient. Modern HIP cycles have been developed to further increase this performance. When combined with Quintus Purus®, modern HIP cycles can minimize the thin, oxygen-affected layer that can result from thermal processing on surfaces of high oxygen-affinitive materials, such as titanium.
For Ti6Al4V, this layer is often referred to as alpha-case. The brittle nature of the alpha-case negatively impacts material properties resulting in medical manufacturers requesting their AM parts in the “alpha-case free” state. Alpha-case can be formed during heat treatment. As surfaces of the payload and process equipment are exposed to oxygen at elevated temperatures, they may be oxidized or reduced, depending on the oxide to oxygen partial pressure equilibrium. During heat treatment, evaporating compounds become part of the process atmosphere, and solids are deposited or formed on other surfaces, either as particles or as surface oxides.
For titanium alloys, surface oxides are formed at logarithmic or linear rates, depending on temperature and oxygen partial pressure. At the same time, oxygen can diffuse into the surface to form the brittle alpha-case, which is detrimental to the part’s fatigue performance. Changes of the surface color can often be seen as an indication that surface reactions have occurred during processing when using traditional thermal processes (Magnusson et al., 2023).
The HIP furnace atmosphere contaminants that cause this oxidation can originate from various sources including the process gas, equipment, furnace interior, and, most importantly, the parts to be processed. The payload itself often absorbs moisture from the surrounding atmosphere before being loaded into the furnace, which is subsequently released into the HIP atmosphere during processing. Industrial practice today attempts to solve the issue by wrapping parts in a material such as stainless steel foil or a “getter” that has a high affinity to oxygen protecting the Ti6Al4V component from exposure to large volumes of process gas, thus helping minimize the pickup of the contaminates.
This method adds material, time, and labor to wrap and unwrap parts before and after each HIP cycle. Also, wrapping in getter cannot guarantee cleanliness and may result in some uneven oxidation. This is where the tools of Quintus Purus® are of assistance; these tools allow the user to define a maximum water vapor content that can be accepted in the HIP system before the process starts. The tool utilizes the Quintus HIP hardware together with a newly developed software routine, ensuring that the target water vapor level is met in the shortest time possible. The result is a cleaner payload, without the need to directly wrap components with getter (Magnusson et al., 2023).

(Source: Quintus Technologies)

Alpha-Case Avoided: Comparing Conventional HIP and Optimized HIP Technologies
Quintus Technologies performed a study with Zeda, Inc. to evaluate Quintus Purus® on L-PBF Ti6Al4V medical implant parts. The study was performed in the Application Center in Västerås, Sweden in a QIH 21 HIP. A conventional HIP cycle was performed as well as an optimized Quintus Purus® HIP cycle, both without the use of getter. No presence of alpha-case was found on the part processed with the Quintus Purus® cycle as shown in Figure 2 below (Magnusson et al., 2023).
Quintus Purus® can be further enhanced with the use of a Quintus custom-made getter cassette supplied as part of the installation, which consumes or competes for the remainder of contaminant gaseous compounds still present in the system after all other measures such as best practice handling, adjustment of gas quality, etc., have been implemented.
Titanium is considered the getter of choice for Quintus Purus® and is included as an optional compact getter cassette placed at the optimum position in the hot zone of the HIP furnace. Although the custom-made getter cassette occupies a small space, its use can significantly increase loading efficiency. The traditional way of individually wrapping components with stainless steel or titanium foil will consume more furnace volume, through reduced packing efficiency, leading to less components per cycle when compared to the Quintus Purus® titanium getter cassette strategy. Using an average spinal implant size of 2 in3 (32 cm3), one can calculate the packing density in a standard HIP vessel assuming two shifts per day and a 90% machine uptime. For example, a Quintus Technologies QIH 60 URC with a hot zone diameter of 16 in (410 mm) and a height of 40 in (1,000 mm) can pack up to 1,280 implants per cycle, with clearances for proper spacing and load plates.
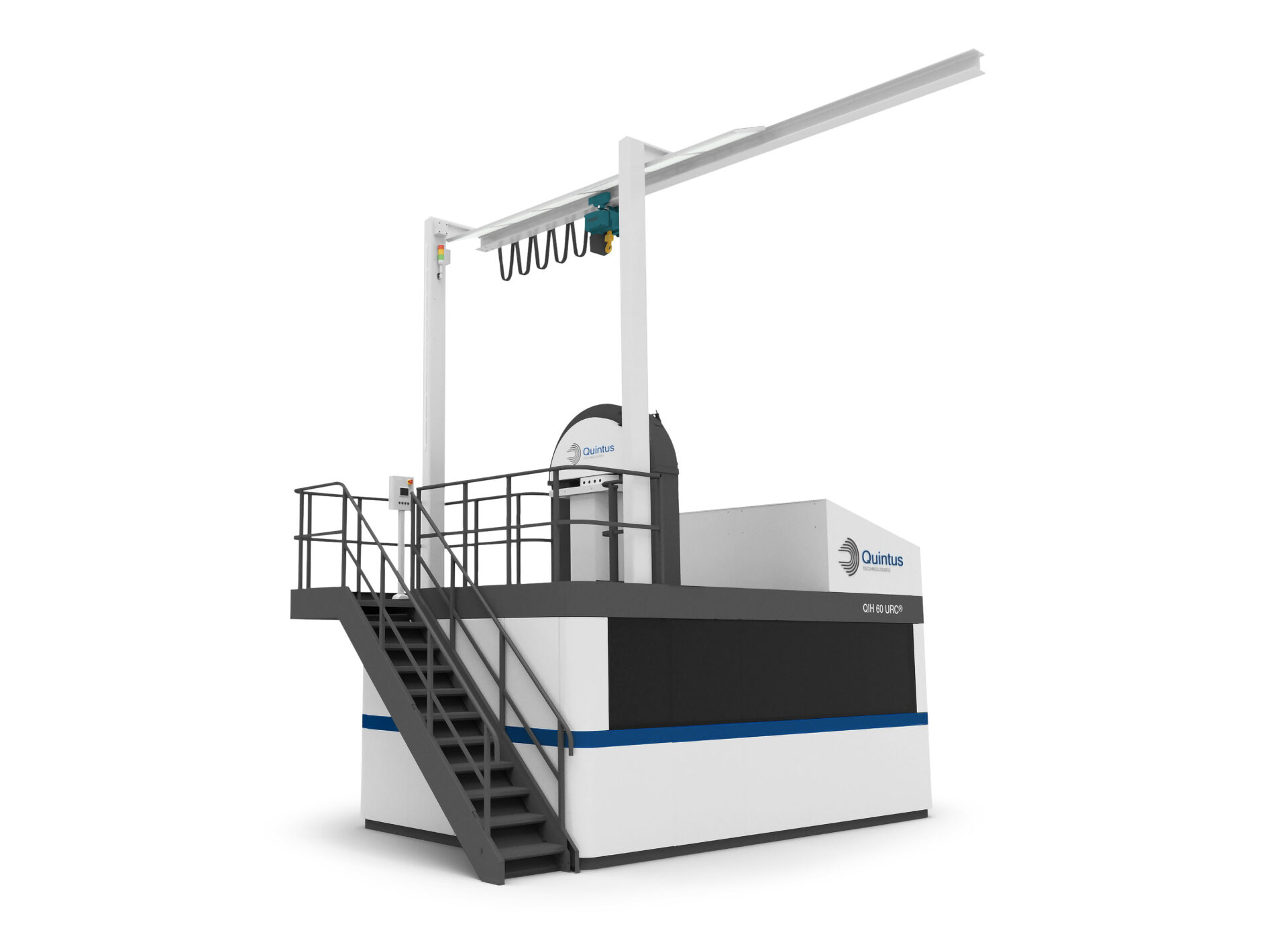
Quintus Purus® technology (Source: Quintus Technologies)
The typical Ti6Al4V HIP parameters include a soak time of two hours at 1688°F with 14.5 ksi argon pressure (920°C with 100 MPa). Accounting for heat up and cool down time, this HIP cycle can take less than eight hours, allowing two cycles per day on a two-shift work schedule. A typical case of wrapping each component in getter material adds time, cost, resources, and uses up to an estimated 50% of the load capacity. With the increased efficiency enabled by Quintus Purus®, clients have the opportunity to HIP 552,960 spinal implants per year (Tables 2 and Figure 3).
In conclusion, the growing Ti6Al4V market in the medical industry demands innovative developments to keep up with ever-increasing production volumes, whilst quality demands in lean production are becoming more significant. Solutions like the Quintus Purus® will allow manufacturers to have control over the quality of their titanium parts during a HIP cycle. It can be applied to produce alpha-case free components ensuring the optimal performance of orthopedic implants with increased service life.
References
Ahlfors, Magnus, Chad Beamer. “Hot Isostatic Pressing for Orthopedic Implants.” (2020): https://quintustechnologies.com/knowledge-center/hiporthopedic-implants/.
Allied Market Research Study performed for Quintus Technologies, 2022.
Benady, Amit, Sam J. Meyer, Eran Golden, Solomon Dadia, Galit Katarivas Levy.
“Patient-specific Ti-6Al-4V lattice implants for critical-sized load-bearing bone defects reconstruction.” Materials & Design 226 (Feb. 2023): https://www.sciencedirect.com/science/article/pii/S0264127523000205?via%3Dihub.
Kelly, Cambre N., Tian Wang, James Crowley, Dan Wills, Matthew H. Pelletier, Edward R. Westrick, Samuel B. Adams, Ken Gall, William R. Walsh, “High-strength, porous additively manufactured implants with optimized mechanical osseointegration.” Biomaterials (Dec.2021): 279, https://www.sciencedirect.com/science/article/abs/pii/.
About the Authors

Andrew Cassese is an applications engineer at Quintus Technologies. He has a bachelor’s degree in welding engineering from The Ohio State University.
Contact Andrew at andrew.cassese@quintusteam.com

Anders Magnusson is the business development manager at Quintus Technologies with an MSc in engineering materials from Chalmers University of Technology.
Contact Anders at anders.magnusson@quintusteam.com
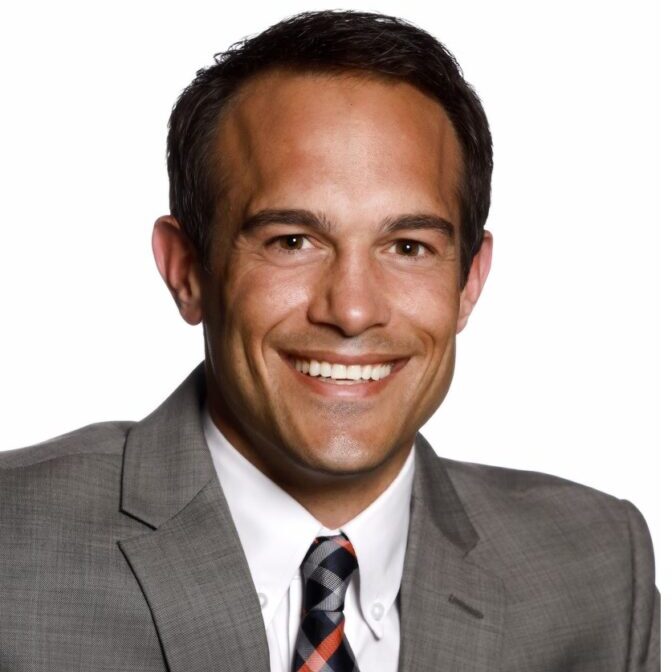
Chad Beamer is a senior applications engineer at Quintus Technologies, and one of Heat Treat Today’s 40 Under 40 Class of 2023 award winners. He has an MS from The Ohio State University in Materials Science and has worked as a material application engineer with GE Aviation for years and as a technical services manager with Bodycote. As an applications engineer, he manages the HIP Application Center located in Columbus, Ohio, educates on the advancements of HIP technologies, and is involved in collaborative development efforts both within academia and industry.
Contact Chad at chad.beamer@quintusteam.com
Find heat treating products and services when you search on Heat Treat Buyers Guide.com
HIP Innovation Maximizes AM Medical Potential Read More »