Heat Treat Radio #47: Justin Rydzewski and James Hawthorne on CQI-9 Rev.4 (Part 3 of 4) – Process Tables & New Resources
Heat Treat Radio host, Doug Glenn, conducts Part 3 of this 4-part series with James Hawthorne of Acument Global Technologies and Justin Rydzewski of Controls Service, Inc. about Revision 4 of CQI-9. We will hear about changes in process tables and key information on how to read this revision of CQI-9.
To find the previous episodes in this series, go to www.heattreattoday.com/radio.
Below, you can listen to the podcast by clicking on the audio play button or read the edited transcript.
The following transcript has been edited for your reading enjoyment.
Doug Glenn: Welcome everybody. In the first episode of CQI-9 Revision 4, we covered pyrometry and Justin mainly covered it because he’s the expert in this area. In the second episode, we spoke primarily with James and he shared about changes in the heat treat system assessments (HTSAs) and job audits areas. Justin, if you don’t mind, would you please review with us just exactly what CQI-9 is?
Justin Rydzewski: It has essentially three primary sections. You have your heat treat system assessment, which is often abbreviated as the HTSA; you have the pyrometry section; and then you have the process tables. The job audit is also something that needs to be completed on an annual basis, so it’s a minor section to the document.
DG: Today we’re going to talk about process tables and some other support portions of the spec. Let’s jump in. James, if you don’t mind, maybe you can talk to us a bit about what are these process tables and why are they important?
James Hawthorne: The HTSA covers the heat treat system and assessing that system. There are very unique processes that are covered by CQI-9. Those are captured in the process table section of the CQI-9 document.
Process Table A covers carburizing, carburnitriding, carburrestoration, austempering, and precipitation hardening or aging. You’ve got sections like B- this covers nitriding and ferritic nitrocarburizing. Then you have process table C which covers aluminum. Process Table D covers induction. Process Table E covers things like annealing, normalizing the stress relief. And we go all the way up to process Table I. So, there is a process table for each unique type of heat treat that is out there in the industry and this allows some very specific topics to be covered in those types of processes. They all cover pretty much the same thing, so I’ll go back just to run through the headers of Process Table A.
The first portion of it is Process and Test Equipment Requirements. What are the rules of engagement for those items? The same thing for pyrometry. There are specific call outs in the process tables. If this is part of your system, you have to play by these rules. Some of them will point you to specific sections of pyrometry. So, if you’re looking at the thermocouple and calibration of thermocouples, the process table is going to tell you that you shall conform to section P3.1 which covers all of those.

Source: Heat Treat Radio
It also covers the process monitoring frequency. How often do you have to check your temperatures? What are the rules of engagement? It calls out specifically each portion that may be included in that type of process. If you have a batch style furnace that covers that process, it has certain rules for you to manage your batch process. If it’s a continuous furnace, you have certain rules on how you would manage that continuous. If your process has an endothermic or exothermic generator or even some type of nitrogen methanol system, there are rules of engagement on how to manage or review that system for those items.
Then you get into things like inspection. Your in-process and final test parameters are also covered here. The last portion of it, in section 5 of the process table, is when you get into things like your quenchant and solution test parameters, and what are the rules for checking that.
What’s really nice about the document is that as you traverse the document, for instance, we have in the quenchant and solution test parameters, it’s A5.1. The next column over, it tells you what is the related HTSA question. It is set up in a way where you can go to the HTSA right from the process table and see if you’re compliant to what’s listed there as the shell statement and the requirements or the frequency for checking those.
DG: That answers another question we were going to address, and that is, how do those process tables work with the HTSA? It sounds like, in a sense, they are cross-indexed. Is that it?
JH: That’s correct, Doug. Like we spoke about in the last interview when we were talking about the job audit, the job audit is set up the same way: It has that same column, it tells you what the related question is, and it affords you the ability to easily traverse the document from the questions in the HTSA to the requirements in the process tables.
DG: Justin, anything else from you on that?
JR: The way that I typically frame it for people new to CQI-9 is that the process tables essentially define two things. First, your tolerances for process and test parameters, and second, your frequencies for those process test parameters in testing parts, which are specific to each heat treat process.
As James mentioned, there are nine process tables. The requirements in each of those process tables are going to be specific to that process. The requirements within the HTSA are intended to be broad and generic. They’re intended to be applicable to any organization performing one of those heat treat processes. As you go an HTSA, you will be notified when to refer to the process table for some specific aspect of the tolerance or frequency portion on that particular requirement.
DG: It sounds like a lot of work has been put into the cross referencing, making it simple and making it user friendly, right? So, whether you’re in the process or whether you’re in the HTSA, you can quickly and easily find the portion in the other section of the spec that applies to what you’re doing.
JH: That’s correct. Plus, it does afford you the opportunity to find compliance in a simpler fashion.
JR: And to also specify tolerances and frequencies that are appropriate for that given process. If I’m heat treating aluminum, I might have a tighter tolerance than that of hardening steel. They are very two different processes susceptible to different things, so the values need to be different.
DG: When you’re looking at the changes that were made from Rev 3 to Rev 4 with these process tables, is there anything that jumps out at you?
JR: I think one of the most notable changes is an item that wasn’t changed, actually, and that was the formatting and grading system retained from the 3rd edition. The primary focus of our efforts with the process tables this go-around was to enhance that clarity. The most notable change across many of the process tables was the added requirement to continuously monitor and record that temperature control signature for generators. So, for atmosphere generators, that temperature side of things needs to not just be monitored, but also recorded.
DG: Having taken just what we’ve heard today about the process tables, thinking back to what we covered in the last section on the HTSAs, and going back, Justin, even to your first episode that we did on pyrometry, it seems like there is a lot of stuff here. The CQI-9 comes in at 115 pages long, I’m guessing there are going to be people that start dipping their big toe into this thing and say, “What the heck? I’m struggling here! I don’t understand. What’s required of me?” From what we’ve talked about, before we hit the record button, there are some other very helpful things in this spec besides these table requirements and things of that sort.
Let’s talk about those a little bit. What are some of those other resources that will help simplify the execution of this spec?
JR: There’s a lot to it, but the underlying intent was not to confuse or bombard the organization with unnecessary rules and just allowing people to figure it out on their own. Everything goes through a “stink test” as we’re writing this up. Everything must make sense to us. If it doesn’t, it’s typically not added in or it’s refined and beat up until it is okay and then added in.
What can we do or what are the things that would be helpful to the end-user to make sure that they’re adhering to these things and that they understand to a point where they can adhere to it? It is not uncommon for me to find my customers having no problem following the rules so long as they know what they are so that can understand them and they make sense.
To convey that and get that buy-in, we’ve added a few elements and refined others. I think the most significant one, and it is in the section within the document that I reference most, is the Glossary of Terms. There is a lot of really good information in there. It’s not that I’m referencing the Glossary of Terms because I don’t understand what the word “calibration” means or what the difference is between a “control thermocouple” and a “monitoring thermocouple”, it’s how did we define those terms relative to CQI-9 in terms of CQI-9? How did we intend that word to be utilized? Sometimes you can find those little bits of detail that make it easier to understand or to capture what some of the requirements are for that are noted within the rest of the main document.
JH: There are also some illustrations added to the Glossary as well. There were a couple there before, but there was some refinement to those illustrations that were in there. Even those harder to define portions where we put those illustrations to help drive home the intent of the message, I think that was done very well in the Glossary section.
DG: Would you say, James, that that’s the major change to the Glossary, or are there other things that changed there?
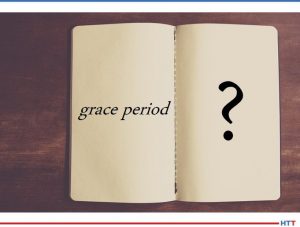
JH: We went through the entire document from cover to cover. There are many, many minor changes across the board, but there were some definitions that were added to the Glossary as questions came up during our normal meeting cycles, or that came from end-users when asking them how we should define something.
As those questions came in, we added those definitions to help with that guidance. Especially, as Justin said, as we’re talking in the meetings, if we’re hammering away at it and we have it digested in the room – we understand what we mean – how do we send this message to the rest of the users out there in the world? The Glossary ended up being a great place for items like that, as well.
JR: Right. So instead of using six paragraphs to describe a certain requirement or whatnot, just use proper terminology and then let’s define adequately those terms, which may be contested or not fully understood immediately, in the Glossary of terms so that there is a clear idea of what it is we’re trying to get across and not have to make this thing 185 pages.
[blocktext align=”right”]“In the context of this document [the CQI-9 revision 4], the following definitions shall apply.”[/blocktext]A real good example of things added into the Glossary would be terms that perhaps we all take for granted, terms that you understand what it means, but when you poll ten different people, their definitions are just slightly different. For example, “grace periods” was a word we added into the Glossary. Not that it’s an overly complicated term to understand, but relative to the document, it can have an impact on how it is you interpret those certain requirements and what it is that it means for you. “RTD” was another one added in there from a sensor standpoint. I think another that might get some attention is the inclusion of “sintering” and “sinter-hardening.” There was a fair amount of contention on the sintering side of things that CQI-9 wouldn’t apply. Then we included sinter-hardening, but we didn’t necessarily define the difference between the two processes. Now, there’s a distinction made, and it’s included in the Glossary.
DG: As far as the Glossary goes then, is there any guidance on when it should be used?
JR: Personally, I would say as often as possible. It is an incredibly overlooked portion of this document. It is amazing how much confusion can result just from misunderstanding a word that was used. Using the example of “grace period”; it’s not that I don’t understand what grace period means, it’s that I want to know what grace period means specific to CQI-9. How is it intended to be utilized? My definition might be different. I want to make sure that I’m lining myself with the definition of the word as it’s defined.
There is a statement at the beginning of the Glossary that says, “In the context of this document, the following definitions shall apply.” So, it’s within the context of this document. I may have a different context of that word, but it doesn’t matter what my definition is, it only matters as to how it’s defined within this book, the context of this document.
DG: That’s a good encouragement to have people refer to that Glossary. Even if you think you know what the word means, it’s probably not a bad idea to make sure that you understand how it’s being used in this document and don’t impose your own definition.
JH: There is one other thing I would offer, as well. I totally agree with what Justin is saying, and I think this speaks volumes or reinforces the things that we’ve talked about already on how one portion of the document supports the other portion of the document and supports the other side. This document, through and through, supports itself.
[blockquote author=”James Hawthorne, Acument Global Technologies” style=”1″]This document, through and through, supports itself.[/blockquote]
DG: Let’s jump to instructions. Probably the most important part of any spec or document is the instructions. Let’s talk about those for a moment, including maybe references, illustrations, figures, and things of that sort. Major changes? What should we know about instructions, references, illustrations and figures?
JR: There are support elements within the document that we’ve spoken about with the glossary of terms and what not, but there are also instances where instructions are called up… Step-by-step instructions on how to do something so that you can feel confident that you’re doing it correctly. For doing the HTSA (heat treat system assessment), there are instructions for completing that with the process for going about doing the assessment there, or even as simple as completing the cover sheet for the document or the job audit. There are instructions provided throughout to try to encourage and support someone’s effort in adhering to the requirements in the document.
DG: Let’s talk about references, illustrations and figures.
JR: Within the pyrometry section, specifically, there are a lot of instances of illustrations. For the system accuracy testing illustrations, the intent is instructional. It is to allow someone a means of seeing it visually both how it’s to be performed and how to correctly perform it.
Whether it’s a probe method A system accuracy test versus a probe method B system accuracy test, the illustrations included now are a bit more clearly refined. The focus was on eliminating anything that was unnecessary from that illustration to allow the user to more easily focus on those elements that are critical. The user will find a lot of improved illustrations throughout the pyrometry section.
You might have no issues performing a system accuracy test and you might have been performing them for some period of time. However, it’s still a pretty good idea to make sure that you’re doing it in the manner that CQI-9 requires in order to see if there is anything in there for added guidance and to make sure that you’re not overlooking something. That just includes simple math to perform one of those tests. Those are also illustrated to show progression of how to go about doing that test properly.
DG: Are there other resources within this spec that are available to help the user?
JR: If there is still confusion, it’s not hopeless. There are other means by which people can reach out to try to get clarification on different interpretations of requirements. James and I just recently participated in a roll-out where we had a Q&A for people to bring their questions regarding confusion around certain requirements. We provided answers from a clarity standpoint. That support doesn’t go away, nor is it just available at special events like the roll-out. At any time, people can, and often do, email into the AIAG with their questions, looking for guidance on certain matters.
If it’s as simple as- “I don’t understand question 214,” write in and ask the question and see if you can get some additional guidance. If it’s “I don’t understand pyrometry,” that’s a bit of a broader question and you’re probably not going to like the answer you get back (~chuckle~) and you’re probably not going to get what you’re looking for in the answer you get back, but there are many other sources for support outside of the document.
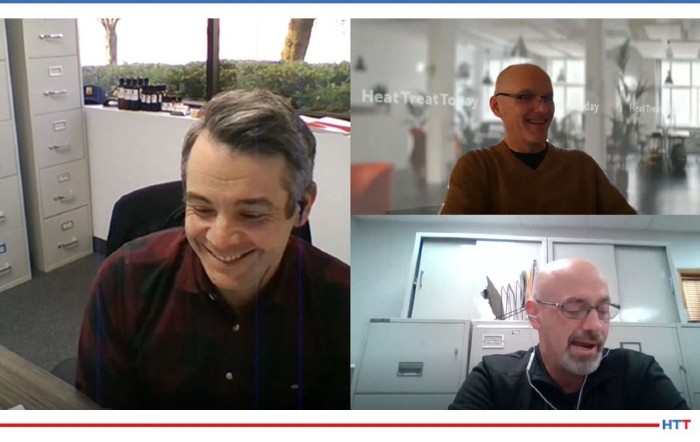
If the document doesn’t have enough, look outside the document. The AIAG is one of those sources. Your customer is another one. If you work with outside service providers (I’m speaking from my world of things – pyrometry), lean on them for guidance and things you don’t understand. I have my nose in these documents constantly, so my understanding of it is pretty alright. I can afford some additional guidance or interpretation.
I guess the advice I would have is don’t jump at something blindly and say “it’s going to be enough.” You’re going to want to have something behind you to give you a little bit more substance than that and to have some confidence in what you’re doing. Otherwise, it will have the tendency to snowball on you.
DG: Because these documents are “living documents”, they are continually evolving. Let’s say someone has a suggestion for a change that they would like to see made in a future Rev 5, what should they do?
JH: At the back of the book, we have what’s called a maintenance request form. The maintenance request form is a very short and sweet form that allows document users to submit for committee review what changes they believe should be made. This would give them the forum to always have their voice heard and how they feel, or believe, something should be managed.
To go back to what we were talking about, the CQI-9 technical committee still meets quarterly. As Justin alluded to, we had questions from the roll-out, but a good portion of our first post completion meeting was answering questions for the heat treater at large to help give that clarification. And, when we come across a question where we don’t really know what the person is asking or looking for, we give those questions back to our AIAG representative. They may reach out to that submitter to gain clarity on what was being asked so that we can give the best answer possible, not just potentially dilute it by giving an answer just of the sake of answering the question.
There is a lot of opportunity there and as these maintenance request forms come in, they will be handled. They’ll be handled with the committee and the group will work on it and develop the best answer. That answer may be, let’s look at making a change, whether that’s through some form of errata or by “putting it on the shelf” until – hopefully a long time from now – we look at a 5th edition. This gives us the ability to capture these things and make sure that it stays on out radar. We want to make sure that they’re taken care of with the urgency that’s needed.
JR: I think an item of note here, to make it clear, is any of those maintenance request forms that are sent in, all of them are reviewed by the technical committee. They are all reviewed. Anything submitted will make its way in front of that committee to be reviewed to on their agenda.
DG: What should these forms be? Is it just for document changes or for other things as well, for suggestions and whatnot?
JR: It’s for document changes as well as a suggestion box form.
DG: We’ve covered a lot in this third episode. We’re going to have a fourth episode that is going to deal with some practical tips from you guys on the actual execution of these things, but is there anything else that you would want to tell the listeners regarding the spec itself? Any other concluding comments?
JR: From a process table standpoint, this was something that was reiterated throughout the entire roll-out presentation: it really does take reading the entire document to capture all of the changes.
Some of them are quite minor and some of them stand out as being significant, but for the most part, they are minor, and sometimes minor ones can be very easy to overlook. There used to be requirements for calibrating your hardness testers on an annual basis. Those requirements have now been expanded to all lab and test equipment that require an annual calibration.
Another element that was included in the 4th edition was we made an effort to increase the clarity and guidance for the use of exceptions that are applicable to section 4 requirements of the process tables. For example, these would be used if you’re employing a surrogate test piece in lieu of sectioning some large or expensive product. If anyone is interested, the clarity is included on page 9.
But make note, these are not blanket requirements; these exceptions require customer approval and ultimately OEM approval, so they must be documented and approved by a customer and increased in your PPAP (Production Part Approval Process) control plan. There is a fair amount of added clarity on that topic, so it’s something people might want to take a look at and dive into just to make sure that they’re familiar with it.
DG: James, any concluding comments from your side?
JH: I think I’d just reinforce a little bit of what Justin was mentioning earlier. Read the document. Read as much of it as you can and try to understand as much as you possibly can. We made a lot of changes. Some of them are very minor, but some of those minor things could potentially be overlooked if you don’t step back and take a moment to understand the document and how each system, or each portion of the document, works with each other.
DG: The next episode is going to have some practical tips. We’re going to pick the brains of these two gentlemen on navigating Revision 4. You won’t want to miss it. There are going to be opportunities here to basically figure out some of the details.
If you have questions, feel free to send them in. You can email htt@heattreattoday.com if you have any questions and we may get those answered.
To find other Heat Treat Radio episodes, go to www.heattreattoday.com/radio.