Welcome to another episode of Heat Treat Radio, a periodic podcast where Heat Treat Radio host, Doug Glenn, discusses cutting-edge topics with industry-leading personalities. Below, you can either listen to the podcast by clicking on the audio play button, or you can read an edited version of the transcript. To see a complete list of other Heat Treat Radio episodes, click here.
Audio: George Smith and Dan Graham
In this conversation, Heat Treat Radio host, Doug Glenn, speaks with George Smith and Dan Graham from SBS Corporation, based in Sarasota, Florida. SBS designs and engineers high-performing heat treatment solutions, including heat exchangers, filtration systems, and monitors. This episode will be especially interesting to companies who are wanting to dip their big toe into the Industry 4.0 or Internet-of-Things swimming pool but have been afraid to do so because of their cost or lack of organizational expertise. This episode introduces a relatively new product on the market that is specifically designed for entry-level applications.
Click the play button below to listen.
Transcript: George Smith and Dan Graham
The following transcript has been edited for your reading enjoyment.
“If your maintenance had the ability to monitor everything in your shop — 24 hours a day, 7 days a week, didn’t eat, sleep, or take a break — how much would that guy be worth to you? Probably quite a bit! Now, if you could also simultaneously record every data point from each sensor in your shop by the minute and then call, text, or email you date, time, and set-point readings, I think he’d be worth a lot more.” ~ George Smith of SBS Corporation
Thanks for joining us. I’m your Heat Treat Radio host, Doug Glenn, also the publisher of Heat Treat Today, which you can find on the web at www.heattreattoday.com. The above was George Smith. George is one of two people we will talk to on this episode from SBS Corporation about their new entry-level and fully expandable monitoring system.
We’ll get back to George and our other SBS guest, Dan Graham, in just a few moments. But first, let me remind you that Heat Treat Today is ready to help you do heat treating better. Our editorial content is targeted at manufacturers with in-house heat treat shops, especially in the aerospace, automotive, medical and energy sectors as well as general manufacturing. Heat Treat Today believes that people are happier and make better decisions when they are well informed. And it is our passion to help you be well informed. We also like to inform you in ways that are current, like podcasts and targeted e-newsletters. You can subscribe to any of these services on our website. Take some time and check out the information we are providing and feel free to subscribe to any of the services we are offering. Go to www.heattreattoday.com/subscribe.
Doug Glenn (DG): Now let’s get back to our guest. Here is George Smith again, followed by Dan Graham, introducing themselves. Both of these guys were members of Heat Treat Today‘s inaugural class of 40 Under 40. First, here is George Smith.

George Smith (GS): I am George Smith, and I am the general manager at SBS Corporation. I have been with the company for 6 years, and it is owned by my family.
Dan Graham (DGr): My name is Daniel Graham, and I have been with SBS Corporation since 2015, and I am the director of technology. I joined SBS as an intern at the tail end of my college career at Rollins College where I studied international business.
DG: Here now is George Smith expanding on his earlier description of the product SBS calls Watchdogg.
GS: [recording] “If you could also simultaneously record every data point from each sensor in your shop by the minute and then call, text, or email you date, time, and set-point readings, I think you’d be worth a lot more.” With Watchdogg, that’s exactly what you’re doing. The Watchdogg’s monitoring system monitors, records, and alerts the appropriate employee when a problem is going to happen before it actually becomes a problem. This can really apply to anything, whether that’s humidity in quench oil, low flow going to a heat exchanger or an over-temperature situation. Any place that you have a 4-20 mA signal available or a place to put a transmitter, you can monitor in real-time and predict what is going to go wrong.

Just a quick example: In the middle of the winter in the Midwest, you’ve got a cooling fan up on your roof. Nobody is going to go check on that fan, but if it’s vibrating too much or pulling too many amps, that can be a sign that the bearing is going bad, so that fan is going to go soon. Watchdogg would text, call, or email you before that breakdown occurs based on those two things. So, if there is anything in your shop that can break down and cause a complete shutdown in production, the Watchdogg is perfect for you.
From the Beginning: SBS Corporation
DG: I have not typically associated SBS Corporation with this type of equipment, so if you don’t mind, give us a brief history of SBS, and what I think most people would typically associate you with, and then tell us about how you transitioned into something like Watchdogg.
DGr: SBS typically provides heating, cooling, filtering, monitoring, and safety equipment for the heat treat industry and we have been since 1974. Our flagship product is the Quench Air which is a quench oil cooler. It can be seen in nearly every major heat treat [shop] in the U.S., and we regularly sell our equipment in 38 countries worldwide. We started in Rochester, Michigan, and recently moved our manufacturing facility to Sarasota, Florida.
So, why text? We thought this was where the world was heading. Trying to find useful data to protect potential problems. Right now we have a product called the Aqua-Sense. This system detects humidity in oil and alerts via strobe and light when humidity is at unsafe levels in quench oil, so it is a local alarm. So, we kind of dipped our toes into technology, but as we looked at that product, we thought, “Wouldn’t it be cool if you could get a text instead? Why do you need to be in the same room as the Aqua-Sense to get the alert?” In our research, we could not find any supplementing systems that could simply alert by text that was industrial, inexpensive, and reliable, so we just developed our own system.
DG: How long has the Aqua-Sense product been on the market?
DGr: Maybe 7 years.
DG: So basically, the Aqua-Sense was kind of the springboard that at least provided the impetus and the idea to go from an Aqua-Sense, where you’re basically monitoring one or just a couple of specific items, to be able to monitor a lot more and be able to send out text, or I suppose, you can communicate in whatever fashion you want, whether it be text, emails, or whatever, correct?
DGr: Correct. All of that is customizable. You can say – this person gets a text, this person gets a text and an email, and maybe the maintenance manager would get a text, an email, and a phone call.
DG: George, you mentioned this is a family business. Tell us a little bit more about you, and especially since both of you guys were in the inaugural class of Heat Treat Today’s 40 Under 40, it would be interesting to know how you got involved with the industry.
GS: I grew up building our product so I’d come in and spend my summers putting together heat exchangers, and became real familiar with the industry at a really young age, so it was kind of just a natural mesh when my dad called me one day and said, “Hey, will you come in and work for the family business?” I was actually working as a wetlands biologist at the time, and I was in a swamp, pretty close to an alligator when he called, and I thought, “You know what? Sure!”
DG: How about you, Dan? What’s your quick history?
DGr: George and I actually went to the same college and that’s how I got to know him. I finished a couple of years after he did, and in order to finish my degree, I needed to complete an internship. I was having trouble finding internships that I was interested in, and so I gave him a call and he had an opening for me. So I started working ay SBS, finished my degree, and haven’t left.
In-House Heat Treat Shops and Watchdogg
DG: So let’s try to dig in a little deeper. I know you guys have mentioned how companies, to a certain extent, might use Watchdogg. Most of the people who are reading this are going to be manufacturers who have their own in-house heat treat. So, they’ve got dedicated furnaces and things of that sort. How might they best use this? What is typical?
GS: This is a way they can bring their old pusher furnace, vacuum furnace, or whatever they’re using, and bring them right up into the 21st century. This is a really easy system to install on any existing equipment, and then you can monitor everything from your cellphone—like temperatures, vibrations, methane levels, I mean really anything that you can send a 4-20 mA signal with, and there are thousands of applications for that. If something is starting to go wrong anywhere on that furnace, you’re going to get a text message, and it’s going to tell you exactly where something is going wrong.
We have a customer in Tennessee that has rotary furnaces and if those rotary furnaces stop spinning, they basically “banana” and that is a $120,000 shop breakdown. If you can’t get a guy in there with a hand crank right away to get that furnace turning, [then] to save a power outage or for whatever reason a belt breaks, we can send a message out to all those guys that need to grab those hand cranks and get over there. You’re going to avert a very expensive breakdown.
DG: Because people may not be thinking along these lines, let’s give people a sense of what the different types of things that you can monitor. George, you’ve already mentioned some. You’re talking obviously quench oil humidity as one and about flow of liquids, etc. Give us some examples of the more common ones.
GS: Temperature, pressure, methanol levels, proximity sensors, level sensors—there are kind of endless possibilities for it. What we’re doing right now at our shop is using one to weigh our bins so that we know when we’re getting low on certain long-lead items. When we get down to 45 pounds of ¼“-20 bolt, we know to order that, and we get a text message that reminds us to.
DG: That is very interesting and a cool way to do that. So it’s almost inventory control as opposed to process control.
GS: Right!
DG: So how many inputs can Watchdogg take? How many things can you monitor with one unit, or are these units serial? Can you connect them?
GS: You can connect them, but each actual bay station has twelve inputs available. For example, on our filters, we do pressure, temperature, humidity, and then you can get basically a scheduling of when you’re going to need to change all your quench oil filters in your shop. We can send a warning saying these are the ones that are coming up next.
Entry-Level Connectivity to the Internet of Things
DG: There are other companies that are coming out with stuff like this, right? Remote monitoring type of stuff, and we won’t mention names here because we’re not talking about them. But I’m sure a lot of our readers would know who those companies are. How does the Watchdogg differ from those products?
GS: The Watchdogg is industrial, but it is also a low-cost monitoring system. We’re going for people who are just getting into the industrial internet of things. We found in our research that typical systems of our competitors were much more expensive, or the home monitoring systems that would be lower cost couldn’t handle the transmitters that we would require in these facilities.
DG: It is safe to say it’s really a nice entry-level product for someone who might want to get started in this area?
GS: It’s one that you can grow with. The more that you add, you can work towards having your entire shop connected. You can start out with 12 different points; we call them failure points, which are basically those points in your shop where if something goes wrong there, it’s going to shut down production. The question is, what are the most important things that can go wrong, and then what transmitters can we use to predict a problem there? From there you can expand out to doing your filter maintenance or dissolve solids in quench oil.
DG: So basically anything you can measure that has a sensor that is going to put out a 4-20 mA signal.
GS: Yes, it’s going to capture that signal if it’s out of the normal range and it’s going to send you a message. But it’s also going to data log all of that, which brings us into Nadcap. You don’t have to have the guy with a clipboard. There is an unlimited amount of data that it can store and it’s also going to grab it when you want it, whether you want it grabbed once every minute or once every hour. It’s all adjustable. It also gives you a very friendly to read graph.
You can also cross-reference. Let’s say there is a correlation between the humidity in your oil and the temperature of your oil. You go onto the site, you click your temperature, you click your humidity, you pick your date range and it graphs them right together for you. So you can go back 2 years and ask, What temperature was my oil at 1:00 in the afternoon on December 24, 2017? You can go right to that day and figure out what each transmitter was reading.
Storage, Users, and Support
DG: So you said that it’s unlimited storage of data?
GS: Yes, it is unlimited storage.
DG: Now that tells me that it is cloud-based.
GS: It is cloud-based. It is stored on a local server in a secure facility which is protected by an SSL, multiple firewalls, and it is off-site from SBS.
DG: How about the number of users that can be on this?
DGr: Also unlimited. 15 or 1500. The idea is that it’s a safety device. You ought to be able to reach out to as many people as possible if something bad is going to happen.
GS: Let’s say, for example, that you’re reading all of a sudden that you’ve got a bunch of water in the bottom of your quench tank. Well, why don’t you let everybody in that building know to get out of there?
DG: Yes, right. I assume that you can customize. In other words, you’re not going to be sending one message to everybody all the time.
GS: No, you set up each transmitter individually. You put in a list that can call in sequential order or it can do a blast call where it just calls the entire list at the same time or texts and emails at the same time. When you do the sequential delivery, someone can actually acknowledge it as “I’m going to fix that problem,” and it will stop calling the rest of the list. And it also records who said, “I’m going to fix that problem”, who acknowledged that alarm.
DG: You guys are selling this domestically, North America, internationally? What’s the market area?
GS: We’re selling the cellular data-based one just in the USA. The Ethernet-based we’re selling internationally.
DG: What’s the difference between those two?
GS: The cellular has a cellular card in it that works like your cellphone, so you don’t need an internet connection. If you don’t want to run internet out in your heat treat, you can use a cellular-based one, which is dollars a month for the cellular subscription. The Ethernet has to have an Ethernet cable run to it.
DG: And you’re able to support this, I assume, remotely?
DGr: Correct. We have our site, which grabs all these points. You see your heat treat, you see all your sensors, you see where you’re at and a very easy to use website. That’s where you go to set up all your transmitters. So basically you connect power and the 4-20 mA signal to the Watchdogg box, and then you go online and you say, for example, this is going to be humidity, so it will be 0 – 100%. You put in 0 – 100%, 4-20 mA signal, and you want this to alarm when it hits 50% relative humidity—that’s halfway to having liquid water in your oil. Then you hit “Apply” and that sensor is up and running. These things take a matter of minutes to set up.
Let’s talk about difficulty of use. This is such an easy-to-use system. I think people tend to be intimidated by the Internet of Things or having web-based monitoring. It can be a scary word to a lot of people. This is a really simple system. My 70-year-old father went ahead and set his own up, and he is not a “techy” by any means. It takes minutes to set up. It arrives basically as plug in and play. You plug it into the wall, you plug your sensors in, and then we walk you through set-up online. With the customer’s permission, we can access their pages and walk them through setting up transmitters. The website itself really walks you through that on its own. It is very intuitive. Each transmitter takes about 3 minutes to set up, so if you sat down for a half hour, you could have your Watchdogg up and running.
Where Watchdogg Is Headed
DG: What are you planning for the future? What’s in the offing here?
DGr: We’ve talked about keeping the data storage on site, so having a dedicated server in the customer’s facility. Some people just don’t want that information to leave, no matter what. That’s something we see in the future that we’re working on currently. Something else that we have been working on is really meshing this Watchdogg with a customer’s current control panel. This is something that we see pretty soon in development. Basically, we would create like a middle man almost that would split the 4-20 mA signal so that you could use the Watchdogg and your control panel at the same time, using your existing 4-20 mA signals that are coming back to your main control panel on your furnace.
GS: We’re also working to improve our products, integrating Watchdogg into all of the equipment that we’ve already built—our Quench Air heat exchangers, filters, sand separators, scale removal systems.
We hate just having a light on the wall. We were at a heat treat a couple of years ago and they had one of our filter systems and somebody had put a rag over the alarm horn on it because it was annoying. Nobody knows when that filter is full because they can’t hear it go off. So instead, let’s text the maintenance manager and give him a heads up when he’s got 2 days before he needs to change out that filter bag and then we’ll send him another note when he needs to change it. That way he can schedule it ahead of time.
This is all about avoiding breakdowns for our customers. The most costly thing that can happen is having a breakdown. That was our whole focus in designing this—How can we stop breakdowns from occurring?
DG: Are you enjoying the development of it, and are you happy with how it’s rolled out so far?
GS: We’re having a lot of fun with it. We’re constantly wondering what else we can do with it as it has so many applications—in our own shop, much less customers calling saying, “You know, I’ve got this in place and it’s got two more slots open on it, can I do this . . . ?” Then we get to figure out how do they do that, and then in 99% of the cases, our answer is, “Yes, you can do that!”
We had a customer that wanted to monitor his methanol. He called us and said, “Can I do that? I’ve got a methanol transmitter.” We said, “Absolutely!” So he plugged it in and now he’s monitoring his methanol.
DG: Do you tend to find people that will buy it, plug in a couple of things, and then find other things to plug into it because they like it so much?
GS: Yes, exactly. Anything you can think of. Like I was saying with our 4-20 mA scales that we’re using, that wasn’t the intended, original use for this, but we’re not running out of parts that we need!
DG: That’s a relatively innovative approach to it, I think—even inventory control! That’s pretty cool!
So if you’re in a company that is interested in moving into the 21st century and are looking for a fully expandable monitoring system to introduce you to the internet of things, this Watchdogg system from SBS Corporation might be just the ticket. For more information, you should go to www.sbscorporation.com or contact me directly at doug@heattreattoday.com and I’ll introduce you to George Smith or Dan Graham.
You can find more Heat Treat Radio episodes by googling Heat Treat Radio. Believe it or not, we’ll be the first nonpaid thing that pops up. You can also subscribe to Heat Treat Radio on iTunes or SoundCloud. Don’t forget to visit our website frequently. We post one new piece of heat treat information every weekday. You can subscribe to our daily e-newsletter or you can subscribe to our growing number of industry-specific heat treat e-newsletters like our Leaders in Aerospace heat treat monthly e-newsletter, which will debut soon, if not already. We’ll also be introducing a similar version for our automotive industry heat treaters as well as our medical and energy heat treat readers. Watch for them in the near future. Also, since we know that you can’t solve all of your own heat treat problems, feel free to reference our list of heat treat consultants on our website or by googling heat treat consultants. We should be one of the top 2 or 3 results that pop up. Or you can simply type www.heattreattoday.com/consultant into your browser.
This and every other episode of Heat Treat Radio is the sole property of Heat Treat Today and cannot be reproduced without specific written permission from Heat Treat Today.
This episode was produced by the recently engaged Jonathan Lloyd of Butler, Pennsylvania. Congratulations, Jonathan! I’m your host, Doug Glenn. Thanks for listening.
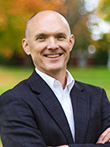
To find other Heat Treat Radio episodes, go to www.heattreattoday.com/radio and look in the list of Heat Treat Radio episodes listed.