Métodos para la medición de la austenita retenida
La mayoría de quienes aplican el tratamiento térmico reconocen la importancia de medir la austenita retenida (RA, por sus siglas en inglés); no obstante, muchos optan por no realizar estas mediciones por razones de tiempo y/o de los costos asociados. Este artículo explica los motivos por los cuales se deben practicar las mediciones RA, los factores a favor y en contra de las tecnologías de medición tradicionales y los beneficios de realizar la medición en la planta misma, utilizando tecnologías más avanzadas.
This informative piece was first released in Heat Treat Today’s March 2025 Aerospace Heat Treating print edition. To read the article in English, click here.
La importancia del porcentaje de austenita retenida
Antes de entrar a examinar algunas metodologías de medición, es necesario entender lo básico en relación a la austenita retenida, al igual que la importancia que reviste el porcentaje de la misma (%RA).
Austenita retenida (RA) es el nombre que se le da a la austenita que durante el proceso de templado no se transforma en martensita. En términos sencillos, la austenita retenida (figura 1) ocurre cuando el acero se ha templado sin llegar de manera contundente a la temperatura de acabado de la martensita (Mf); es decir, la temperatura ha estado por encima de lo requerido para permitir la formación de martensita al 100%. Debido a que la Mf está por debajo de la temperatura ambiente en la mayoría de las aleaciones que contienen más del 0.30% de carbón, se pueden presentar cantidades significativas de austenita retenida en la martensita a temperatura ambiente. (Herring, Atmosphere Heat Treatment).
Al tratarse del %RA, con frecuencia existe un equilibrio muy sensible entre sus efectos benéficos (el aumento en la durabilidad de ciertos componentes manufacturados) y sus atributos negativos (la creación de piezas susceptibles de fracturas y averías). Por tal motivo es de crítica importancia que los tratadores térmicos logren el %RA óptimo para la aplicación deseada.
Por ejemplo, en las industrias de la aeronáutica y la astronáutica, con frecuencia se especifica que los niveles de RA sean inferiores al 8%, y para piezas como los cojinetes y los actuadores lineales, se requiere un RA por debajo del 3%, lo más cercano posible a cero. No obstante, en otras aplicaciones, como por ejemplo los engranajes grandes para generadores de energía, energía eólica y plataformas de rendimiento, se ha identificado que un RA en el rango del 15-30% reviste mayores beneficios. (Errichello et al., “Investigations of Bearing Failures”). De igual manera, un alto % RA es una ventaja en el caso de cojinetes que vayan a entrar en contacto con lubricantes contaminados.
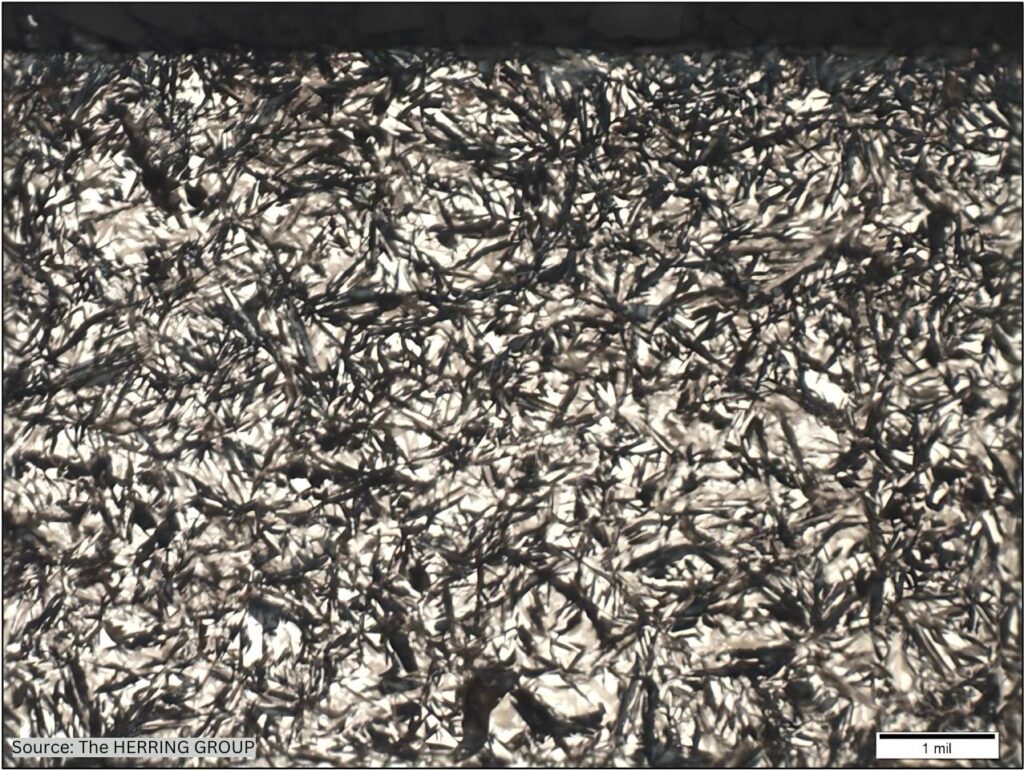
Marco DeGasperi, gerente técnico de Verichek, se pronunció al respecto señalando que el %RA es de crítica importancia para los inyectores de combustible, para piezas pequeñas en aplicaciones médicas y para aplicaciones de alto nivel y alto volumen tales como las placas de desgaste en la industria minera. Lo resumió afirmando: –Cuando tu ejercicio se trate de someter a presión y movimiento cualquier dispositivo de calibración fina…si utilizas la palabra “precisión” para darte a conocer, vas a querer hacerte a una [herramienta de medición del %RA].
Las mismas características que le dan a la austenita retenida muchas de sus propiedades particulares, son a la vez las respons ables de significativos problemas de funcionamiento. Sabemos que la austenita es la fase normal del acero a altas temperaturas, mas no a temperatura ambiente. Debido a que la austenita retenida existe por fuera del rango normal de su temperatura, es metaestable, lo que quiere decir que, cuando entre en funcionamiento, los factores como la temperatura, el estrés, y aún el tiempo, harán que se transforme en martensita no revenida. Es más, junto con dicha transformación se dará un cambio en el volumen (aumentará) generando un alto grado de estrés interno en el componente y provocando muchas veces la formación de grietas lo que podrá llevar a que las piezas fallen en el campo.
El % RA también es importante, no solo por el impacto sobre la estabilidad dimensional, sino además por las propiedades mecánicas tales como el límite elástico, la resistencia a la fatiga, la tenacidad, y la manejabilidad. (Herring, Atmosphere Heat Treatment). A manera de ejemplo, DeGasperi identifica en la industria automotriz las consecuencias de un %RA demasiado alto o demasiado bajo: –Hablemos de las piezas en una transmisión o en una caja de transferencia; aquí es donde se dan los casos en los que se empiezan a romper los cojinetes, o terminas viéndote en la obligación del retiro masivo del producto del mercado. Y por lo general toda la cadena de suministro identifica al anterior como el culpable cuando ninguno en toda la cadena se ha tomado la molestia de probar las piezas por sí mismo.
Por el contrario, en algunos casos, la RA diseminada en pequeñas cantidades aporta para que el material resista la propagación de fracturas por fatiga y disminuye el estrés por fatiga en el contacto de rodamiento, así que lograr el correcto equilibrio en la cantidad de RA es importante en muchas aplicaciones. Además, el % justo de RA es esencial para el control de calidad, al igual que para evitar problemas de seguridad y retiros masivos del mercado. El debido control y la medición precisa del % RA en las aleaciones de acero es un punto crítico para garantizar la calidad y la seguridad de los componentes terminados, salvaguardando así la reputación y el margen de ganancia tanto de los tratadores térmicos como de los fabricantes.
Métodos de medición de RA
El medir con precisión la RA es de vital importancia para establecer si existe el balance correcto entre la austenita retenida y la martensita en determinado componente. Los tratadores térmicos tienen a su disposición varias metodologías para esta medición, cada una con sus respectivas ventajas y desventajas. Para el tratador térmico entender la importancia de medir el % RA representa tan solo una parte de la batalla ganada, mientras que la otra parte se gana cuando se logra identificar un método de medición que sea rápido, preciso y rentable.
La difracción de rayos-X: el mejor y más preciso de los métodos
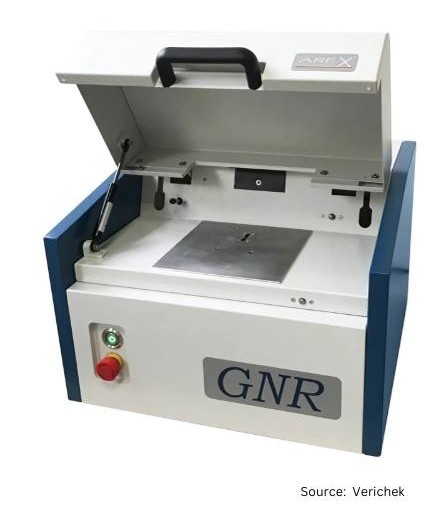
La difracción de rayos-X, utilizada para identificar y cuantificar las fases en un material, se considera el método más preciso de medición de RA en acero ya que logra establecer los niveles de RA hasta el rango aproximado de 0.5-1% (GNR, “AreX Diffractometer,” 3). En la difracción de rayos-X, las diferentes fases cristalinas demuestran diferentes patrones de difracción, lo que permite que sean identificadas y medidas. Además del análisis de fases, la difracción de rayos-X se puede utilizar para analizar car acterísticas microestructurales tales como la textura, el esfuerzo residual y el tamaño del grano.
Hoy en día, la difracción de rayos-X es una solución segura y no-destructiva que permite valorar una región mucho más amplia que la de varios de los otros métodos disponibles, sin necesidad de gran preparación ni análisis de la muestra, haciendo de ésta una solución más eficiente y efectiva. Es la tecnología más opcionada para una empresa que requiera valorar la RA con un resultado esperado inferior al 10%,
La actual generación de difractómetros de rayos-X ostenta un diseño de sobremesa con un peso aproximado de 25 libras. Existen modelos con costos inferiores a los USD $100.000, lo que los hace rentables frente al costo de un difractómetro tradicional (USD $200.000) que tenía además la desventaja de presentar dificultades cuando la muestra tuviera fases y reflexiones adicionales, ya fuera por el tamaño del grano, por los carburos o por las texturas que pudieran provocar disturbios y variaciones en la medición. La nueva generación de equipos de rayos-X logra superar estos obstáculos utilizando múltiples picos de difracción para minimizar los efectos de la orientación preferida y detectar la interferencia de los carburos.
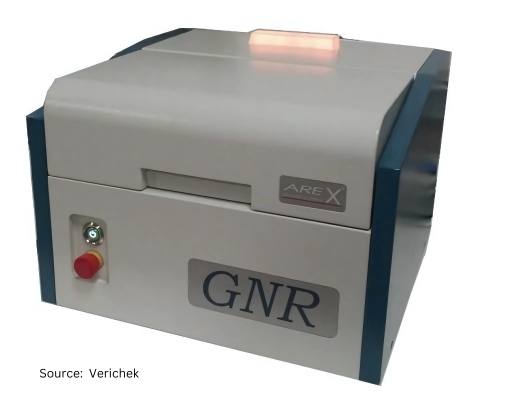
Las máquinas modernas de difracción de rayos-X tienen la capacidad de recoger hasta siete picos de difracción (tres para la fase ferrítica/martensítica y cuatro para la fase austenítica) para luego establecer la concentración de porcentaje por volumen de RA en la muestra al comparar las intensidades de los picos y analizar las relaciones entre éstos de acuerdo con el ASTM E975-22 (práctica estándar para la determinación por rayos-X de austenita retenida en acero con orientación cristalográfica cercana a la aleatoria).
No es complicado usar los equipos modernos de difracción de rayos-X. En menos de tres minutos se logra la medición con tan solo ubicar la muestra en la máquina y oprimir el botón de inicio. Estos difractómetros realizan mediciones en muestras de diferentes tamaños y se valen de software intuitivo, dando lugar a que cualquier técnico, tenga o no experiencia previa en metalurgia o difracción, efectúe la medición de manera rápida, precisa y eficiente.
La microscopía óptica: un método a prueba del tiempo
La RA se puede medir de manera metalográfica con un microscopio óptico. En la mayoría de los casos, un metalúrgico con experiencia puede establecer el %RA en el rango hasta del 10-15%, lo cual es más que suficiente para muchas aplicaciones, con el beneficio adicional de que también caracteriza la microestructura.
Este método, que implica establecer la fracción de austenita mediante el contraste derivado del comportamiento de grabado o morfología, es de bajo costo; sin embargo, puede ser demorado. En libros de referencia existen tablas y diagramas que ayudan a determinar el porcentaje de austenita retenida utilizando métodos comparativos. La microscopía óptica es subjetiva ya que depende del individuo y la interpretación que haga de la muestra bajo el microscopio.

Métodos alternos
Los tratadores térmicos también disponen de otros varios métodos de medición de la RA. Entre los más comunes se encuentran:
La inducción magnética: Aquí se magnetiza una muestra al punto de saturación y se mide la polarización de saturación. Con esto, se calcula la diferencia entre la saturación medida y la saturación teórica de la RA utilizando la ecuación.

La inducción magnética no es destructiva y ofrece un rango más alto y amplio que el de la microscopía óptica (1-30%). Sin embargo, al ser una medición de volumen, es necesario que el instrumento sea calibrado a los materiales específicos, junto con sus tratamientos térmicos y geometrías, lo cual exige mucho tiempo y depende en un alto grado de la habilidad del técnico.
Difracción de electrones por retrodispersión (EBSD, por sus siglas en inglés): Utilizar este método de medición de RA implica ubicar la muestra en un microscopio electrónico de barrido (SEM, por sus siglas en inglés) para caracterizar la estructura cristalográfica al igual que la microestructura. Las mediciones de RA con base en esta técnica no suelen ser muy precisas y dependen de la correcta preparación de la muestra. Adicionalmente, es un método destructivo y arroja una medida sobre un volumen muy pequeño.
En conclusión
El medir acertadamente el nivel de austenita retenida permite que tanto el ingeniero de diseño como el metalúrgico maximicen los efectos benéficos que ofrece, al mismo tiempo evitando sus consecuencias negativas. El tratador térmico, por su parte, deberá tener en cuenta la química del material y las variables del proceso de tratamiento térmico tales como la temperatura de austenización, la rapidez de enfriamiento, los tratamientos criogénicos o de congelación profunda y las temperaturas de templado.
Referencias
Errichello, Robert, Robert Budny, and Rainer Eckert. “Investigations of Bearing Failures Associated with White Etching Areas (WEAs) in Wind Turbine Gearboxes.” Tribology Transactions 56, no. 6 (2013): 1069–1076.
GNR, Analytical Instruments Group. “AreX Diffractometer: GNR Proposal for measuring Retained Austenite in the industrial domain and in laboratory.”
Herring, Daniel H., Atmosphere Heat Treatment. Volume I. Chicago: BNP Media, 2014.
Agradecimientos
Queremos agradecer a los siguientes contribuyentes por su aporte en el desarrollo de este artículo: Thomas Wingens, presidente y especialista en Heat Treat, WINGENS CONSULTANTS; Dennis Beauchesne, gerente general, ECM USA; Tim Moury, presidente & CEO, Marco DeGasperi, gerente técnico, Jeff Froetschel, vicepresidente y director financiero, Verichek Technical Services, Inc.; y Dan Herring, The Heat Treat Doctor®, The HERRING GROUP, Inc.
Find heat treating products and services when you search on Heat Treat Buyers Guide.Com
Métodos para la medición de la austenita retenida Read More »