A French manufacturer of high-performance automobiles has developed the largest titanium functional component produced by additive manufacturing in a 45-hour process that includes heat treating to achieve minimum weight with maximum stiffness.
The development department of Bugatti Automobiles, S.A.S., which established itself as a pioneer for new technical developments and innovations in the extreme performance sector of the auto industry with the Veyron and Chiron super sports car models, recently announced the successful design of an eight-piston monobloc brake caliper that can be produced by 3-D printing. Bugatti, in cooperation with Laser Zentrum Nord of Hamburg, bypassed aluminum and turned to aerospace-grade titanium alloy, with the scientific designation of Ti6AI4V, for a tensile strength of 1,250 N/mm2. This means that a force of slightly more than 125 kg (276 lbs.) be applied to a square millimeter of this titanium alloy without the material rupturing.
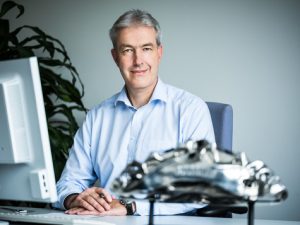
The development time for the 3-D-printed titanium brake caliper was about three months. The basic concept, the strength and stiffness simulations and calculations and the design drawings were sent to Laser Zentrum Nord by Bugatti. The institute then carried out process simulation, the design of the supporting structures, actual printing and the treatment of the component. Bugatti was responsible for finishing.
The printing process results in a brake caliper complete with supporting structure which maintains its shape until it has received stabilizing heat treatment and reached its final strength. Heat treatment is carried out in a furnace where the brake caliper is exposed to an initial temperature of 1,292°F (700°C), falling to 212°F (100°C) in the course of the process to eliminate residual stress and to ensure dimensional stability.
The new titanium brake caliper, which is 16.2 in. long (41 cm), 8.2 in. wide (21 cm) and 5.4 in. high (13.6 cm), weighs only 6.4 lbs. (2.9 kg). In comparison with the aluminum component currently used, which weighs 10.8 lbs. (4.9 kg), Bugatti could, therefore, reduce the weight of the brake caliper by about 40% at the same time as ensuring even higher strength by using the new part. The result is a delicately shaped component with wall thicknesses between a minimum of only one millimeter (.039 in.) and a maximum of four millimeters (.157 in.).
“It was a very moving moment for the team when we held our first titanium brake caliper from the 3-D printer in our hands,” said Frank Götzke, head of New Technologies in the Technical Development Department of Bugatti Automobiles S.A.S, which is a brand of Volkswagen AG. “In terms of volume, this is the largest functional component produced from titanium by additive manufacturing methods. Everyone who looks at the part is surprised at how light it is – despite its large size. Technically, this is an extremely impressive brake caliper, and it also looks great.”
The first trials for use in production vehicles are due to be held in the first half of the year.