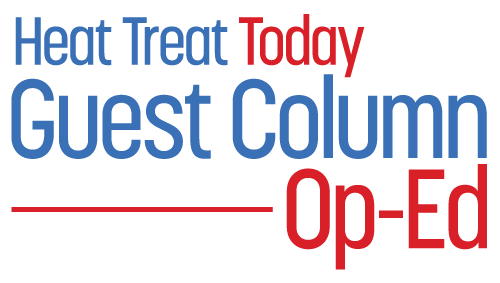
Hot isostatic press (HIP) processing is a manufacturing technology used to densify metal and ceramic parts to improve a material’s mechanical properties. It is based on applying high levels of pressure (up to 2,000 bar/200Mpa) and temperature (up to 3632°F (2000°C)) through an inert atmosphere in order to densify parts and components, mostly of metallic and ceramic material, and to give them improved mechanical properties.
HIP technology has become the decisive tool for aerospace parts and components to certify materials and parts with the strictest quality and safety controls. These developments require highly advanced, complex, and processed materials capable of withstanding the demanding work they will be subjected to.
There are strategic materials and components in the space sector that can only be manufactured by advanced manufacturing in a specific way. Rubén García, project manager of HIP at Hiperbaric, noted that “These developments need very advanced, complex, and processed materials that are capable of withstanding the demanding work they will be subjected to. Therefore, advanced processes are needed to ensure and certify that these materials can be part of a satellite or rocket.” In addition to elements that form part of satellites and rockets and their respective engines, turbomachines, burners, and more intended for space also see benefits from HIP processing.
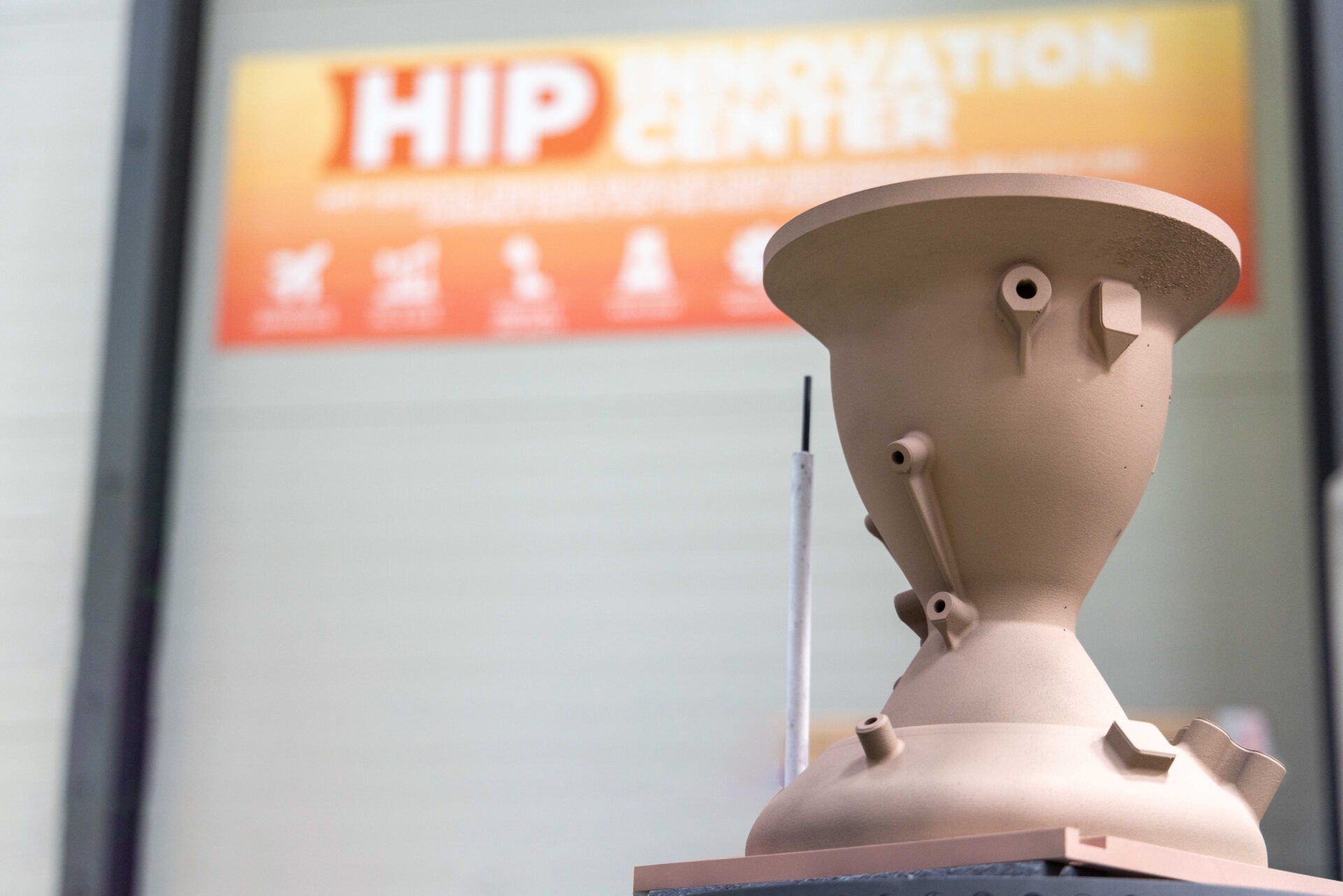
Source: Hiperbaric
An X-ray inspection of each part evaluates the suitability of the component and ensures that it will not fail during the combustion process. “If we find any pores in the part, they are repaired with HIP technology, which repairs and densifies the component,” explains García. The HIP technology supplier uses Fast Cooling technology to cool materials very quickly, especially in materials whose capabilities may be impaired if they are not cooled quickly.
Emphasizing how HIP is the key that takes components to space, García describes, “The more complex qualification components are required to go through a HIP process to ensure that the component will not fail. Materials engineering and the metallurgical process are closely tied to these innovations to ensure what some processes can’t do 100%. That is where HIP becomes our best ally.”
Hiperbaric has devoted a HIP press for its HIP Innovation Center in Spain for companies worldwide for the purpose of investigating and developing HIP products with a particular focus on the aeronautical sector. Here, companies will find the help and knowledge required to achieve success.
About the Expert:

HIP Project Manager
Hiperbaric
Rubén García Reizábal is an industrial engineer with a master’s degree in Material Components and Durability of Structures and has recently obtained his PhD. After his first stage in Hiperbaric, where he held the position of Quality Manager, he has been working as project manager of several R&D projects for more than 11 years. In this role, he leads all the actions of the Spanish-based company related to its hot isostatic pressing (HIP) business line, including R&D and business development efforts.
Contact Rubén at r.garcia@hiperbaric.com.