Electrification is afoot and is claimed to be a more sustainable heating source than natural gas. Art Moslow, electrification project manager at Kanthal Heating Systems, discusses challenges and options when switching heat treat operations from gas-fired to electric with Doug Glenn, Heat Treat Today publisher.
Below, you can watch the video, listen to the podcast by clicking on the audio play button, or read an edited transcript.





The following transcript has been edited for your reading enjoyment.
Kanthal® and Electrification (00:00)
Doug Glenn: I’d like to introduce today, Arthur (Art) Moslow. Art is with Kanthal Heating Systems, and Art, first off, welcome to Heat Treat Radio.
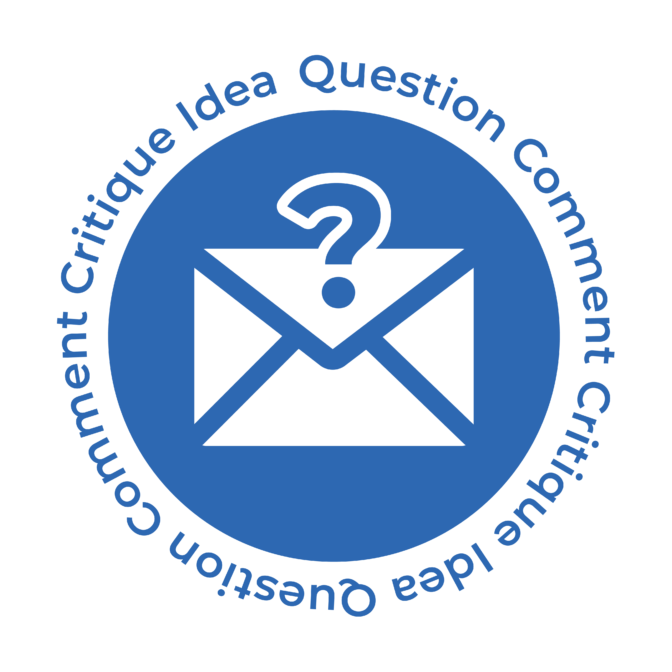
your Reader Feedback!
Art Moslow: Thanks for having me.
Doug Glenn: Art, just to give people a sense of your background, you are currently an engineering and communications professional for Kanthal, but you’ve been with them for 20+ years. And, I think, electrification project manager for Kanthal Heating Systems is where you are.
Art Moslow: That’s correct, Doug, for a little over 22+ years with Kanthal.
Doug Glenn: Great, that’s good.
I’ve got a few questions for you. One of them is: Is Kanthal seeing a lot more inquiries now about electrification than they have had in the past?
Art Moslow: It is a significant increase. And I just want to say thank you for the opportunity to meet with you, Doug, and discuss this — what would be viewed as a very important topic.
Over the years, Kanthal has assisted many companies and industries with the exploration and implementation of gas to electric conversions.
Initially, it was a demand from “heavy industry.” That’s kind of an industrial term that means very large projects in the steel and petrol chemical industries, and they’re typically looking for megawatts of power, which is a lot of power.
Over the last few years, we’ve seen a significant increase from other industries like air pollution control, calcination, and heat treating.
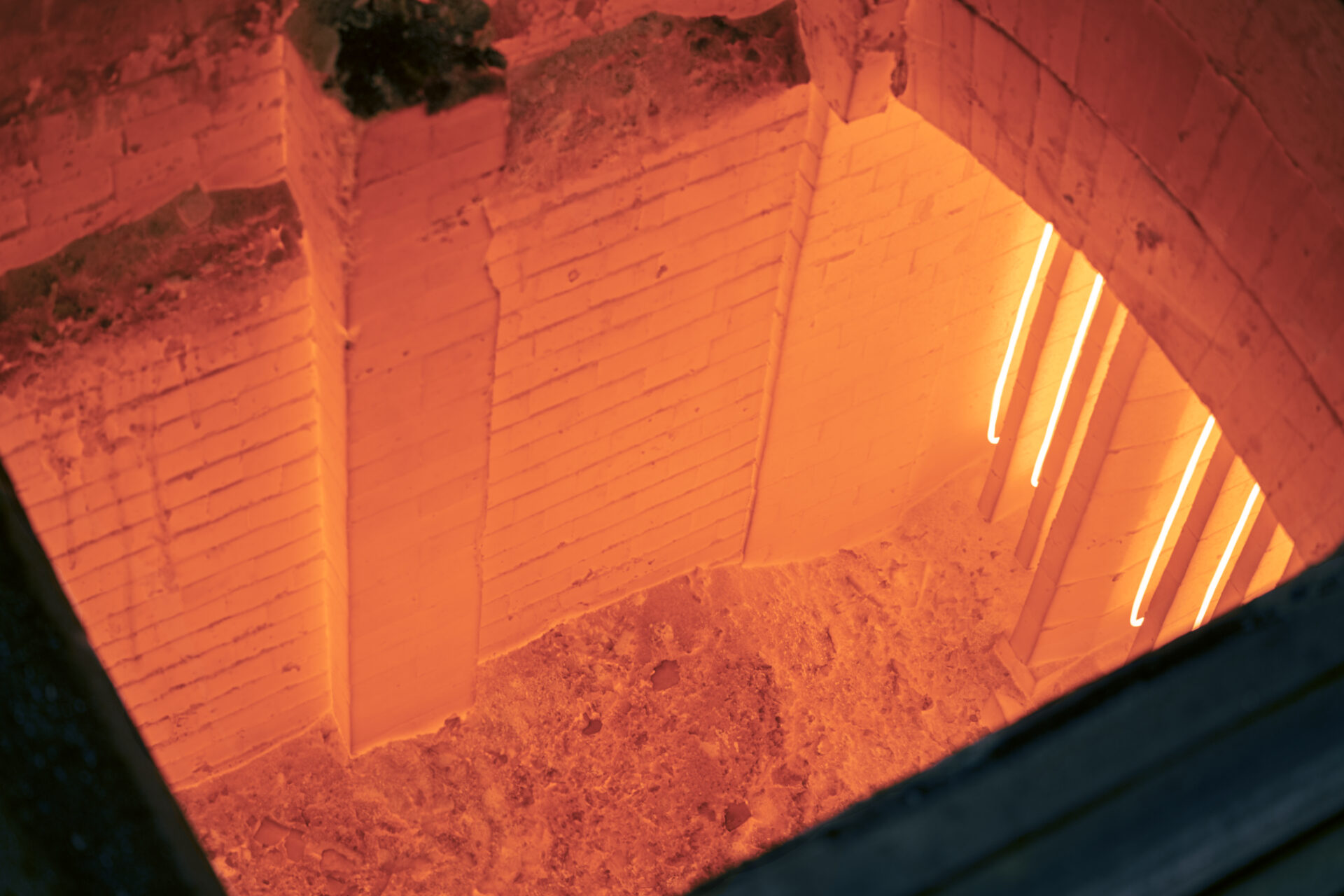
Source: Kanthal
Heat treating represents a great opportunity for converting from gas to electric. A lot of furnaces have indirect-fired gas burners, heating tubes that then heat the furnace — so it’s radiant heat — and it’s primarily a big form of heat transfer for electric heating.
Kanthal has formed, in the last year and a half, a new group. It’s a global group within our company of sales engineers to assist all our different sales areas with gas to electric conversions. We saw that as a significant need. Our sales area and our clients were looking for more support. That’s the group that I head at Kanthal.
Doug Glenn: I assume, if they formed this group, activity is up.
The bulk of our audience are captive heat treaters, manufacturers who do their own in-house heat treating/thermal processing of some sort. What are some of the issues that they’re facing regarding decarbonization?
Art Moslow: Well, a lot of companies have global initiatives for sustainability. It’s not just an individual location, it’s more of a corporate initiative. Every facility, every location, is looking to contribute to their corporate goals of sustainability. We see in a lot of industries that a lot of furnace production or heat processing contributes significantly to CO2 emissions.
A lot of these companies have multiple furnaces at each location, and an ideal way to reduce their CO2 emissions is by converting from gas to electric. It’s something they can contribute to their corporate goals and objectives.
Electric Incentivization and Utility Companies (05:05)
Doug Glenn: Would you say the bulk of the activity that you’re seeing is being driven by regulation or by efficiency improvements? What’s the motivation?
Art Moslow: I’m not really a regulations expert, but there are a lot of local regulations where companies are being incentivized a little bit. In fact, there are some government agencies in the U.S. that are incentivizing clients to switch from gas to electric.
We have worked with utility companies — this is a little bit new for us — coordinating with utility companies that are incentivizing their clients to use electricity. The utility company wants to sell more electricity — they have a sales team — and so they work with their customers to help offset some costs to modify the furnace and upgrade furnaces to electric.
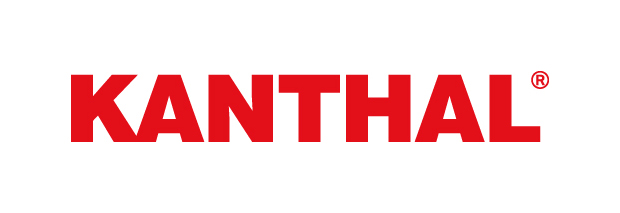
Doug Glenn: It is odd about the utilities. I’ve had experience with a number of utilities that are involved with the Industrial Heating Equipment Association (IHEA). They even have programs to help you reduce the amount of electricity that you use. Even though they are the sellers of electricity and they want you to use more, they actually are concerned with people being more efficient because they can’t take the load. The amount of electricity that’s being required these days is amazing.
Your point is good: Utilities are, in fact, providing incentives to companies to help them electrify.
Art Moslow: They provide incentives. A few of the utility companies that we have contact with have test labs where they’ll test equipment to prove out a solution to see if it’s something they can provide to multiple industries.
They might have a test unit to invite their customers to view it.
They’ll help source clean energy too. It’s always important when you’re converting from gas to electric, not just to shift the carbon footprint somewhere else by using “non-clean” energy — you’re just shifting it to another location, and you’re not really contributing.
Utility companies will help to source clean energy. So, when you’re converting from gas to electric, you’re reducing your CO2 footprint, and the utility companies providing you with clean energy help reduce the CO2 emissions.
Obstacles to Electrification (07:56)
Doug Glenn: For these manufacturers who have their own in-house thermal processing or heat treating, what are some of the major obstacles that they must overcome in order to get to a point where they can potentially be converting from gas to electric?
Art Moslow: A lot has to deal with challenges related to the idea of change. How can Kanthal really help and assist our clients to change?
You know, gas-fired systems work. We’re not coming in to say, “This doesn’t work, switch to electricity.” That’s not what we’re promoting. What you have does work.
It’s thinking of how we can improve the idea of sustainability and reduce CO2 emissions. We can help you do that, and it’s up to Kanthal to explain that and overcome those kinds of challenges. We prove to a client that this technology does work, and it doesn’t impact your furnace process. Switching from gas to electric does not mean now you have to make all these modifications to your furnace and your whole production process to achieve the same product yield or outcome of the production process. You don’t have to do that.
Doug Glenn: Does Kanthal help companies do an assessment of the cost-benefit analysis?
Art Moslow: Yes, we do. A lot of times, there are a lot of steps involved to convert from gas to electric. Even to present a client with an electric solution, we have to do a lot of background work like that to analyze their furnace process, to calculate the amount of power, in terms of kilowatts or watts, that is needed to energize their furnace and achieve their desired outcomes.
It’s not a simple action of plugging into an equation, hit an equal sign, and all of a sudden you have a number; there’s a lot that has to be done. And that’s what Kanthal does.
We run a lot of calculations, and then present that information to the client. That’s part of it: we want to show the return on your investment.
False Assumptions about Electrification (10:41)
Doug Glenn: Art, are there any fallacies or false assumptions that you guys tend to find you run into regularly that need to be addressed? If so, what are they and what do you say to them?

Art Moslow: Again, it’s going back to the challenge to change. The main challenge to overcome is proving how an electric heating system can achieve the same outcome as a gas-fired system, no matter what type of form of heat transfer. This includes radiant-type heating or even simulating a direct-fired burner. With the latter, you have all the convection, so it’s just the flame with the heat being transferred via air circulation; so, you can do the same process with electric heating.
Doug Glenn: I’ve heard some people have been concerned about the temperature range of electric versus gas-fired or the atmosphere in which the process is taking place and the sensitivity of electric elements versus gas-fired, and things of that sort. Can you address that?
Art Moslow: I would say temperature and atmosphere and heat-up rates — a lot of that contributes to the demands of the heating system.
For electric heating, you have very low temperature — a couple hundred degrees Fahrenheit up to probably a little over 350 degrees Fahrenheit. You can cover that entire temperature range with electric heating, whether it’s a metallic alloy that goes up to a certain temperature range, and then we have ceramic-type heaters like silicone carbide glow bars, molybdenum disilicide Kanthal Super. You cover the entire temperature range with electric heating. Then, you can use those materials in different modes of heat transfer.
You have different modes of heat transfer for gas; you can do the same thing for electricity when it comes to radiant-type heating (convective or conduction). A lot of times, it’s a combination of more than one of those types.
It’s up to Kanthal to assist the client and help them select the right alloy or the right material. Some materials are better suited than others in different atmospheres.
Art Moslow, Kanthal
When it comes to atmospheres, there are a lot of different atmospheres other than just air. There’s nitrogen, hydrogen, there’s carburizing furnaces. There are all different types of atmospheres that need to be controlled within a furnace. Electric heating elements can operate under all of those conditions.
It’s up to Kanthal to assist the client and help them select the right alloy or the right material. Some materials are better suited than others in different atmospheres. It’s just ensuring that you’re using the best fit for that atmosphere.
Doug Glenn: I assume that Kanthal’s elements can also go inside of tubes, if they need a protective tube of some sort.
Art Moslow: Oh, yes. In a lot of heat treat furnaces (if it’s a gas-fired system), the gas burner is firing into a tube and the tube is radiating into the chamber, and that’s what’s generating the heat.
We have a few different types of heating elements that you can use when replacing the burner with an electric heating element right inside the tube. It’s the same mode of heat transfer and provides a high-power output.
You’re not really modifying the furnace that much in terms of its process and its temperature profile. You’re just replacing the heat source with an electric heat source.
Doug Glenn: Right, a burner with a heating element.
Preparing to Electrify (16:28)
Tell me, Art, what question does a manufacturer, who currently has a gas-fired furnace, need to ask to start preparing if they want to electrify?
Art Moslow: Typically, when we’re working with a client or manufacturer and helping them on this journey (converting from gas to electric), we put the process into four really basic steps.
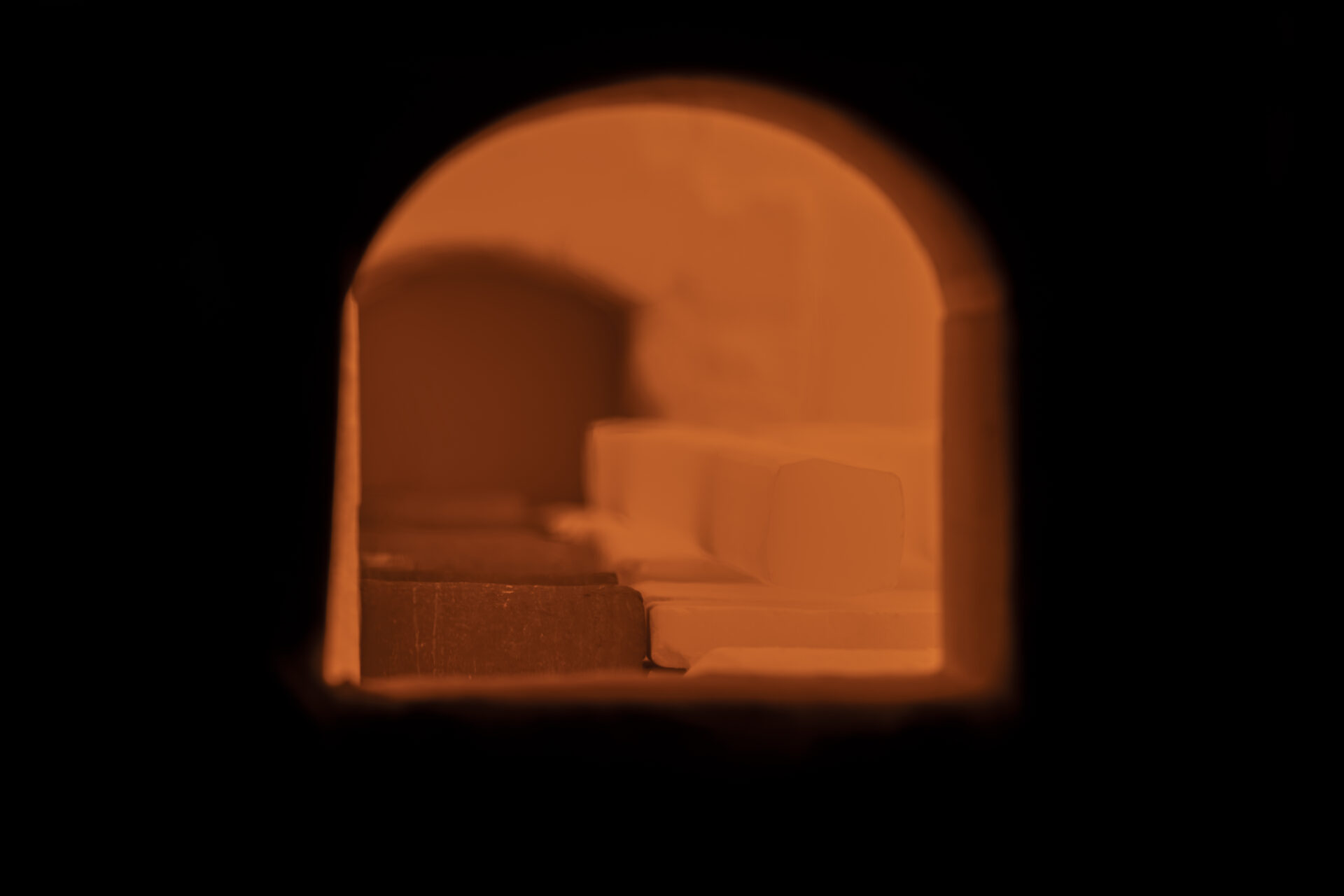
Source: Kanthal
The first two are, kind of, the most important to prove a system solution. It involves calculating the power required, converting the BTUs to kilowatts.
As I said earlier, we’ll collaborate with our clients to do that, and it’s much more than just “crunching the numbers.” You really want to analyze the furnace process. You’re getting a full view of the “as is” state. What are they currently doing? What are they processing? What temperatures are they going to?
Perhaps we even do some analysis of the furnace. For example, you’re taking the temperature of the casing. Does the client want to make any process improvements? Is it time to replace some of the insulation? Can we make some recommendations to improve the efficiency of the furnace? We’ll also do a lot of thermal dynamic calculations and then provide that information to the client. This is, kind of, the expectation to achieve your throughput in the furnace or the specific heat-up. Whether it’s a batch furnace where you’re loading a product, heating it up, cooling it down, and then pulling it out, or if it’s continuous.
So, there are a lot of questions that we ask and a lot of analysis that we do. Then, we communicate that back to the client. It’s all presented to them — this is what we would propose.
After that, the next step is designing the heating system. I mentioned earlier that Kanthal has a very wide range, when it comes to temperatures and materials. There are times when an overlap of multiple solutions might work in a furnace, and it’s up to Kanthal to recommend solutions for clients. We’ll lay out: this is the ideal solution, this is why, and this is the payback.
We offer (that is, some clients ask for) CFD modeling (computational fluid dynamics). So, you’re mapping out the solution using a computer. It helps to reinforce the solution to lay it out for a client so they can see it before any kind of decision is made. They might have some feedback as to — oh, we see that this is possible; is there anything more we can do in the furnace?
A lot of times we see that a furnace is originally built for a certain process and a certain temperature, and, over the years, it changes. You want to get more and more use out of your furnace, so maybe you’re pushing the temperature higher than it was designed to, or you’re trying to increase your throughput. You’re putting more product through and pulling more out. So, maybe there’s a chance to do that even more, when converting to electric.
Instead of buying new furnaces or more furnaces, maybe you can get more out of your existing equipment. That’s where CFD modeling helps, as well. It helps us to really present everything to the client.
The last two steps are really specific to a furnace. It’s about removing the existing gas system, removing the gas train, which can improve the safety of the facility.
Typically, gas burners are very loud. We’ve had clients comment, “We don’t even notice that the furnace is on, if we don’t look at the temperature controller,” because there is no more noise when you’re running electricity.
All of that is specific to a client’s furnace.
The last step is installing the electric heating system.
Timeframe for Electrification (21:19)
Doug Glenn: This is a loaded question, and I’m sure it varies widely, but can you give an example of the timeframe that it would take to convert any type of furnace? Maybe one Kanthal have done in the past? There are a lot of batch furnaces that our listeners would use; there’s also a lot of continuous. And, of course, the size of each of those is going to make a huge difference.
Can you give the listeners a sense of how long it is going to take for this process to convert?
Art Moslow: Typically, the first couple steps take a couple of weeks. There is a lot of communication back and forth between the client and Kanthal. We’re gathering information, so we might have to visit a couple of times, and also coordinate with their utility’s supplier. Does the facility have the electric power available? How can they source it to get it to the facility?
Then, there are other components that are needed to electrify a furnace, like the electrical control system.
We have partners (other suppliers) that we know and work with who are very familiar with supplying controls to the appropriate type of heating system.
Different alloys and different materials behave differently when it comes to electric heating. Some controls require current-limit settings, some transformers, some don’t, so there are suppliers out there that are familiar with the requirements.
Art Moslow, Kanthal
Doug Glenn: And you work with them.
Art Moslow: We do. Typically, we work with them, we provide the client with recommendations, saying, “This is what you need.”
Kanthal doesn’t supply control systems. We do, for a couple of our products, because they’re unique, but we tend to work with other partners to do that.
The entire process could take a couple of months. Procuring and manufacturing all of the components is the longest part of the process.
Doug Glenn: As I said, it’s a loaded question because I’m quite sure it’s very dependent upon the process that the client is running, how long it’s going to take to validate the conversion, and whether or not your CFD modeling and things of that sort to really convince people that this does work.
Art Moslow: What is the size of the equipment, too? It’s not just the furnace.
And we want to fit it into the client’s timeline. When is their shutdown? To do a conversion, you can’t just do that overnight. The furnace must be shut down for a given amount of time to do a conversion.
When Not to Electrify (24:26)
Doug Glenn: This is a question where you have to be really honest: Are there times when people should not electrify? Are there instances out there where it just doesn’t make sense?
Art Moslow: There are times where a client might have a furnace that’s quite old, and the cost to convert doesn’t make sense. They really need to rebuild the entire furnace because the insulation is old and losing its integrity, and there’s too much heat loss from that. And the size of the system to try and fit an electric system into a given space just might not work.
We haven’t really seen the process like that other than when the client has a used furnace that they’ve been running. It doesn’t quite match the process they’re trying to run, but it’s a furnace that they had, so they just keep running it. It just makes sense and is more cost effective to replace the furnace with an electric furnace.
Doug Glenn: Are you finding that there are certain U.S. geographies where it’s much harder to get people to convert to electric simply because of the disparity between gas prices and electric prices, or does it almost always make sense to at least investigate it pretty much everywhere?
Art Moslow: You know, Doug, if you asked me that 5–10 years ago, I would’ve said yes, without hesitating. But I would not say the majority of our clients are in “this” geography or in “that” region of the U.S. It’s beyond the point of just looking at the cost of gas and electricity — it’s well beyond that now.
There are a lot of strong arguments about the CO2 emissions reduction, safety, and environmental aspects and benefits when it comes to sustainability that are really being driven at a corporate level now, especially in the U.S., which is a newer trend.
Doug Glenn: Yes, it is. As everybody knows, we tend to lag behind Europe in these things. I don’t know if that’s good or bad, but that is the case.
Maintenance of Electrical Equipment (27:19)
I want to back up a little bit on the equipment and ask you a question about maintenance. Because one of the advantages, I have heard, is that there is potentially a significant advantage with maintenance and upkeep of electrical equipment versus combustion equipment.
As you mentioned, combustion tends to be pretty loud; that’s because you’ve got blowers spinning at who knows how many RPMs. You’ve got air piping, you’ve got gas piping, you’ve got mixtures, and all that stuff.
Can you address any major maintenance issues with electrical systems?
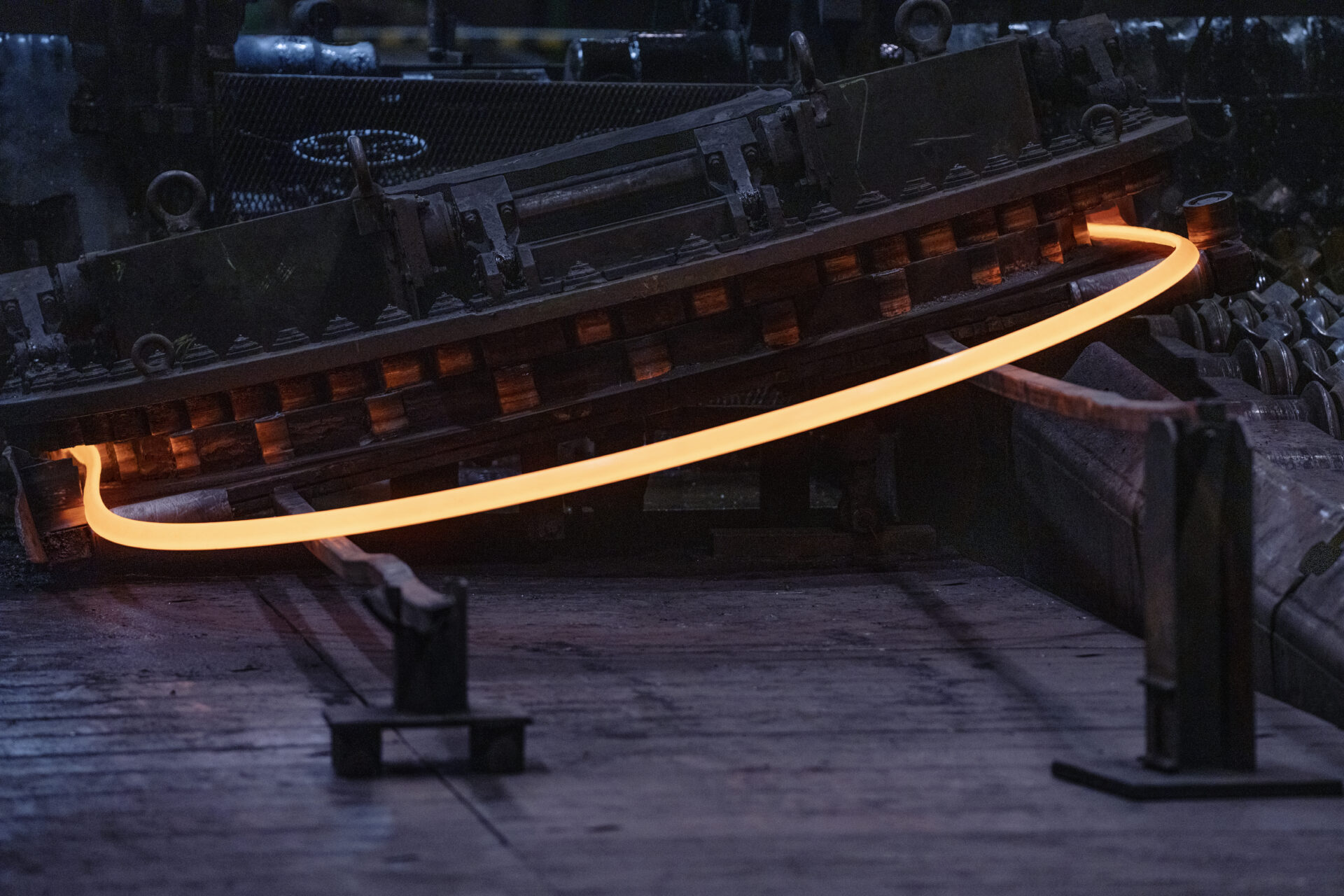
Source: Kanthal
Art Moslow: There are a lot of systems — like the example you brought up earlier, where you asked the question of if it is possible to put a heating element inside of a tube. For that type of solution, we have a proprietary alloy tube that Kanthal manufactures that goes to very high temperatures. We also sell an applicable heating element made out of the same material that’s designed for use inside the tube.
Typically, when you put in tubes, you’re isolating the atmosphere inside the furnace, and you put a heating element inside the tube. Inside the tube, it’s just air, so it’s very easy to replace the heating element when an issue like that comes up.
You do your safety “tag out/lock out” procedures; you secure power to the elements, and you disconnect them; you can pull them out, you can handle them when they’re hot, provided you’re following proper safety procedures; most, if not all, electric heating elements can be installed while the furnace is still hot; you don’t have to worry about thermal shock or overheating them; and they can be connected and run right away.
Most elements, too, you can mix old and new elements without an issue; there is no performance degradation with the older elements or the new element.
Doug Glenn: So, maintenance, generally speaking, seems to be a bit easier with electric.
Art Moslow: Yes. It’s easy to store a spare element; it’s easy to replace one. And, typically, we’re shooting for life that’s measured in years when it comes to electric heating systems. That’s our objective when designing a solution.
Sustainable Technologies (29:57)
Doug Glenn: Alright, coming down the homestretch here. There have been a lot of improvements in technologies over the last several decades to help with sustainability and things of that sort. Are there any newer technologies, materials, processes that you would like to mention that might be of interest to our in-house heat treat or thermal process people, when it comes to sustainability?
Art Moslow: When it comes to sustainability and ensuring that we’re meeting the demands of industry, in the advertisement, you had indicated that at Kanthal we do spend a lot of resources on R&D to continuously improve our materials to come up with new materials within a product — a grade perhaps, like new grades of moly disillicide Kanthal Super materials that meet the demands of the industry.
We’ve seen an increase in demand for hydrogen atmosphere furnaces and nitrogen. So, we’re constantly developing new materials to meet the demands of industry.

A newer product that we have, too, we call a Kanthal airflow heater. It’s a very high temperature air heater that’s on the market now that can be used in a lot of different industries.
There are a lot of newer applications that we’re looking into. We’ve seen clients wanting to duplicate or mimic the performance of a direct-fired gas burner. It’s just a flame-firing heat — it’s all convective heat — into a combustion chamber. We’ve had some applications for clients wanting to duplicate that using electric heating.
Doug Glenn: Do you know the temperature range on that?
Art Moslow: I can list it in degrees Centigrade: it goes up to about 1100/1200°C.
Doug Glenn: Any other new technologies or processes?
Art Moslow: No, that’s it. There are a lot of newer materials. It’s always really pushing the materials that we have on the market — so looking for higher temperatures, higher power outlets.
Final Thoughts on Electrification (32:49)
Doug Glenn: Last thing: Is there anything else for manufacturers who have their own in-house thermal processing or heat treating? Any other encouragements or thoughts you’d like to share with them, when it comes to sustainability in the conversion from gas to electric?
Art Moslow: Keep in mind that you can convert from gas to electric. And Kanthal can help you do that. We can assist you and collaborate with you to analyze your process and come up with recommendations.
Doug Glenn: This is a “tack on” question, here at the end: Is Kanthal involved, in any way, with reliability of the power grid? Are they doing anything to help? It’s outside the scope of Kanthal — I realize you are manufacturers — but the reliability of electricity is a critical thing for people to convert, and I’m just wondering if Kanthal is doing anything to help utilities make that supply of electricity more reliable.
Art Moslow: Kanthal is involved with providing heating systems to various industries that are making clean energy, like the solar industry and wind turbines.
There are companies looking at energy storage. In the past, that was really more of a theoretical-type idea as to how to come up with an ideal energy storage-type application, but there are increasingly more companies looking at, exploring, developing, and improving technologies that work.
Doug Glenn: Art, thank you very much, I appreciate it and appreciate your time.
Art Moslow: Thank you for having me, Doug.
About the Expert
Arthur (Art) Moslow is an engineering and communications professional, working as the electrification project manager at Kanthal Heating Systems for the past year. He has been with Kanthal for over 20 years serving in various sales and product engineering roles. He received his Bachelor of Engineering in Naval Architecture and Marine Engineering from State University of New York Maritime College.
Contact Art at arthur.moslow@kanthal.com or go to www.kanthal.com.