The Workhorses of Industry: High-Strength, Heat-Treated Bolts & Fasteners
Source: Bayou City Bolt
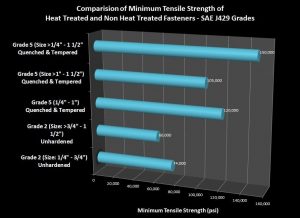
One would be hard-pressed to find an industry that isn’t served by high-strength or heat-treated bolts and fasteners. They are required in the automotive, construction, transportation, marine, aerospace, oil & gas, petrochemical, and presses and molds manufacturing fields. In oil & gas and petrochemical manufacturing, for example, high-strength bolts and fasteners are necessary in order to achieve seal closure on flanged joints, fittings, and closures; withstand tensile stresses within the bolts; and provide the strength needed for bolts and pins to withstand forces from high horsepower equipment. You name the industry sector, and the manufacturing process will be just as dependent upon bolts and fasteners to answer the demands of the equipment, the process, and/or the application.
In this overview of the importance of heat treating in fastener and bolt production, Bayou City Bolt provides:
- an explanation of the heat treating processes used depending upon the material and the application,
- a comparison of the minimum tensile strength of heat-treated and non-heat-treated fasteners (see image to the right),
- grade steels best used for heat treating fasteners and bolts,
- the case hardening process, and
- the proper use of hardened steel fasteners.
An excerpt:
“About 90 percent of fasteners are steel based and the required strength level is usually developed in steel fasteners using quenching and tempering processes. Accordingly, the terms “high strength” with “heat treated” or “hardened” are often equivocated with the fastener world. However, heat treatment includes a wide range of processes. Some heat treatments like annealing soften a metal, while others harden and strengthen.”
Read more: “Heat Treatment of Bolts & Fasteners”
The Workhorses of Industry: High-Strength, Heat-Treated Bolts & Fasteners Read More »