OSU Scientists Develop Shape Shifting Material for Medical Applications
A small magnetic rose sitting between two copper coils in an Ohio State laboratory gives a demonstration of a new shape-shifting magnetic material developed by Ohio State researchers that will be used in biomedical devices, antennas, artificial muscles and robotics. The material can squeeze and grab objects and change its shape and temperature when electromagnetic fields are applied, according to the research paper published in December in the journal Advanced Materials.
Ruike Zhao, an author of the paper and assistant professor in the mechanical and aerospace engineering department, said the researchers embedded two types of magnetic particles into a soft material called a shape-memory polymer. At room temperature, the soft material is rigid, like acrylic. But when it comes within a magnetic field, the iron oxide particles heat up, softening the material so it’s like rubber, through a process called induction heating — the same technology used in some home cooktops.

Previous generations of soft materials needed a constant supply of energy, Zhao said.
“Once we deformed the [earlier] material, if we wanted to lock its deformed shape, we have to keep the external stimulation, which is not energy efficient.” She added that Ohio State’s new material is more efficient and can lift an object 1,000 times its own weight.
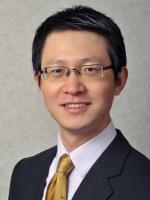
According to Liang Guo, an assistant professor in the electrical and computer engineering department, soft materials have existed for several decades. However, this new type of soft material with embedded magnetic particles is the first to be controlled wirelessly by magnetic fields. Guo stated that soft devices cause less stress on the surrounding skin and muscle tissues than similar mechanical devices. They also require less energy than similar mechanical devices.
Guo and Zhao previously worked together to create an insulin pump using soft materials that is one-third the size of current battery-powered pumps. The Ohio State team worked with researchers at the Georgia Institute of Technology to develop the polymer material.
OSU Scientists Develop Shape Shifting Material for Medical Applications Read More »