Magnetic Shield Manufacturer Commissions First Vacuum Furnace
A company that manufactures custom magnetic shields, precision sheet metal fabrication, and Hydroforming recently commissioned its first-ever vacuum furnace to accommodate expansions to better serve the magnetic shielding industry by providing material designed to protect sensitive electronics from magnetic fields.
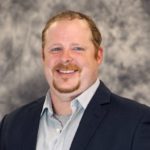
MuShield Company of Londonderry, New Hampshire, commissioned Solar Manufacturing to design the furnace, built with a SolarVac® Polaris control system, fully compliant to AMS2750E pyrometric specification, operating at a vacuum level of 10-5 Torr with the capability of maximum temperatures up to 2400°F, and featuring an external quench system designed for pressures up to two bar.
“What this means for us is that we’ll be able to offer quicker turnaround times on heat-treated products, fit larger shields into our furnace, and eliminate outside vendor work,” notes MuShield’s website.
“MuShield was already aware of our excellent reputation in the industry, and they were impressed with our facility when they visited earlier this year,” said Jason Davidson, Solar Manufacturing’s northeast regional sales manager. “They were also impressed with results of testing performed for them by Solar Atmospheres, so we’re pleased they have placed confidence in Solar Manufacturing to provide their first vacuum furnace.”
The new vacuum furnace will also allow MuShield to perform stress relief annealing cycles on hydroformed parts made from non-shielding alloys, which is a manufacturing requirement on most materials that the company hydroforms.
Magnetic Shield Manufacturer Commissions First Vacuum Furnace Read More »