This is the first in a 4-part series by Dr. Steve Offley (“Dr. O”), Product Marketing Manager at PhoenixTM, on the technical challenges of monitoring low-pressure carburizing (LPC) furnaces. This introductory article explains the LPC process and general monitoring needs and challenges.
Carburizing Process
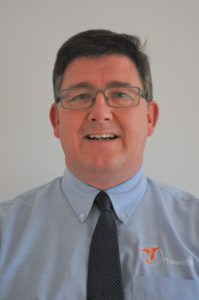
Carburizing has rapidly become one of the most critical heat treatment processes employed in the manufacture of automotive components. Also referred to as case hardening, it provides necessary surface resistance to wear while maintaining toughness and core strength essential for hardworking automotive parts.
The carburizing heat treatment process is commonly applied to low carbon steel parts after machining, as well as high alloy steel bearings, gears, and other components. Being critical to product performance, monitoring and controlling the product temperature in the heat treatment process is essential.
The carburizing process is achieved by heat treating the product in a carbon-rich environment, typically at a temperature of 900 – 1050 °C / 1652 – 1922 °F. The temperature and process time significantly influences the depth of carbon diffusion and associated surface characteristics. It is critical to the process that, following diffusion, a rapid quenching of the product is performed in which the temperature is rapidly decreased. This generates the microstructure giving the enhanced surface hardness while maintaining a soft and tough product core.
Increasing in popularity in the carburizing market is the use of batch or semi-continuous batch low-pressure carburizing furnaces. New furnace technology employs the dissociation of acetylene (or propane) to produce carbon in an oxygen-free low-pressure vacuum environment, which diffuses to a controlled depth in the steel surface. Following the diffusion, the product is transferred to a high-pressure gas quench chamber where it is rapidly gas cooled using typical N2 or Helium up to 20 bar.
An alternative to gas quenching is the use of an oil quench, used commonly in continuous carburizing furnaces where the products are plunged into an oil bath.
Fig 1: Schematics of the LPC Carburizing process showing the Temperature and Pressure steps
Temperature Monitoring Challenges in Low-Pressure Carburizing
As already stated, the success of the carburizing process is governed by careful control of both the process temperature and duration in the heating and quench stages. Obviously, when considering temperature, we are interested in the product temperature, not the furnace. Measuring product temperature through a carburizing process, although possible using trailing thermocouples, as performed historically, is neither easy nor safe, and it disrupts production for lengthy periods.
PhoenixTM provides a superior solution with the use of a “thru-process” temperature monitoring system. As the name suggests, the PhoenixTM temperature profiling system is designed to travel through the thermal process, measuring the product and or furnace environment from start to finish. The system can be incorporated into a standard production run so does not compromise productivity. A high accuracy, multi-channel data logger records temperature from thermocouple inputs, located at points of interest on, in, or around the product being thermally treated. To protect the data logger as it travels through the hostile furnace, a thermal barrier is employed to keep the logger at a safe working temperature to prevent damage and ensure accuracy of measurement. The barrier also obviously needs to protect during the quench, whether that be against high pressure or oil ingress if the quench can’t be avoided.
Employing the PhoenixTM system a complete thermal record of the product throughout the entire process can be collected. A popular enhancement to the system is the use of 2-way RF telemetry, providing real-time process monitoring directly from the furnace, useful for either profiling or performing a live Temperature Uniformity Survey (TUS). The product temperature can be viewed live and downloaded at any point in the furnace. Raw temperature data collected from the process can be converted into useful information using one of the custom-designed PhoenixTM Thermal View Software packages available. The thermal graph can be reviewed and analyzed to give a traceable, certified record of the process performance. Such information is critical to satisfying CQI-9, AMS2750, and other regulatory demands. Fully TUS-compliant reports can be produced in moments from the simple and intuitive software, making accurate TUS a simple and quick task. Information can be used to not only prove product quality but provide the means to confidently change process characteristics to improve productivity and process efficiency (Optimize Diffusion, Soak and Quench).