HART-TECH has expanded its capabilities with a vacuum furnace that will allow for the heat treatment of multiple steel types and the ability to implement a wide range of processes, from hardening through vacuum carburizing and carbonitriding. The furnace will efficiently heat treat large loads of research, test, and production elements.
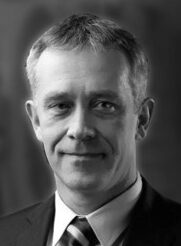
Vice President of Business of the Vacuum Furnace Segment
SECO/WARWICK
The commercial heat treater has previously incorporated over 10 SECO/WARWICK processing solutions. This system is being provided to work on the implementation of vacuum carbonitriding technology services that HART-TECH can now offer to a wide range of clients.
“We can say that we have a kind of synergy with the HART-TECH hardening plant,” said Maciej Korecki, vice president of the SECO/WARWICK Group’s vacuum segment. “Our partner, just like us, loves science, research, and development, and the common curiosity about the world motivates us to create further innovations.”

Management Board CEO & Technological Dept Head Director
HART-TECH Sp. zo. o.
“This solution will help us to put into action a project concerning the implementation of vacuum carbonitriding technology at the HART-TECH plant with our customers in mind,” said Dr. Eng. Robert Pietrasik, president of HART-TECH. “We want to implement the low-pressure carbonitriding process and be able to use it in mass production.
“By expanding the machine park with a new vacuum furnace,” Dr. Pietrasik continued, “we will also significantly shorten the waiting times for heat treatment for our current and future customers. The large workspace will significantly increase our capabilities for processing elements hardened in gas. Thus, we will be able to gradually switch from hardening elements in oil to hardening in gas, which is more efficient, cleaner and ensures smaller deformations.”
The vacuum furnace supplied to the company has been enhanced with a gas system equipped with two acetylene mass valves, a hydrogen mass valve, and an ammonia mass valve. The furnace can use three gases for various technologies: acetylene, hydrogen and ammonia. HART-TECH specializes in hardening, carburizing, nitriding, sulfur nitriding, steel tempering, supersaturation and aging, annealing, vacuum brazing and low-friction layers, and hardening of machine and tool elements.
The press release is available in its original form here.