“High-pressure gas quenching (HPGQ) attempts to reduce temperature nonuniformities by reducing the cooling rate; however, this is generally not sufficient to eliminate shape change. Shape change can be predicted by heat treatment simulation software, but it is difficult to reproduce the exact same cooling conditions in the vessel for each batch. Therefore, the distortion of the components will not be consistent from batch to batch.”
Read the case study to see one response to this issue in this original content from Heat Treat Today by Justin Sims, lead engineer at DANTE Solutions.
This article first appeared in the latest edition (March 2020) of Heat Treat Today’s Aerospace Heat Treating magazine.
Distortion is generally described by a size change and a shape change. In heat treatment of steels, size change is unavoidable and is mainly due to the volumetric difference between the starting microstructural phase and the final microstructural phase. Shape change of steel parts from heat treatment is due to nonuniform thermal and nonuniform microstructural strains as a result of nonuniform cooling or heating, alloy segregation, poor support of the component while at high temperature, thermal expansion or contraction restrictions, or residual stresses from prior forming operations. Nonuniform cooling or heating can be as fundamental as the temperature gradient from the part surface to its core, or as complex as the flow of fluid around a component feature. Both can result in nonuniform strains, resulting in a shape change. If the stresses causing these strains exceed the yield strength of the material, then permanent shape change will occur. Size change can be anticipated and is predictable, while shape change, or distortion, is usually unanticipated and more difficult to predict.[1-2]
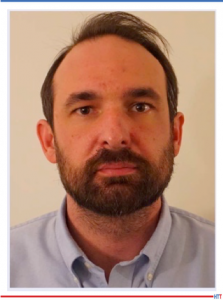
Lead Engineer,
DANTE Solutions
Most thermal processes try to control these nonuniformities using methods of low complexity such as part orientation and rack design. Quenching systems, for example, are generally designed to remove as much thermal energy from the work pieces as possible and to do this as quickly as possible. High-pressure gas quenching (HPGQ) attempts to reduce temperature nonuniformities by reducing the cooling rate; however, this is generally not sufficient to eliminate shape change. Shape change can be predicted by heat treatment simulation software, but it is difficult to reproduce the exact same cooling conditions in the vessel for each batch. Therefore, the distortion of the components will not be consistent from batch to batch.
In response to this issue, a prototype gas quenching unit capable of controlling the temperature of the quench gas entering the quench chamber was devised. With the DANTE Controlled Gas Quench (DCGQ) unit, it is possible to have control of the thermal and transformation gradients in the component by controlling the temperature of the incoming quench gas, thereby significantly reducing, or eliminating entirely, the shape change caused by quenching. In doing so, the size change can easily be predicted by heat treatment simulation software, and post-hardening finishing operations can be reduced or eliminated. This process is ideal for thin parts or components with significant cross-sectional changes. Atmosphere Engineering (now part of United Process Controls) in Milwaukee, Wisconsin constructed the unit and provided the logic to control it. All experiments with the unit were conducted at Akron Steel Treating Company in Akron, Ohio. The project was funded by the U.S. Army Defense Directorate (ADD).
Figure 1 (left) shows the front of the unit, while Figure 1 (middle) shows the back of the unit. The back of the unit contains the human machine interface (HMI), shown in Figure 1 (right), where process parameters can be modified and DCGQ recipes entered. The prototype unit has a working zone of nine cubic ft. and is capable of quenching loads up to 100 lbs. at one atmosphere of pressure.
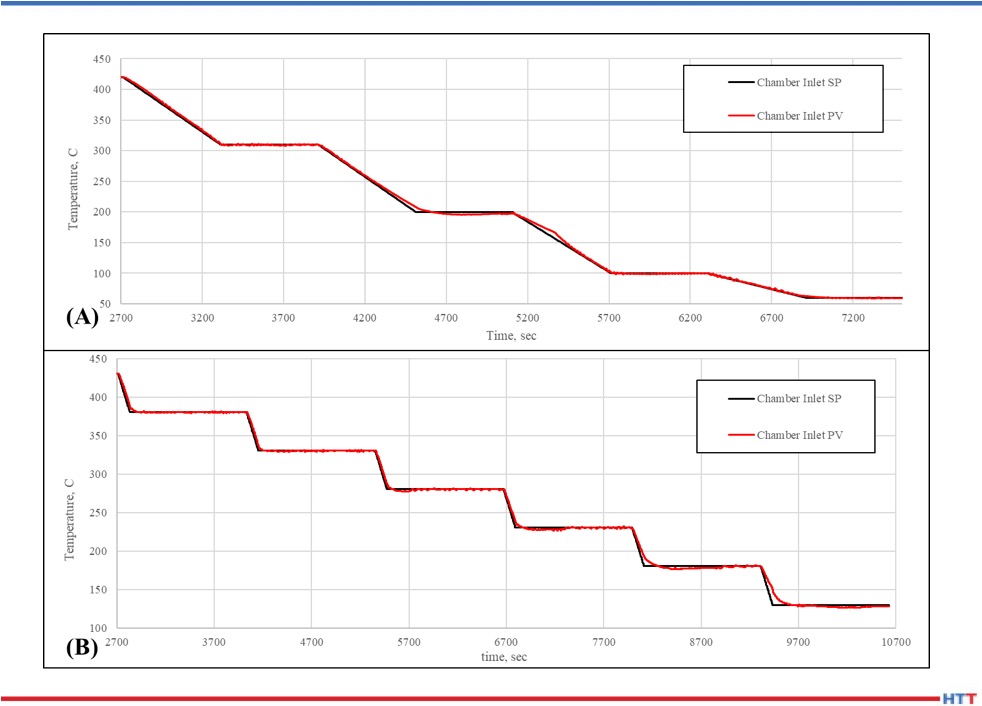
quench chamber versus the recipe setpoint temperature for
two different DCGQ process recipes
The ability of the unit to maintain continuity between the recipe setpoint temperature and the actual temperature entering the quench chamber is absolutely paramount. Figure 2 shows two schedules, one aggressive and one conservative, comparing the recipe setpoint (Chamber Inlet SP) to the actual quench gas temperature (Chamber Inlet PV). Figure 2 also shows that the prototype unit has good control of the quench gas temperature between 752°F (400°C) and room temperature, the martensite transformation range for most high hardenable steel alloys. There is some deviation between the two temperatures below 392°F (200°C) for the aggressive schedule as the setpoint reaches its set temperature, due to the relatively small temperature difference between the quench gas and the shop air. This small temperature difference makes it slightly difficult for the air-to-air heat exchanger used in the design to keep up with the rapid drop in temperature, but overall there is very good control of the quench gas temperature.

There is a copper layer on the surface of the DCGQ processed coupon.
Microstructural examination was conducted on Ferrium C64 coupons processed using the DCGQ process and coupons processedusing a 2-bar HPGQ. C64 was chosen for this study due to its extremely high hardenability and its high tempering temperature. Figure 3 compares the microstructures of the two processes at a magnification of 1000X, and no significant difference is detected. The DCGQ coupons required two hours to complete the transformation, whereas the HPGQ coupons transformed in a few minutes. There is no indication that the slow rate of transformation damaged the microstructure or mechanical properties in any way. Tensile and Charpy properties were equivalent between the two processes.
Distortion coupons, thick disks with eccentric bores, were designed and manufactured with the goal of evaluating the distortion response when subjected to a DCGQ process, and then compared to coupons subjected to a standard 2-bar HPGQ operation. All coupons were manufactured from the same Ferrium C64 bar stock. All coupons were cryogenically treated and tempered at 595°C for eight hours after quenching.
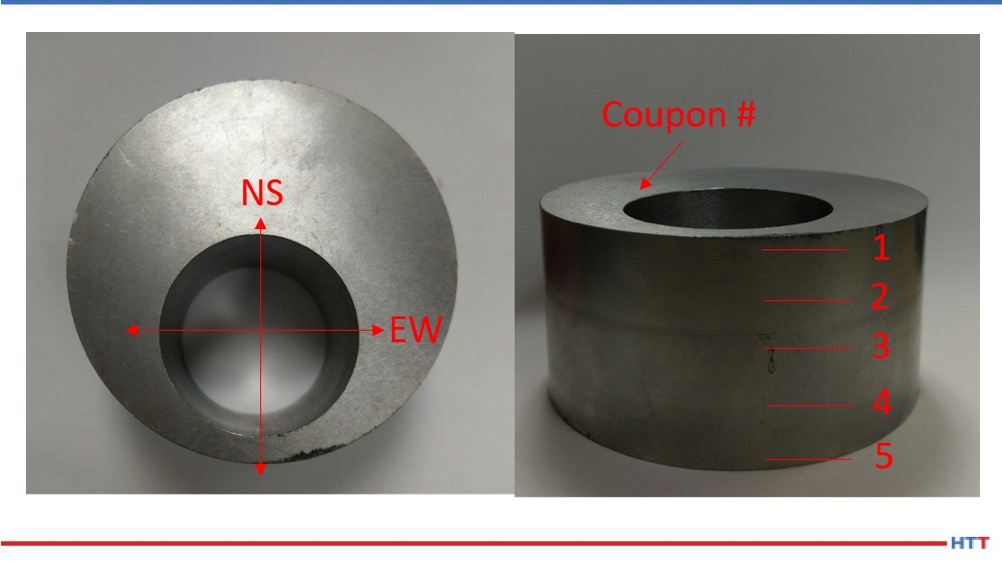
Figure 4 shows a distortion coupon with the nomenclature and locations used for measuring the out-of-round distortion of the eccentric bore. Due to the uneven mass distribution, the north-south direction will generally be larger than the east-west direction. Five measurements were then made along the axis of the coupon using a Fowler Bore Gauge.

Table 1 shows the results from four coupons; two hardened using the DCGQ process and two processed using the standard 2 bar HPGQ for C64. The individual measurements (EW1, NS5, etc.) are relative and are dependent on the reference value used for the bore gauge. The individual measurements give an indication of the variation in distortion in the axial direction. The out-of-round measurements are actual values, as they are the difference between the actual measurements. The DCGQ process gave significantly less distortion than the HPGQ process.
While the values reported show a 50% reduction in out-of-round distortion for the DCGQ process, a larger gain could have been realized if two other conditions were addressed. First, the coupon for DCGQ was placed directly into a 1832°F (1000°C) preheated furnace since the prototype unit does not have austenitizing capabilities. Controlled heating, just like controlled cooling, should be utilized to realize the full potential of this process. Second, the DCGQ schedule was designed for another coupon geometry that was processed together with these distortion coupons. Therefore, the schedule was not optimum for this coupon geometry.
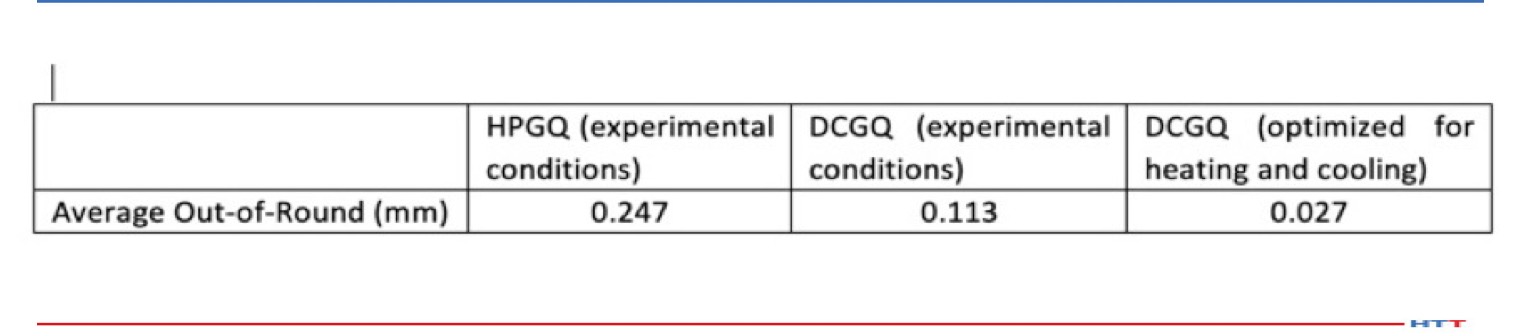
Table 2 compares the DCGQ simulation results in which the two processes executed on the experimental coupons were compared to an optimized process, including controlled heating and cooling schedules designed for this coupon. The optimized schedule predicts an order of magnitude reduction in out-of-round distortion. Comparison of the measurements from the HPGQ and DCGQ experiments in Table 1 to the model predictions in Table 2 shows that the model predictions agree closely with the experimental results.
Simulating the application of the DCGQ process to a gear geometry, the predicted warpage of a bevel gear was examined. The simulation looked at the differences between an oil quench, 10 bar HPGQ, and a 10 bar DCGQ process. From Figure 5, it is clear that the HPGQ process is predicted to produce the most distortion. Even though the 10 bar gas quench has a slower cooling rate than the oil quench, less distortion is not guaranteed since a slower rate does not guarantee a more uniform phase transformation.[3] In this case, both heating and cooling were controlled for the DCGQ simulation.
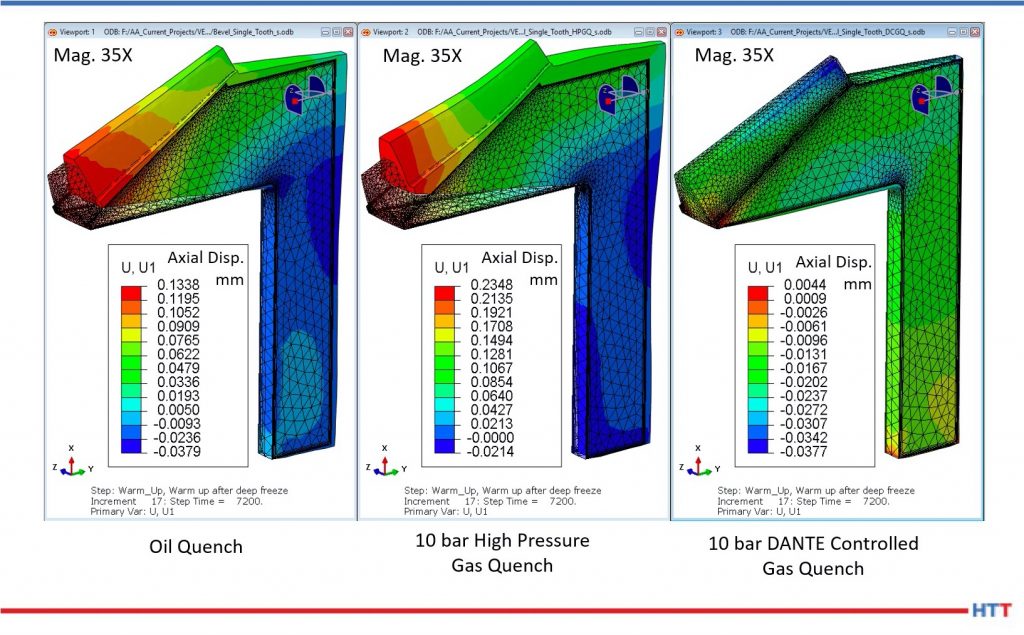
In summary, a prototype gas quenching unit has been constructed with the ability to accurately control the temperature of the quench gas entering the quench chamber. Experimental results have shown that mechanical properties and microstructure are equivalent between the DCGQ process and a 2-bar HPGQ process for Ferrium C64. Thick disks with eccentric bores were machined and then heat treated using DCGQ and HPGQ. It was shown that the DCGQ process reduced distortion in these disks by 50%. Simulation using DANTE then showed that the distortion could be reduced further if controlled heating and cooling are used. Finally, a comparison was made between an oil quench, HPGQ, and DCGQ processes for a bevel gear. This comparison showed that the HPGQ process was predicted to cause the most distortion. HTT
References
[1] Prabhudev, K.H., Handbook of Heat Treatment of Steels, Tata McGraw-Hill Publishing, 1988, p.111-114
[2] Sinha, Anil Kumar, ASM Handbook, Vol. 4: Heat Treating, ASM International, 1991, p.601-619
[3] Sims, Justin, Li Zhichao (Charlie), Ferguson B. Lynn, Causes of Distortion during High Pressure Gas Quenching Process of Steel Parts, Proceedings of the 30th ASM Heat Treating Society Conference, ASM International, 2019, p.228-236
About the Author: As an analyst of steel heat treat processes and an expert modeler of quench hardening processes, Justin Sims was the lead engineer for designing and building the DANTE Controlled Gas Quenching (DCGQ) prototype unit. This system was developed to minimize distortion of quenched parts made of high hardenability steels, while still achieving the required properties and performance.
For more information, contact Justin at DANTE Solutions