California Heat Treater Expands with New Furnaces, Endo Generator
A California-based, full-service brazing and heat treating company recently installed several pieces of equipment, including an indirect temper furnace as well as a generator that has clocked less downtime than the previous unit.
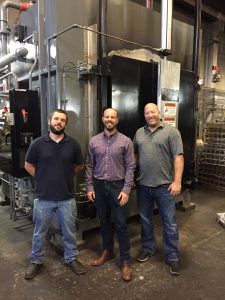
ThermoFusion’s investment of the 2200 Tru-Mix Generator and indirect temper furnace, both McLaughlin Services products, are part of the company’s commitment to support customers in the automotive, aerospace, medical, and energy industries, as well as for multiple other application.
The Tru-Mix 220 is supporting two of ThermoFusion’s internal quench furnaces and a high-temperature tool furnace, almost twice as much equipment as the generator it replaced. According to Glen Ottinger, president of ThermoFusion, the results were better than he had anticipated when researching the 2200 Tru-Mix and other gas generators.
The McLaughlin Indirect Temper Furnace was fully functional and ready for operations only two days after arrival, according to Nick Schreiber, quality manager at ThermoFusion, and has been surveyed at +/- 10F or less, between 300ºF and 1400ºF.
Photo credit: ThermoFusion
California Heat Treater Expands with New Furnaces, Endo Generator Read More »