The Pros and Cons of Gas and Ion (Plasma) Nitriding
Source: AHTcorp.com
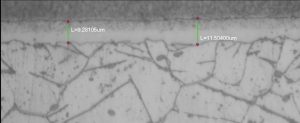
Engineers considering the advantages and disadvantages of surface treatments typically have a usable lifespan, surface hardness, and fatigue strength in mind. As a process, both gas and ion (plasma) nitriding avoid the issues involved with coatings and achieve similar metallurgical properties, and the compound zone increases corrosion resistance. But what are other areas in which the two processes can be compared, and what are their differences? It’s good to know, particularly since the latter could significantly make a direct impact on the end product.
Jacob McCann, a process metallurgist with AHT Corp., provides a specific list of pros and cons of gas nitriding and ion (plasma) nitriding in our Technical Tuesday feature for today.
Read more: “Gas and Ion (Plasma) Nitriding: What’s the Difference?”
Photo credit: Advanced Heat Treat Corp
The Pros and Cons of Gas and Ion (Plasma) Nitriding Read More »