Precise heat treating is essential to enable components to withstand space exploration. In this Technical Tuesday, Mike Grande, vice president of Sales at Wisconsin Oven Corporation, discusses the role of aluminum solution treatment and aluminum aging in heat treating space exploration components.
This column was first released in Heat Treat Today March 2024 Aerospace Heat Treat print edition.
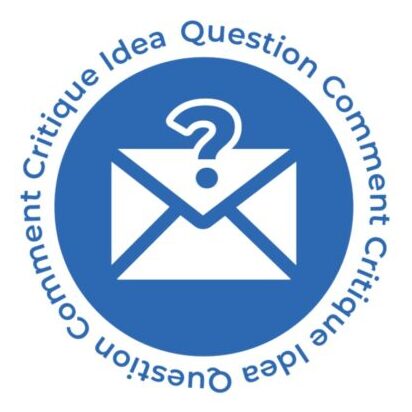
In space exploration, the various parts, electronic components, and materials used to make the rockets, crew capsules, rovers, and other equipment, are subjected to brutal extremes of temperature, vacuum, and radiation. In order to withstand these extreme environments without failure, the parts must be manufactured to very tight tolerances and precisely heat treated. Therefore, convection heat treatment emerges as a critical process in the manufacturing of space exploration components and materials, offering tight control over temperature profiles and the microstructure of materials.
Heat treatment involves heating a material to a specific temperature, holding it at that temperature for a certain duration, and then cooling it down at a controlled rate, which can be rapid or gradual, depending on the objective. The purpose of heat treatment is to improve the material’s mechanical properties, such as strength, ductility, and toughness. Probably the most common metal used in space exploration is aluminum. It is an excellent choice for spacecraft components because it is lightweight, durable, and has excellent thermal conductivity, which is necessary for components that need to dissipate heat.

The first stage of the Falcon 9, for example, utilizes four legs used during landing. They are manufactured from an extremely light, rigid, aluminum honeycomb material that also contains carbon fiber and has a very high strength to weight ratio. Another aluminum component common in space exploration is gas transfer tubes, used to transfer gases, such as methane, between chambers in the interior of rocket propulsion systems. Additionally, there are composite overwrapped pressure vessels (COPVs), which carry compressed fuels such as hydrogen and oxygen, among other gases. These are made of an aluminum tank covered with filament-wound, resin-impregnated composite material, which forms an extremely robust structure capable of withstanding the high pressures created by compressed gases and the rigors of high-speed propulsion. For aluminum to be useful in space applications, it must be heat treated to give it the strength and durability required.
Aluminum Solution Treatment
Since aluminum has such widespread use in space exploration, aluminum heat treatment plays a central role in this industry, with solution treatment and aging being the most common heat treatments utilized. All aluminum materials that require high strength are solution heat treated, then subsequently aged, in two separate heat treat processes. The purpose of solution heat treatment is to evenly dissolve the alloys contained in the aluminum, such as manganese, magnesium, copper, zinc, and silicon, and then rapidly quench it to retain the grain structure. The aluminum alloy is heated and held at a temperature of 800°F to 1000°F (420°C to 540°C), which is just below its melting point. The aluminum is then quenched in water or a water/glycol mixture quickly (within 7 to 15 seconds) to essentially “freeze” the microstructure before the alloying elements can redistribute themselves.
Aluminum Aging
After quenching, aluminum is precipitation hardened. Also known as artificial aging, this process involves heating the aluminum at a lower temperature, typically in the range of 200°F to 400°F (93°C to 204°C) for several hours. This final process dramatically increases the hardness, yield strength, and ultimate strength of the aluminum, making it suitable for use in space applications.
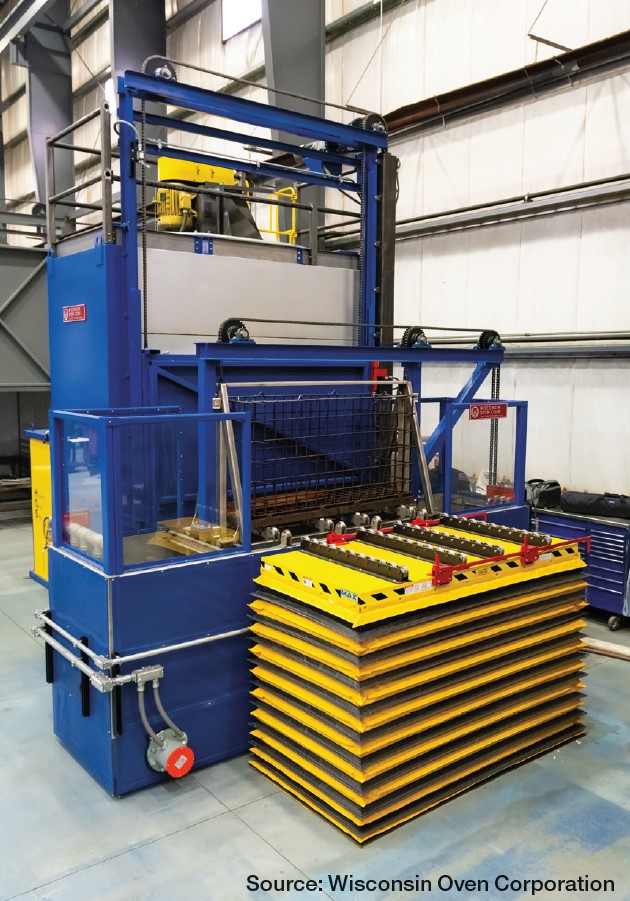
The above is just a sample of the many types of heat treatments for materials used in space exploration. Other examples are annealing, tempering, normalizing, and hydrogen embrittlement relief, to name a few. In conclusion, heat treatment plays a critical role in the manufacturing of parts used in space exploration and is essential to the reliability and safety of space missions.
About the Author

Mike Grande has a 30+ year background in the heat processing industry, including ovens, furnaces, and infrared equipment. He has a BS in mechanical engineering from University of Wisconsin-Milwaukee and received his certification as an Energy Manager (CEM) from the Association of Energy Engineers in 2009. Mike is the vice president of Sales at Wisconsin Oven Corporation.
For more information: Contact sales@wisoven.com.