Heat-Treatable SupremEX Alloy Gains 2nd SAE-AMS Approval
A heat-treatable aerospace grade aluminum composite used heavily in applications for national defense, aviation, and space was recently awarded AMS 4368 specification approval from the Society of Automotive Engineers – Aerospace Material specification Nonferrous Alloys Committee (SAE-AMS).
This is Materion Corporation’s second AMS specification for a SupremEX metal matrix composite.
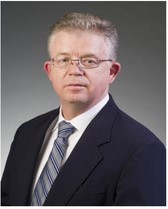
SupremEX® 640XA provides improved performance in aero-engine components and aircraft structures because it is 60 percent lighter than steel and 36 percent lighter than titanium, yet offers high strength, stiffness, and fatigue properties that significantly increase a component’s capability and useful life. The high-quality alloy is reinforced with 40 percent silicon carbide particles and is manufactured using a proprietary mechanical alloying process to ensure a homogenous reinforcement distribution. It provides a refined grain structure and enhanced mechanical properties, making it an ideal replacement for aluminum, titanium, steel and other structural alloys and composites.
SupremEX also provides superior damage tolerance and improved wear resistance when compared to conventional alloys. With a low coefficient of thermal expansion, components made of this composite will not deform over the range of temperatures experienced during flight.
“Other Materion aerospace-grade products have earned SAE-AMS specifications, including SupremEX 225XE, so we understand the value of this designation,” said W. Glenn Maxwell, President, Materion Performance Alloys and Composites. “With this specification, it’s much easier and faster for engineers to include the material in their designs and recommend it to new customers. In fact, many engineers will not consider using materials without SAE-AMS specifications.”
SupremEX 640XA is reinforced with 40 percent silicon carbide particles and is manufactured using a proprietary mechanical alloying process to ensure a homogenous reinforcement distribution. It provides a refined grain structure and enhanced mechanical properties, making it an ideal replacement for aluminum, titanium, steel and other structural alloys and composites.
Heat-Treatable SupremEX Alloy Gains 2nd SAE-AMS Approval Read More »