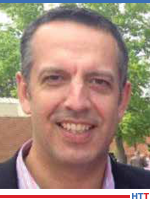
A clash of generations may be inevitable at family gatherings, but in the heat treat shop, everybody is on board with the changes that have developed over the last few decades: technological advances in equipment and processes, enhanced quality control, greater awareness for safety issues and green operations, among others. Peter Sherwin of Eurotherm by Schneider Electric traces the course the industry has taken out of the past and into the future. This article first appeared in Heat Treat Today’s March 2019 Aerospace print edition.
My first experience in a heat treat shop could be described as your grandfather’s shop—it was dirty and dusty, and you had to be alert to avoid danger. A handful of paper chart recorders were present, and tempering ovens were controlled by a dial indication of temperature, adjusted up and down to find out the current temperature. Only manual flow controls existed. Process temperature, times, and flow-rates were handwritten on small paper cards and stored in a filing cabinet.
Fast forward 15 years and the shop has clean processes, mostly vacuum-based equipment, and all automatically controlled process cycles. Shop floor instructions moved from paper to entirely computer-generated, an industrial transformation to the digital-age that took place in the 1990s and 2000s.
How We Got Here
So, what have the last couple of decades brought? Shakespeare’s Much Ado About Nothing springs to mind. First, we had the painful hangover from the global recession in 2008-09 which, for the next half-decade, had everyone consumed with operating as lean as possible with only a slow trickle of investment. The last few years brought a healthy rebound in manufacturing and increased heat treat production requirements. However, this surge in activity and a continued make-do attitude did not allow the time or motivation to refurbish or replace aging equipment. Add to this the promise and “soon-to-be-fulfilled” prophecies of IoT and Industry 4.0, the coming of age of the electric car, and the resultant effects on heat treatment requirements, and all of these factors conspire to make the heat treater think twice about rushing into investing in new furnaces or upgrading the existing plant.

The curse of this is watching the average life of equipment catch up with the average age of operators, and we are transported back to the dark ages of your grandfather’s shop.
Admittedly, this is an over-simplification of the current situation—not all plants are stuck in this rut. Contrary to the above, AMS2750D (released 2005) was a boon to European furnace OEMs and associated suppliers, and yet this was not a worldwide phenomenon because the U.S. received a “grandfathered” pass due to the heavy involvement and prior investment in meeting AMS2750C requirements.
Over this same recent period, the final aerospace customers (aerospace primes and engine manufacturers) have not rested on their laurels. A rise in the middle class in Asia has fueled a healthy increase in demand for passenger aircraft and allowed best-in-class suppliers to invest, innovate, and develop more energy-efficient aircraft. Younger airline brands in the Asian continent have been able to rapidly take market share by leveraging a lower cost base created mainly by engine technology improvements.
Engine Developments and Quality Control
The A320neo, available since 2015, incorporates new, more efficient engines and large wing tip devices called “Sharklets” delivering significant fuel savings of 15 percent, which is equivalent to 1.4 million liters of fuel per aircraft per year, or the consumption of 1,000 mid-sized cars. In addition, the A320neo provides a double-digit reduction in NOx emissions and reduced engine noise. [1]
The 737 MAX 8 reduces fuel use and CO2 emissions by 14 percent over the newest Next-Generation 737 and 20 percent better than the first Next-Generation 737s. Also, the 737 MAX 8 uses 8 percent less fuel per seat than the A320neo. [2, 3]
The GTF engine has met all performance specifications since entry into service. For example, the GTF-powered A320neo has achieved a 16% reduction in fuel consumption, a 75% reduction in noise footprint and a 50% reduction in nitrogen oxide emissions. [4]

These significant recent engine innovations have been possible through the use of modeling software to aid fast development (versus slow in-field trials) and by maximizing the overall performance via a mix of standard and exotic materials. Future developments include evaluating the use of actual component properties (e.g., tensile test, hardness profiles, other material, etc.) rather than relying on industry averaged properties. These advancements could lead to substantial changes in shape design and associated weight reduction but would require more stringent processing control.
Nadcap accreditation and the SAE AMS2750 standard have been used to manage a specific quality output from the heat treat supply chain. Even with the expected release of AMS2750F, control tolerances are not anticipated to change dramatically. This situation could create tension between the ongoing innovation on the design-side and the slower-development in process equipment capability. Let’s hope this doesn’t result in a path back to individual prime requirements over-shadowing the unified AMS standard.
Heat Treating 101 for the Shop of the Future
So, it’s back to the heat treat shop and the conundrum of upgrading/updating equipment due to age, performance, capability, and now the added twist of potential changes in future customer requirements. What strategy should a heat treater undertake?
Refurbishment of existing equipment to help lower running costs and improve capability can usually occur with updating the control and automation system. By looking at the Total Cost of Ownership (TCO) rather than just the “ticket” price of the upgrade, the payback for the investment can be in months rather than years. Control systems can improve the uptime of the equipment and precision control can positively impact quality results and even shorten process times in some instances. The relatively low payback time can ease the decision to invest.
Investment in new equipment requires a more detailed look at the customer base and changes within the external environment. To help with this uncertainty, some OEMs are starting to provide flexible financing solutions, including leasing. Control and automation suppliers are also doing their bit by designing control and recording instruments that can be enhanced by secure over-the-air software updates rather than requiring a complete change of hardware.
Conclusion
The shops of the past are looking less and less like the shops in most plants today, but it’s more than just physical changes that reflect a forward-looking operation. Today’s shop can leverage innovative thinking about cost of operations, improve the quality of communication with customers and suppliers, effectively use control systems, and be creative about equipment upgrades. These are changes that begin with an attitude adjustment—having the right view of the past and a broad vision for the future.
References:
[1] “Airbus, Indigo places order for 130 A320 neo”, https://www.airbus.com/newsroom/press-releases/en/2011/06/indigo-firms-up-order-for-150-a320neo-and-30-a320s.html
[2] Retrieved 01-Feb-19 https://www.boeing.com/commercial/737max/by-design/#/leap-1b-737ng-737max
[3] Retrieved 01-Feb-19 https://www.cfmaeroengines.com/engines/leap/
[4] Retrieved 01-Feb-19 https://www.pw.utc.com/products-and-services/products/commercial-engines/Pratt-and-Whitney-GTF-Engine/
About the Author: Peter Sherwin, a Chartered Engineer, is business development leader with Eurotherm by Schneider Electric, recognized for his expertise in heat treat systems technology, IIoT, Industry 4.0, and SaaS/digital solutions. This article, which originally appeared in Heat Treat Today’s March 2019 Aerospace print edition and is published here with the author’s permission.