Heat Treat Radio #37: Rethinking Heat Treating for the 21st Century with Joe Powell (Part 1 of 4)
In this 4-part series, Heat Treat Radio host, Doug Glenn, talks with Joe Powell of Integrated Heat Treating Solutions about bringing heat treating into the 21st century.
According to Joe, the real focus should be on the quenching portion of the process where distortion often happens. In many instances, distortion is able to be eliminated. Find out how in this episode.
Below, you can either listen to the podcast by clicking on the audio play button, or you can read an edited version of the transcript.
Click the play button below to listen.
The following transcript has been edited for your reading enjoyment.
Doug Glenn (DG): On today’s episode, I sit down with Joe Powell, president of Akron Steel Treating Company to hear what he and his team are doing to combat heat treat distortion. Joe Powell is a veteran in the industry and carries a wealth of knowledge with him. Joe, your company has 75 years of experience working with different part makers, and after a very brief conversation with you, pretty much anyone would conclude that you’re a man on a mission to bring heat treating into the 21st century. Before we turn you loose on that topic, first tell us a little bit about Akron Steel Treating and how it got started.
Joe Powell (JP): It was founded by my father in our garage in 1943 at the behest of the Department of the Army who wanted him to heat treat some parts, and it grew along with all the tool and dye makers in Akron, OH by making machinery for making various rubber products like tires, belts and hoses . . . you name it.
DG: You’ve also spearheaded another company: Integrated Heat Treating Solutions. What are you doing with that company?
[blocktext align=”right”]”It should be ‘quench treating’ not ‘heat treating.’ That’s the way I look at it.” -Joe Powell[/blocktext]JP: Integrated Heat Treating Solutions is the culmination of 75 years of commercial heat treating experience with literally over a 1000 different part makers. What we’ve learned that if we can integrate our heat treating solutions with the part-making design and the optimal material selection, we can produce better parts. And what I mean by “better parts” is they could be lighter, they could have longer fatigue life, and they could have less distortion after heat treating. All of these benefits are brought to the table to part makers so that heat treating becomes a fully integrated part of lean manufacturing.
Once heat treating becomes a lean, integrated part of manufacturing, everybody wins. It enables the use of leaner alloy materials; it eliminates oil quenching; it eliminates long carburizing cycles and batch carburizing cycles; and we now are able to literally do the heat treating in the manufacturing cell where the parts are made.
DG: What do those two companies look like now?
JP: We have about 50,000 square feet and are currently in the process of acquiring another building to our east. We have 48 employees and there are three shifts; and again, we do salt heat treatment, vacuum heat treatment and controlled atmosphere heat treatment. Also, we are currently getting into induction heat treating with our friends at Induction Tooling.
For the last 23 years, we have been concentrating on finding the best way to quench parts and to drive the distortion out of the part-making process. The heat treat distortion has been a problem for centuries. Parts crack, they distort, they come out of the heat treat process unpredictably with size change that is absolutely necessary to get the mechanical properties, but also, if it’s nonuniform, that size change can cause major problems down the line that have to be corrected by hard turning, grinding, flattening, straightening, you name it.

We’ve also delved into the science of computer modeling, finite element modeling as well as computation of fluid dynamic modeling with our friends at DANTE Solutions. What has happened from that modeling is seeing this concept: the surface of the part contains a bunch of grains, and those finite elements – if they are not quenched uniformly – will transform nonuniform, leading to nonuniform thermal shrinkage upon beginning quenched. Then they will also transform to martensite nonuniformly, which means that the thin and thick sections of a part will have different amounts of distortion and size change. In order to control that, we’ve developed what we call “quench to fit” technologies where we literally build a shell on the outside of the part, using a gas quench or a uniform salt quench or uniform water quench. Once you’ve built that shell in the first few seconds of the quench on the outside of the part, that martensite shell acts like a custom-made quench dye, and that custom-made quench dye allows the part core to cool by conduction through that shell. So, if that cooling by conduction happens by very uniform conduction through the geometry and the mass of a given part, you will have a predictable size change after heat treat. And, you will enable the part designer to go back to the initial part design and adjust it accordingly so that it quenches to fit during the quench process.
When a commercial heat treater receives the part, 99 times out of 100, that part is using a material that was selected many, many years ago, because that is what they’ve always used. Additionally, it’s going to be heat treated in legacy equipment that has always been used. For instance, case carburized 8620 steel valve seats have been used for decades now, and they last about 40-70 hours in the fracking pump, but a ductile iron valve seat can be made to last many times longer; it’s cheaper to buy the material and our heat treating equipment can heat treat it in 5 minutes instead of a 20 hour case carburizing cycle in batches. That single part flow of that new induction heat treating equipment and quenching equipment that is built into it can be built in right at the end of the CNC machines.
I am a commercial heat treater who believes that part design should be integrated for heat treating by the part-maker. It’s a nuance, but what it really boils down to is that sometimes commercial heat treaters do it best, but sometimes the part-maker can do it better. [Side bar quote: I am a commercial heat treater who believes that part design should be integrated for heat treating by the part-maker. It’s a nuance, but what it really boils down to is that sometimes commercial heat treaters do it best, but sometimes the part-maker can do it better.]
[blockquote author=”Joe Powell” style=”2″]I am a commercial heat treater who believes that part design should be integrated for heat treating by the part-maker. It’s a nuance, but what it really boils down to is that sometimes commercial heat treaters do it best, but sometimes the part-maker can do it better.[/blockquote]DG: So, the importance in the part design process of including the heat treater is that you can more consistently predict what the distortion will be, because if I understand it correctly, you can actually predict distortion in the part and therefore design the part with the distortion that will come consistently every time you design that part, yes?
JP: Yes. And it doesn’t matter if it’s an air quench or a hot salt quench or a uniform water quench, it just has to be very, very uniform from the initiation of the quench. In other words, you can’t take it out of the furnace and air cool it for 45 seconds and then begin a water quench, it doesn’t work that way. That shell is starting to form instantaneously when the heat is turned off. An air quench is very slow compared to an intensive water quench and so you have to introduce that quench all over the part surface shell as instantaneously, and with as much uniform impact, as possible. That’s what we do in terms of designing equipment to do the quench process.
DG: Right now, there are a lot of companies, a contractor or commercial heat treater, that send you parts to heat treat. Is it not possible that if the part designer and the heat treater talk in advance as they design the part, that some of these parts could be, in fact, heat treated in-house and not be sent out to a commercial heat treater? Is that possible?
JP: They could actually be heat treated not only in-house, but directly after the CNC machine, right in the manufacturing cell, right after the forge. It takes the proper selection of the optimal hardened ability material. In other words, part of that part design with the heat treater has to be considerations like, “Is it going to get too hard in the core? Is it going to swell up too much in the core? Is it going to be unable to build that shell on the surface without blowing it off, because the core starts to harden up?” So again, the optimal material selection and the design of the mass and the geometry of the part need to be considerations that the heat treater gets a chance to look at.
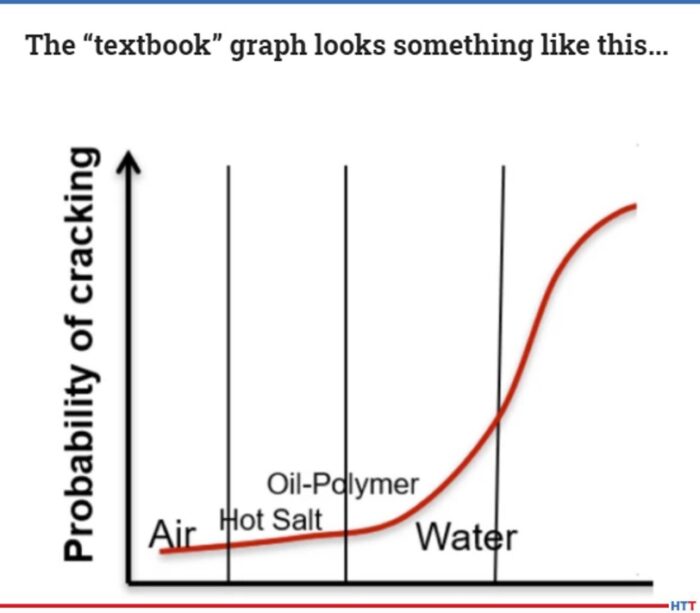
DG: So, if the part designer and the heat treater get together and talk about the part design before the part is finalized, or if they’ve got a legacy part, they can sit down and talk with a heat treater that understands what you’re doing over at Akron Steel and Integrated Heat Treating Solutions. If they can understand that, and if they can talk with you about how that part might be redesigned, it’s very possible that you could use lower cost materials to get the same thing, minimize the amount of time to actually heat treat, and you may be able to put that part in a single piece or at least possibly a small batch flow so that there’s not a bottleneck at heat treat, yes?
JP: Yes.
Sponsorship for this episode is Furnaces North America the Virtual Show.
DG: Joe, let’s talk about the quenching bell curve as it relates to distortion.
JP: There are many, many metallurgists and many metallurgical textbooks that indicate that the faster the quench cooling rate, the higher the probability of distortion. There is a curve that is generated that basically says that if you quench very slowly in gas, or if you increase that quench rate and go to a hot salt or a martemper bath or an austemper bath or you increase it even further with warm oil or highly agitated oil, or you go to a brine quench where you do a polymer or a polymer water quench where you increase the rate of quench cooling, there is a point at which most of the parts are going to crack and you’re going to have major distortion. It is not because of the quench speed being faster, it is because the uniformity tends to be less the faster your quenchant. In other words, you need to keep the water from film-boiling and creating a situation where the initial quench is actually done under a steam blanket, or gas, very slowly. Once the thin sections of the part quench-out under gas, then you have the thick sections that are still under that gas blanket, and you have very rapid cooling and very rapid martensite transformations that cause a shift in the size of the part where the shell now cannot contain the core swelling that’s happening underneath the surface.
Whereas 21st century heat treating practice is, what I call, a “uniform quench renewal rate” and an instant impact. In other words, you instantly impact the shell, create that shell, and once it’s created with uniform cooling, then the rest of the cooling happens by conduction through that shell. Whatever the geometry and the mass of the part is will determine that uniform conduction cooling which ends up being very predictable. Once it’s predictable, then you can morph the green size of the part before heat treating so that it predictably quenches to fit during the quench process.

DANTE Solutions has a method where they use their model to model the finite elements in the part so that the thin and thick sections of the part quench uniformly. IQ Technologies Inc. and my company, Integrated Heat Treating Solutions, have gone on the other side and shown that it is really a bell-shaped curve, and that the probability of distortion goes back down if you can create that shell on the outside of the part instantaneously, and then provide a uniform quench renewal rate to the part surface so that the core can cool by uniform conduction through that shell.
DG: Let’s just put in our listener’s minds the standard bell curve. Most of the quenching and most of the textbooks that we see these days is done on the left hand side of that bell curve, and as you approach the peak of that bell curve, the probability of distortion and/or cracking occurs. People are saying – don’t quench too fast because you’ll get cracking. You’re kind of switching the whole paradigm to say that it’s not the speed at which you quench, but more so: Can you create, almost instantaneously, a hard shell because of exceptionally rapid cooling on the whole part so that that shell basically holds the part in place? If you can get that, then you can cool the rest of the part, however slow or fast, in a sense, you want, because it’s not going to distort because it’s already locked in.
JP: Right, and this is cooling by conduction which is the physics of the material. How fast will it give up the heat through its mass? It’s the difference between 100 degrees or 50 degrees or 10 degrees per second of cooling and 400 to 600 degrees centigrade cooling per second, so it’s very, very intensive. The middle of the bell curve, where most parts are cracking, is because there is not a uniform quench renewal rate. You start off with a gas quench, then you end up with a very intensive evaporative cooling quench with nucleate boiling. You then end up with water quenching without boiling, and so you have three different phases of cooling happening on different parts of the part. This is exacerbated by different parts in different sections of the batch which will have different cooling rates.
It’s almost impossible to get the full benefits of very, very intensive quenching or even very, very uniform gas quenching in a vacuum furnace unless you have staged the cooling in such a way that you create that uniform shell at the beginning of the quench, and you hit that martensite start temperature and cool to that martensite start temperature all over the shell of the part uniformly. That’s the key.
DG: There are several things that jump into my mind like questions that might arise from people. You’ve already hit on the differences in part thickness – you may have thick sections, you may have thin sections. It’s very possible to maybe get down to the martensite start temperature on the thin section right away, but the thick section may not be, and therefore you’re going to distort because you haven’t created that “frozen shell” uniformly around the entire part. Let’s talk about, not just part thickness, but part geometry in the sense of the awkward curves and turns or lips and things of that sort on parts. How would we deal with that?
JP: That’s where new 21st century heat treating equipment needs to be designed. Every furnace company that is selling furnaces to either captive heat treaters or commercial heat treaters calls itself a furnace company. The reality is, yes, heating is important and it is the precursor to getting the mechanical properties, but the heat treatment is actually done, and the mechanical properties are actually obtained, in the quenching process. It should be “quench treating” not “heat treating.” That’s the way I look at it.

For the last 23 years that’s what has been more apparent to me. My dad taught me how to quench stamps that were used for marking the inside of tire molds, and these steel stamps would uniformly blow up if you just quenched them. But if you were able to uniformly quench the marking end, you could get it hard as hell and it would last a long, long time, but you had to kind of bifurcate the quench. You had to make sure that you created that shell in the marking area of the stamp and let the rest of the stamp kind of cool much more slowly. In other words, create the shell in the face of the stamp where the lettering is, and set those letters. Then the rest of the stamp can basically cool much slower because you don’t need the hardness there; it’s not the working part of the part.
Also, the designers of the stamps had to integrate the right radius in the face of the stamp. If they had sharp corners, those sharp corners would blow off during the heat treat. So, over time, we said, “If you don’t want us to crack this stamp, you’re going to have to put a radius over here and change the design slightly.” It didn’t take much change, but it did take a recognition of the fact that this was not going to work. There’s no way to eliminate the nonuniform cooling in the shell if you’ve got a corner. Steam collects in that corner and it doesn’t quench, so you can’t create the hardened shell.
DG: Let’s take a little deviation and talk about something non-metal. Let’s talk about the Prince Rupert’s drop to illustrate residual compressive stresses.
JP: The mystery of the Prince Rupert’s drop of glass is that glass makers noticed that if they dropped a drop of molten glass into a bucket of cold water it would form a drop that has a head and then a tail – it almost looks like a tadpole. If you hit the head of that glass drop with a hammer or try to break it with a pair of pliers, you can’t do it. It is literally unbreakable at the head. However, if you snap the tail off, it instantaneously explodes. This is because there are counterbalancing tensile stresses that are below the surface in the tail that once you break the compressive stresses off, it’s like taking the hoop off a barrel and the barrel staves explode; the elements on the surface just explode. The reason they don’t explode on the drop of glass at the other end is because there are sufficiently high compressive stresses on that surface that hold the drop of glass and keep it from fracturing.
DG: This is a fascinating video where you take a Prince Rupert’s drop, actually hang this Prince Rupert’s drop and shoot it with a .38 or a .45 or a 9 mm, hitting the head of that tadpole, if you will, and it shatters the bullet while the glass remains untouched. However, if a guy just simply takes his finger, or whatever, and snaps the tail, not just the tail shatters, but the whole tadpole blows up.
JP: What we’ve been able to do with all of the research that we’ve done is to harness those compressive stresses and make them available to the part-marker for making their parts more robust, making them lighter, and making them basically carbide hard and hammer tough. They don’t chip when hit with a hammer.
DG: Let’s jump back to some of the projects you’ve done at Integrated Heat Treating Solutions. Do you have any current projects that you’re working on where this integrated solution – where you were involved with part design or improvement of part design – worked well?
JP: Yes. There are several case studies. The first case study was a punch that lasts 2 – 9 times longer than an oil quench punch.
DG: A punch for what?
JP: Punching holes in metal plates. And the other thing that has happened is that since we’ve begun working with Induction Tooling, we’re able to then bring this down to the level of thinner parts and more complex geometry parts. We’re able to get more hardenability out of lean hardenability alloy such as ductile iron. Plain ductile irons are now acting as carbides. Even the people that make the material said it couldn’t be done, but we’re doing it.
DG: Can you give an example of that?
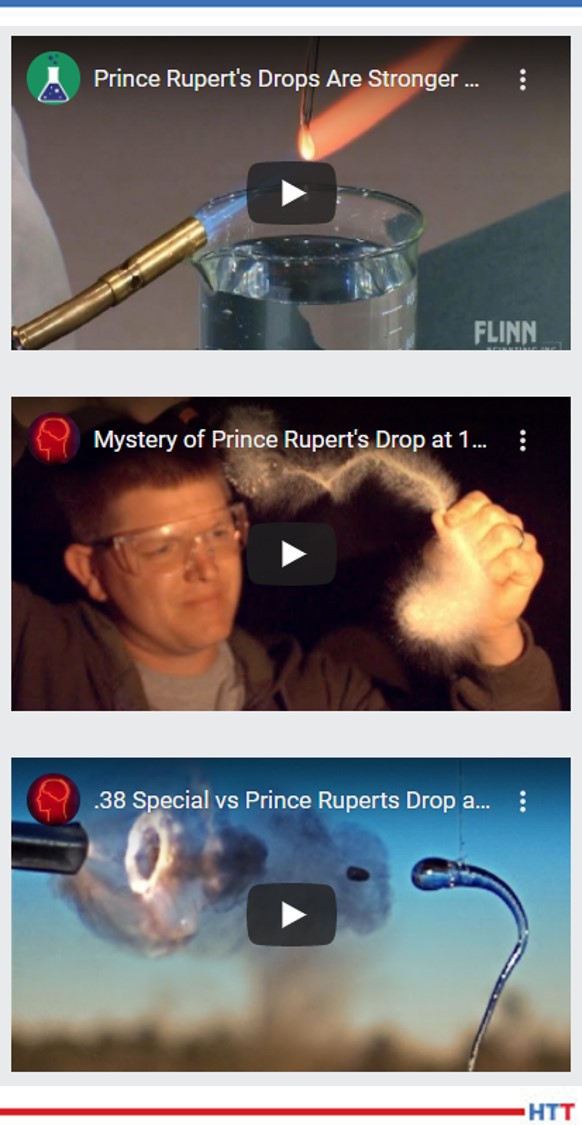
JP: Yes, that would be a fracking pump valve seat made out of ductile iron and heat treated with our special heating and quenching technologies.
DG: What was the performance prior to the treatment and afterwards?
JP: 40 to 60 hours and our initial testing we got 166 hours, so 2 ½ times longer.
DG: So 2 ½ times better performance on this fracking valve seat, and you were using the same material?
JP: No. Rather, we replaced an 8620 carburized steel that needed to be carburized for 20 hours in the furnace, and we did it with a 5 minute induction heating process.
DG: Of what type of material?
JP: Ductile iron.
DG: So we’ve got a punch, a valve seat in the fracking industry. What else?
JP: We have bevel gears that we do. We have worked with the part manufacturer and they’ve adjusted their CNC program so that it actually quenches to fit and doesn’t require a final grind.
DG: Expensive hard machining or hard grinding after heat treat.
JP: Right. And it saves them about $750 per gear in final grind costs. And, the gear lasts longer because it has high residual compressive surface stresses versus a standard carburization process and quenching in oil that does not have as high of a residual compressive surface stress. Especially after you grind it all off to get the final dimensions you want.
DG: Right. So you put all these nice hard stresses in, then you grind them off.
JP: Exactly.
DG: Any other examples?
JP: We have a company that wanted to have a weldable gear rack that could be welded on in the field on mining equipment that’s out on the side of a mountain. Because it might be cold up there, and they didn’t want to have to pre- and post-heat in order to weld on the gear rack, or repair a tooth on the gear rack, they wanted to have a material that had less hardenability but still wanted to have all of the mechanical properties. We were able to get the mechanical properties of 4330 from a 4130 material that doesn’t need to be pre- and post-heated to prevent it from cracking when welding it onto the machinery. They call that “field repairability.” So, we were able to enable field repairability and still maintain the mechanical properties’ requirements.
DG: In future episodes, we’ll go into some depth on some of those applications you just described, but before we wrap up things for this episode, is there a last impression you’d like to leave with us?
JP: Professor Jack Wallace* did not believe that there was a right half of the bell-curve, he did not believe that intensive quenching would work, but, again, he became a believer. It is all key to understanding the dynamics and uniformity of quenching over time. If you get the uniformity, you’re in good shape and eliminate a lot of heat treating problems.
DG: Thanks, Joe. Looking forward to you joining us for future episodes.
JP: Thanks so much.
*Professor Jack Wallace was the “Dean of the College of Metallurgical Engineering at Case Western Reserve University in Cleveland Ohio – who said in 1997, ‘Intensive water quenching would not work! – The parts will blow up in the quench!’ He became a convert once he figured out how compressive surface stresses worked during uniform quenching.” Information provided by Joe Powell.
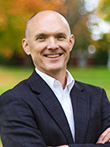
To find other Heat Treat Radio episodes, go to www.heattreattoday.com/radio and look in the list of Heat Treat Radio episodes listed.