Between science and business, the evolution of heat treatment is taking large strides. A global heat treat solutions manufacturer and a Polish laboratory hardening plant are developing modern solutions to metal treatment needs.
For the past decade, SECO/WARWICK, the global manufacturer and parent of North America SECO/VACUUM Technologies of metal heat treatment equipment and technologies, and HART-TECH, a hardening plant with scholarly shareholders — professors, doctors of science, process engineers — have been working together to engage in the evolving science of modern metal heat treatment solutions.
Together with professor Piotr Kula’s team from the faculty of Mechanical Engineering at the Łódź University of Technology, the company implemented projects and research, and collaborated on the technical capabilities of the equipment in terms of the latest research and innovations in the discipline. As this work progressed, the cooperation started to involve product development through equipment testing in practical business applications.
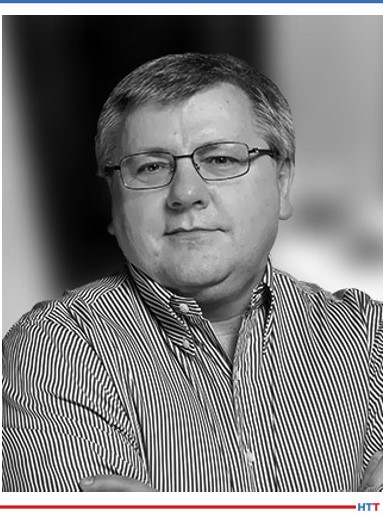
Management Board CEO and a Technological Department Head Director
HART-TECH Sp. z o. o.
In 2009, the initiative of three researchers from the Institute of Materials Science and Engineering of the Łódź University of Technology — professor Piotr Kula, professor Antoni Rzepkowski, and Robert Pietrasik, Sc.D. Eng. — brought to life the HART-TECH hardening plant, which currently holds 11 specialized devices for vacuum metal treatment, equipment provided by the global heat treat manufacturer.
The hardening plant specializes in: hardening, carburizing, nitriding, sulfonitriding, steel tempering processes, and more. They apply the latest technologies to modify, change, and improve products. In turn, SECO/WARWICK modifies their equipment designs to meet the exact needs of the customer.
“Our experience and process facilities enable us to perform very demanding and difficult processes,” explained Robert Pietrasik, Sc.D. Eng, president of the board of HART-TECH. “We are renowned to be experts in the impossible since we have vast scientific knowledge and expertise as well as reliable technological back-up from SECO/WARWICK. This cooperation enables us to specialize in highly demanding and difficult jobs requiring the best quality.”
The companies seek new implementations with technologies and processes/modifications that will make the heat treatment process more efficient, allow optimizations, or even defining new technologies. SECO/WARWICK equipment is for trials, experiments and tests. The devices allow for the control and monitoring of a given process, and their design provides for additional safety margins that make it impossible to exceed temperature, power and speed limits. The furnaces are enable many processes with the use of one device. Commercial hardening plants especially value the versatility when serving many different customers from various industries and sectors.
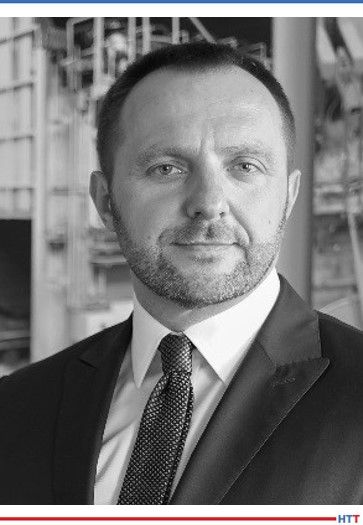
CEO
SECO/WARWICK
Source: secowarwick.com
“On the one hand,” said Sławomir Woźniak, CEO of SECO/WARWICK Group, “HART-TECH is a particular partner with whom we have very close cooperation in terms of the technologies and processes. On the other hand, this customer is something of an extreme. They quickly switch from what the device was intended for to what more can be done with it.”
“Our [partner’s] curiosity of the world motivates us to develop new innovations,” added Maciej Korecki, vice president of the Vacuum Business Segment at SECO/WARWICK Group. “We attentively listen to the feedback from our customers. This enables us to create tailor made solutions that always respond to the needs 100%. With HART-TECH, we share the passion and a huge, constant drive for excellence.”
After the hardening plant’s growth in their heat treating capacities over several years, they found themselves, like others confronting hardening deformations. Therefore, HART-TECH was in need of a device enabling gas quenching to minimize the problem. The company selected a single-chamber Vector® furnace for high-pressure gas quenching (10 bar) with nitrogen cooling.
The dynamic expansion of HART-TECH motivated them to place an order for another Vector® furnace for high-pressure gas quenching (15 bar).
The last device ordered summarizes the 10-year cooperation between the two companies: another CaseMaster Evolution® (CMe) unit — a two-chamber, third-generation furnace for batch processing with oil cooling. It offers a significant advantage in shortening the production process and improving the quality targets.
“Certainly, the expansion of our hardening plant has not been a conventional one,” says Pietrasik. “We need to remember that the developing market needs were a significant factor affecting the purchase of new devices by HART-TECH[…] We started with one customer and furnaces rented from Łódź University of Technology on an hourly basis. Now, all our vacuum furnaces come from SECO/WARWICK[..] More than 1300 customers and a technology partner are probably the best recommendation for us and for this partnership.”
“We are not interested in the intended purpose of the device,” Sylwester Pawęta, Sc.D., Eng, operations director and shareholder of HART-TECH, “but in what it can really do, what are its technological limits.”
“Continuous feedback from trials of equipment operated under the maximum load, used in an intensive way, shows us what we need to reinforce and improve to maintain the highest treatment parameters for the entire lifetime of the device, and also how we can upgrade them to work even better. Sometimes, this is a real trial by fire, or a test bench,” summarised M. Korecki.
Images sourced from SECOWARWICK.com.