Special Steel Plant in Kapfenberg, Austria, to Boast Fully Automated Melting System
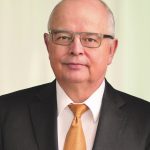
Since the official groundbreaking ceremony in April 2018, preparations for the construction of the world’s most advanced special steel plant in Kapfenberg, Austria, have been progressing rapidly. By awarding the contract for the electric arc furnace, the converter, and the secondary metallurgical systems—which represent the technological core of the plant—voestalpine has taken another important step in realizing the project.
The SMS group, based in Düsseldorf, Germany, will be responsible for the engineering, process technology, and start-up of the fully automated melting system, which will begin production in 2021.
“Awarding the contract for the supply of the main melting units, which represent around one-third of the total investment volume, lays the technological basis for the new special steel plant,” said Franz Rotter, member of the management board of voestalpine AG and head of the High Performance Metals Division. “The SMS group will contribute its comprehensive know-how to this project, both in the metallurgical systems and in the areas of digitalization and automation.”
In addition to the electric arc furnace, in which ultra-pure scrap and alloys are melted into liquid special steels at temperatures of up to 16232°F (9,000°C), the SMS group will also supply various after treatment systems that give the material its special properties. The units are operated with electricity from 100 percent renewable energy.”
The plant technology will set new standards worldwide in terms of digitalization. An ultra-modern sensor and electronic system enables the entire production process to be controlled from a central control station.
Special Steel Plant in Kapfenberg, Austria, to Boast Fully Automated Melting System Read More »