This instructive piece was first released in Heat Treat Today’s April 2025 Induction Heating & Melting print edition.
In heat treating, clean parts are essential for repeatable, high-quality results. Yet cleaning is often seen as a necessary evil rather than a strategic process. That mindset must change.
For decades, gas carburizing with oil quenching has dominated the industry despite challenges, such as contamination, environmental concerns, and part distortion. These issues have driven growth in alternative processes, such as vacuum carburizing with gas quenching and nitriding, which eliminate post-quench oil contamination. However, not all metallurgical requirements can be met with these newer processes, and gas carburizing with oil quenching remains necessary for many part sizes, geometries, and material types. Furthermore, some alternative processes require more advanced pre-cleaning technology, adding complexity.
I briefly left heat treating in 1998 — I call it my sabbatical from heat treating — to work in advanced industrial cleaning and automation. When I returned about five years later, I was struck by how far behind the industry was in cleaning technology. While other manufacturing sectors had embraced modern solvent and hybrid cleaning systems, heat treating continued to rely on outdated aqueous washers that struggle to clean oil-contaminated parts effectively. It goes back to the old axiom: oil and water don’t mix. Spraying harder only emulsifies the oil further, making separation and disposal even more difficult, increasing costs, and creating sustainability concerns.
Paths Forward
- Process shift — Where practical, companies have transitioned from oil quenching to vacuum carburizing with gas quenching, nitriding, and other alternative processes that reduce contamination issues. Of course, such changes are not driven solely by cleanliness — metallurgical requirements and process economics are complex topics. Gas carburizing with salt quenching is an often overlooked alternative, which offers superior heat transfer over gas quenching, reduces distortion, and is environmentally sustainable. Unlike oil quenching, cleaning aft er salt quenching is far simpler, as hot-water washers reclaim over 99% of the salt in a closed-loop system. The old negative mindset about salt, which questions the safety and toxicity of high temperature salt, has restrained process growth in this area. New equipment designs could create interesting, alternative paths with multiple benefits.
- Mindset shift — If oil quenching remains necessary, cleaning processes must improve. Conventional aqueous washers are inefficient, and while modern cleaning systems are effective, they are costly. However, when considering part quality, sustainability, efficiency, and long-term cost savings, these systems provide a strong ROI and should not be dismissed.
- Technology shift — Sustainability in cleaning cannot be ignored. Water-based systems with distillation attempt to recycle but have high energy costs, making solvent-based systems with integrated distillation more practical for higher efficiency and lower hazardous waste output.
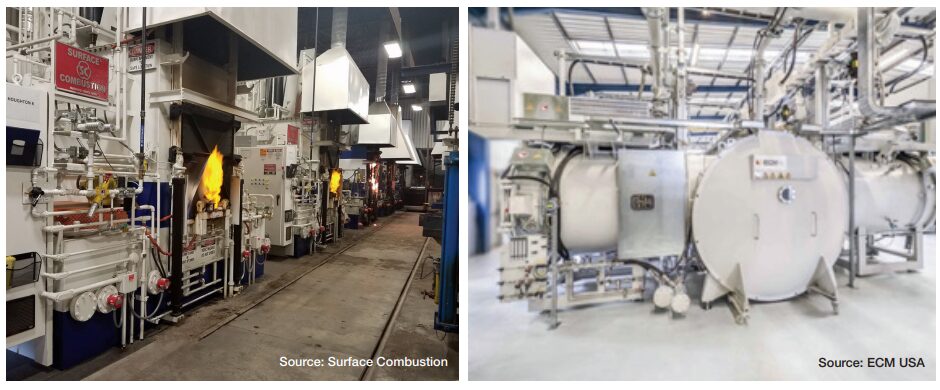
Challenges with Modern Washer Designs — Thoughts for Manufacturers
One major barrier to adopting advanced cleaning systems is cost, driven by their design. Many new washers are built for clean, controlled environments like vacuum heat treating but are poorly suited for traditional heat treat shops using oil quenching. Th ese shops have different requirements — floor space constraints, varied load configurations, and harsher conditions — meaning rugged, adaptable, and cost-effective solutions are needed. Function must take priority over aesthetics.
Washer manufacturers should rethink their designs to better fit conventional operations by focusing on durability, modularity, and cost-conscious engineering. Doing so could lower costs while improving adoption rates and accelerating industry-wide improvements in part cleanliness, quality, and sustainability.
Conclusion
Heat treating is changing, and cleaning technology must evolve with it. Whether by adopting better process alternatives, improving cleaning methods, or rethinking equipment design, companies that embrace innovation will reduce waste, improve efficiency, and ensure long-term success with a stronger commitment to sustainability and environmental responsibility.
The industry is evolving. It’s time to evolve with it.
References
- “All About IQ Furnace Systems.” Heat Treat Today, 4, no. 1 (February 2021): 16-28. https://www.heattreattoday.com/ february-2021/
About The Author:
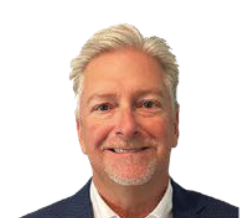
President
WDD Consulting LLC
William (Bill) Disler entered the heat treat industry as a young engineer, quickly establishing himself as a hands-on expert and eventually leading an international heat treat supplier company as CEO/president. He now serves the industry as a strategic advisor and partner to the C-Suite, as an engaged board member, through his consultancy, WDD Consulting, and in roles where he can make a positive impact.
For more information: Contact Bill Disler at wdisler@wddconsulting.com