AMS2750F, a rewrite of the specification that covers pyrometric requirements for equipment used for the thermal processing of metallic materials, was released at the end of June. For this Technical Tuesday feature, Heat Treat Today asked a few experts in the aerospace industry to share their insights of this much anticipated revision that helps to better clarify issues with the previous revision. Specifically, Heat Treat Today wanted to know what they perceived to be the top 2-3 most important changes in revision F; what companies should do to prepare for these changes; and additional thoughts about the revision as it relates to aerospace heat treating.
Industry experts who contributed to this Original Content piece are Andrew Bassett, president, Aerospace Testing & Pyrometry, Inc., Jason Schulze, director of Technical Services; Special Process – Metallurgy, Conrad Kacsik Instrument Systems, Inc., Peter Sherwin, Global Business Development manager for Heat Treat, Eurotherm by Schneider Electric, Jim Oakes, president, Super Systems, Inc., and Doug Shuler, lead auditor, owner, Pyro Consulting LLC.
Andrew Bassett was on the subteam for AMS2750F as well as the previous revision AMS2750E and has been a member of AMEC and SAE Committee B since 2006. He shares some “inside baseball” background about this four year process, “The AMS2750F subteam utilized the Nadcap Pyrometry Reference Guide, the Nadcap Heat Treat Audit Advisories that pertained to Pyrometry, and the collective experience from the sub-team which dealt with the previous revision issues and problems. The AMS2750F sub-team had a broad range of backgrounds, with representatives from Boeing, Safran, Arconic, GeoCorp Inc, Nadcap-PRI, and Aerospace Testing & Pyrometry.”
What do you believe to be important changes in revision F?
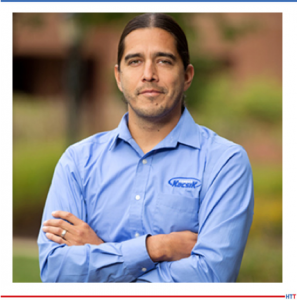
Jason Schulze comments on offsets saying, “Offsets have often been a confusing subject throughout the years. How they are applied, removed and documented has caused confusion and has been a source of Nadcap findings. With the changes to the offsets section of AMS2750 in the new revision, these issues will be greatly reduced. Offsets have now been split into two categories; correction offsets and modification offsets. It will be important for suppliers to understand and implement the new requirements as well as use the same verbiage as this will hopefully alleviate further confusion.”
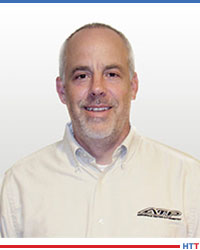
Andrew agrees this is an important change regarding the offsets and further clarifies, “A “Modification Offset” is when an instrument is purposely, either through electronic means or manual means, shifts the accuracy away from the nominal temperature. This is typically done to “center a temperature uniformity” that may be skewed in one direction or another. The modification offset, when used properly, will shift the temperature uniformity more towards the set point of the thermal processing equipment. A “Correction Offset” is used to bring the instrument back to the nominal temperature. As always, a well defined procedure will be required on how the “Correction Offset” and “Modification Offset” will be introduced into your system.”
“One of the biggest changes that caused a lot of controversy was the restricted re-use of expendable test thermocouples,” Andrew notes. “The AMS2750F subteam provided studies and data that showed that there was considerable drift of certain types of base metals thermocouples, especially when it came to Type “K” thermocouples. The previous revision of AMS-2750 already had restrictions on these types, but after providing data of the drift of these thermocouples, the team felt further restrictions were required for Expendable Base Metal SAT & TUS Sensors. Section 3.1.7.3 describes the limitations of these type thermocouples. Types “M”, “T”, “K” & “E” shall be limited to 3 months or five uses, whichever occurs first between 500F and 1200F (260C and 650C) and is limited to single use above 1200F (650C). Types “J” and “N” shall be limited to 3 months or ten uses, whichever occurs first between 500F and 1200F (260C and 650C) and is limited to single use above 1200F (650C).”
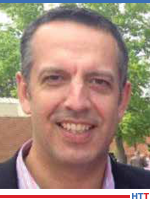
Peter Sherwin comments on instrumentation, “From an instrument perspective our no.1 focus is the instrument accuracy specification. This has not changed for Field Test or Control and Recording Instruments (now in Table 7), however the impact of the decimal place for digital recorders could cause some issues for less precise instrumentation. In 3.2.3.1 All control, recording and overtemp instruments shall be digital 2 years after release of AMS2750F – this was not a surprise, and today’s overall cost (paper, pens, storage etc.) of paper chart recorders cannot match their digital counterparts. Digital time synchronization (3.2.3.19) is also sensible to ensure you have an accurate time record across a number of Furnaces/Ovens and charts – we are used to this for other regulations (e.g. FDA 21 CFR Part 11) and offer a SNTP/Time Synchronization feature in our Recorders.”
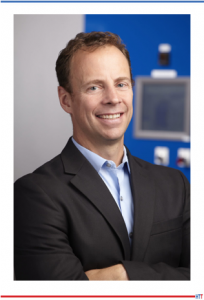
Jim Oakes shared his pleasure with section 3.2.3.12, “I was happy to see the document address integrated recording/controlling data. It states in section 3.2.3.12 when the control and recording system is integrated such that the digitally displayed control value and digitally recorded value are generated from the same measurement circuit and cannot be different, it is only necessary to document a single displayed/recorded value for the control reading. This is happening through direct communications, so what you see on the controller is what you are recording electronically. This saves a step and eliminates the need for additional documentation.”
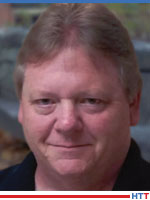
Doug Shuler cites the auditor advising piece, “The top of the list has to be the overall progress we made by incorporating auditor advisories and pyrometry reference guide FQS into the body of the specification so users don’t have to ask themselves “What did I miss.”
How should companies prepare for these changes?
Jason Schulze’s advice to companies focuses on training, “Companies should receive concise training regarding the revisions within AMS2750F, including administrative and technical. As with any training, continuous courses may be necessary to ensure comprehension. I recommend performing a characteristic accountability for each and every requirement stated within AMS2750F.”
Peter Sherwin encourages companies to ready instrumentation for the standards, “Recent feedback from the MTI indicated that 3rd party audits to the new standard would probably start next year. However, if you are in the market for a new instrument then it only makes sense to ensure this meets the requirements of the updated standard.”
Doug Shuler sees the benefit of analysis, “Users should prepare by performing an internal or perhaps an external gap analysis to establish where their pyrometry system is today, and what has to be changed going forward. Users don’t have to wait until AMS2750F and AC7102/8 Rev A are released and in effect before making changes. The key is that if a user has an audit before the revised Nadcap Checklist AC7102/8 Rev A becomes the law of the land, they will have to declare compliance to AMS2750E or AMS2750F in full and will be held to that revision’s requirements. Once AC7102/8 Rev A takes effect (best guess after January 1, 2021) all audits will be done to AMS2750F.”
Andrew Bassett recommends, “First and foremost, get a copy of AMS2750F and start the review process. Since the document was a complete re-write, there is no change summary or change bars to point the supplier in the direction of what has changed. Spend time creating a matrix of the previous requirements (AMS2750E) and comparing to the new requirements (AMS2750F). I would suggest breaking this matrix down into four main sections: Thermocouples, Calibrations, System Accuracy Testing, and Temperature Uniformity Surveys. This will allow suppliers to work on each section without getting overwhelmed by the entirety of the specification. Currently at the time of writing this, there is no formal implementation requirement for AMS2750F. Typically this will either be dictated by the suppliers’ customers, or in the case of Nadcap, they will issue a “Supplier Advisory” as to when their expectation for implementation will be.”
Final Thoughts
Planning for the future will serve companies well for the long term encourages Doug Shuler, “With a number of significant changes, nearing a complete rewrite, now is a good time to take a look at your internal procedures that may have become fragmented over the years and streamline them to the new revision. Auditing for Nadcap for over 10 years has shown me one thing for sure. Those companies that have a thermocouple procedure, a calibration procedure, a SAT procedure, an alternate SAT procedure, a TUS procedure, and maybe even multiple TUS procedures for different kinds of furnaces (Air, Vacuum, Atmosphere, etc.) usually have a more difficult time with audits because the SAT procedure also addresses thermocouples, but doesn’t address correction factors because that’s in the instrument calibration procedure… See where this is going? Consider writing one pyrometry procedure with sections in it just like the specification. Then, the SAT section can refer to the thermocouple section for test thermocouples and to the instrument section for test instruments, etc. It’s like re-writing AMS2750, but customized for your facility, your equipment, and your practices. In the end, remember that the pyrometry portion of your Nadcap audit follows my P.I.E. acronym. Procedures that Include all requirements and Evidence to show compliance.”
Paying close attention to the right data solution will alleviate potential headaches when dealing with both the new AMS2750F revision and the CQI9 (V.4 update) says Peter Sherwin, “Many commercial heat treaters will also have to cope with the update to CQI9 Version 4 at the same time! According to the MTI, your ‘end’ customers may request you perform your self-audit to the new standard from this point forward. There is a bit more time allocated to move to digital (3 years), but my advice would be to take advantage of digital solutions sooner rather than later. The right data solution should save you money over time compared to the paper alternative.”
Finally, amidst all the new changes AMS 2750F has offered, Jim Oakes assures, “…the pyrometric requirements that most of us are used to will still be very familiar as this document becomes the new standard.”
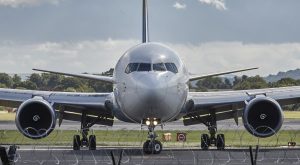