Passing of Professor Hans M. Tensi: From Blacksmithing to 3rd Generation Heat Treating Metallurgy
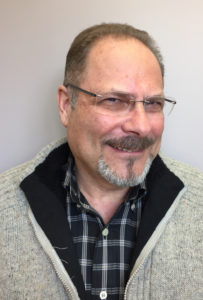
We Made A Mistake – We’re Making It Right Read More »
The Southeast U.S. facility of a heat treat supplier for the aerospace industry has received Nadcap approval for vacuum furnace brazing.
The Nadcap accreditation is the second in two years for the Greenville, SC, location of Solar Atmospheres’ operations; the facility received its first Nadcap approval in September 2016 to include low-pressure vacuum carburizing.
“Earning this Nadcap accreditation for vacuum furnace brazing reaffirms our commitment to providing our customers with quality services that meet the increasingly stringent requirements of the aerospace industry,” said Jon Collier, Quality Manager at Solar Atmospheres in Greenville, SC.
Nadcap Approval for Furnace Brazing Awarded to Southeast Heat Treat Facility Read More »
by David Pye, Pye Metallurgical Consulting
EDM is a tried and accepted, economical method of machining many different tool steels. This method of EDM machining can produce very intricate shapes can be machined to very accurate sizes.
However there are problems which can (and do) occur that are associated with the EDM process in relation to the final heat treatment of the die or tool.
It is most important for both the toolmaker and the heat treater to have an understanding of the resulting metallurgy and surface layer construction in relation to the final heat treatment.
Below is shown a schematic of both system principle and the resulting operation of the EDM process.
The final EDM layer is generally seen (microscopically) as follows;
The surface layer which is also known as The Recast Layer. This layer is at the immediate surface and is generally very hard and brittle. (Remember it has seen a very high temperature, which is up to the point of melting). The objective of the EDM is to vaporize the surface layer and remove it. But it is, in reality a melted layer which will cool rapidly at the surface of the tool. The surface is now in a highly residual and stress full condition which can and very often does, lead to cracking, heat checking and ultimately premature surface failure. More often than not, it is the heat treater who is blamed, no matter how careful the heat treater has treated the tool.
The untempered martensite transformation occurs due to the heat sink that takes place from the generated heat of the EDM. The generated heat energy diffuses into the body of the tool and creates the appropriate transformation from austenite into martensite because of the rate of cooling. This will give rise to a stressful potential crack occurrence condition (due to the untempered, unstable m fresh martensite). Hardness values of the untempered martensite layer can be as high as 62 HRC (depending of course on the chemistry of the steel).
Below the untempered martensite layer will be another layer of what can be a tempered martensite layer with hardness values (once again depending on the steel chemistry) in the region of up to 52 to 54HRC.
Below that layer on tempered martensite will be the original hardness and microstructure of the base material.
The recast layer is the dangerous layer, because not all of the melted layer has been flushed away. When a failed/cracked sample is etched, the recast layer will be seen as a white layer (do not confuse with the white layer of a nitrided surface).
What can be done to prevent (or at least reduce the risk of potential cracking)? The only simple procedure (but with no guarantee) that can reduce the risk of cracking, would be to temper the component immediately after the EDM procedure.
EDM and the Heat Treater Read More »
Source: Thermal Process for Gear Solutions
Read More: Hot Seat by Jack Titus
Vermont Custom Gage LLC. a subsidiary of Vermont Precision Tools Inc., Swanton VT, selected Lucifer Furnaces to create manufacturing capability with the addition of an air recirculating oven, a salt bath pot furnace and a quench tank. The new equipment will be used in the production of small steel component parts of their measuring (gage) equipment. The oven, a 4000 series, model 48-R36 with working dimensions of 24”Hx24”Wx36”L, heats to 800°F and will be used for Tempering. Insulated with 6.5” multi-layered lightweight firebrick and block insulation with a roof lined with ceramic fiber modules, the oven features a stainless steel liner which isolates the workload from the heating elements and directs airflow in a horizontal pattern. A high CFM fan assembly mounted through the oven rear wall circulates air over heating elements and back through the work chamber. The horizontal swing door is mounted with heavy duty hinges, 6” of insulation and two cam latches for a secure seal. After pre-heating, parts will be loaded into the salt pot furnace, model 2055-1624 and then oil quenched in a Lucifer Quench Tank, QT-2020, complete with air mixer, heater and soak timer. Next, the tools will be loaded into the 4000 series, model 48-R36 oven to be held at a constant temperature over a period of time to stabilize the structure of the steel. Vermont Precision Tools dba Vermont Gage manufactures a wide range of fixed limit gages including both threaded and cylindrical. Vermont Gage manufactures high quality gages with tolerances ranging from .00020” – .00002”. Vermont Precision Tools Inc. chose Lucifer Furnaces for the equipment based on its robustness and value.
Vermont Precision Tools Selects Lucifer Furnaces Read More »
[Best of the Web] Source: YouTube from The Science Channel
A 6-minute video shows how titanium is made. A great introductory video for those interested in learning more about titanium.
Watch by clicking here.
Titanium: How They Do It? Read More »