Car Bottom Furnace Increases Large Component Heat Treat for Solar Atmospheres
Solar Atmospheres of Western PA recently commissioned their third car bottom air furnace. This Class 2 air furnace has a maximum operating temperature of 1350°F measures 60” wide x 38” high x 168” deep.
The newly installed equipment, manufactured by Heat Treat Equipment Inc., joins two other HTE car bottom furnaces that are 14’ long and 20’ long respectively.
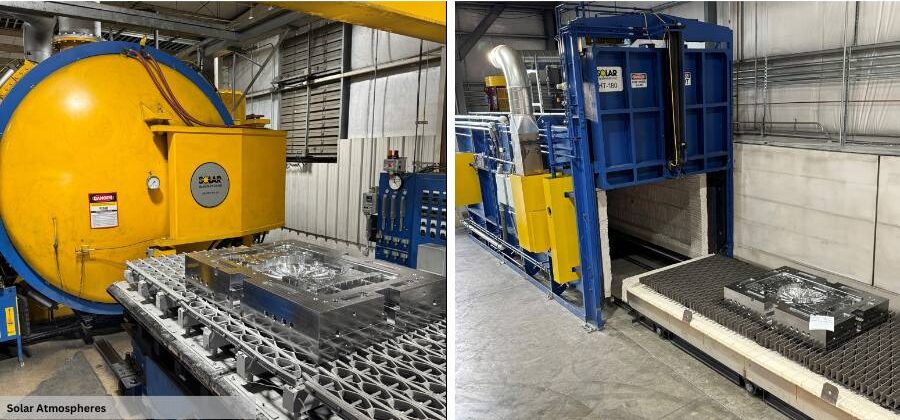
Source: Solar Atmospheres
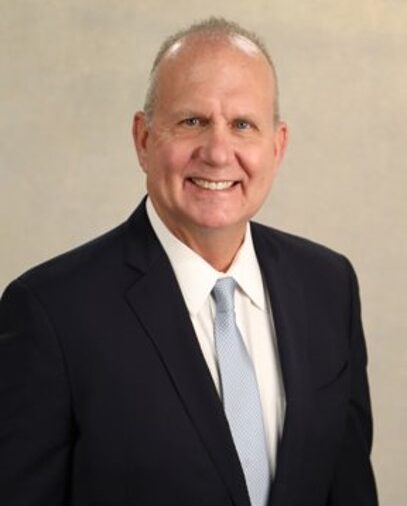
President
Solar Atmospheres of Western PA
Source: Solar Atmospheres
Bob Hill, president of Solar Atmospheres of Western PA and Michigan, states, “the addition of this large air tempering/aging equipment compliments our five (5) state of the art vacuum car bottom furnaces very nicely. Instead of hardening and triple tempering this 6000 pound H13 die exclusively in a vacuum environment, Solar can save our customers and our company over 100 hours of valuable and expensive vacuum processing time.”
He continues, “After successfully hardening in vacuum at 1850°F +/- 10°F, the fully hardened die was transferred to the air car bottom furnace for the triple temper operation of 1025°F +/- 10°F. These large and uniform car bottom furnaces are a win/win for both the customer and for production — not exclusively for heavy parts, but also when treating long components.”
This press release is available in its original form here.
Find Heat Treating Products And Services When You Search On Heat Treat Buyers Guide.Com
Car Bottom Furnace Increases Large Component Heat Treat for Solar Atmospheres Read More »