Jason Schulze on AMS2750E: Initial and Periodic Temperature Uniformity Surveys
This is the seventh in a series of articles by AMS2750 expert, Jason Schulze (Conrad Kacsik). Click here to see a listing of all of Jason’s articles on Heat Treat Today. In this article, Jason advances the discussion of initial and periodic TUS requirements. Please submit your AMS2750 questions for Jason to editor@heattreattoday.com.
Introduction
Any technician who has performed a Temperature Uniformity Survey (TUS) understands that the assembly, use, and placement of thermocouples is imperative to the success of the TUS.
As we move through the requirements of Temperature Uniformity Surveys, we will examine the requirements that apply to TUS thermocouples.
Initial Temperature Uniformity Surveys
Before we get started, let’s take a look at how AMS2750E describes :
An initial TUS shall be performed to measure the temperature uniformity and establish the acceptable work zone and qualified operating temperature range(s). Periodic TUS shall be performed thereafter in accordance with the interval shown in Table 8 or 9. ~ AMS2750E page 23, paragraph 3.5.1
Most companies, whether purchasing a new furnace or used one, know what they would like the acceptable work zone size and qualified operating range to be. I emphasize “would like” because what we would like our furnaces to be capable of is not always what they are able to do. We would like to use every square meter of our furnace control zone in an effort to maximize capacity and, of course, maximize profit on each cycle we process. We would like our furnaces to operate at the very limits of what the furnace manufacturer states it can do. Unfortunately, these items don’t always exist once the furnace is subjected to an initial Temperature Uniformity Survey per AMS270E.
An initial TUS is used to tell us what our furnaces can do based on pre-determined parameters. Normally, these parameters should be flowed down to our furnace manufacturers, and prior to shipping, these parameters are compared to what the furnace can actually attain making the furnace conformative and ready for shipment. I strongly recommend this whenever purchasing a new or used furnace.
Initial temperature uniformity testing requirements are as follows;
- Initial survey temperatures shall be the minimum and maximum temperatures of the qualified operating temperature range(s).
- Additional temperatures shall be added as required to ensure that no two adjacent survey temperatures are greater than 600 °F (335 °C) apart.
These requirements are simple and straight forward. One could argue that I may be oversimplifying the requirements of an initial TUS, but let’s not forget, these are merely the requirements, not the conditions, under which an initial TUS must be performed. Let’s look at an example that would conform to the stated requirements.
Example
A furnace (in this case, it is irrelevant what type of furnace or what it is used for) processes production hardware from 900°F to 2200°F. Based on the requirements of AMS2750E, the initial TUS would start by testing at 900°F and the last temperature tested would be 2200°F. The supplier would need to select temperatures between 900°F and 2200°F to ensure that there is no more than a 600°F gap between each adjacent temperature. Figure 1 is an example of temperatures that could be selected.
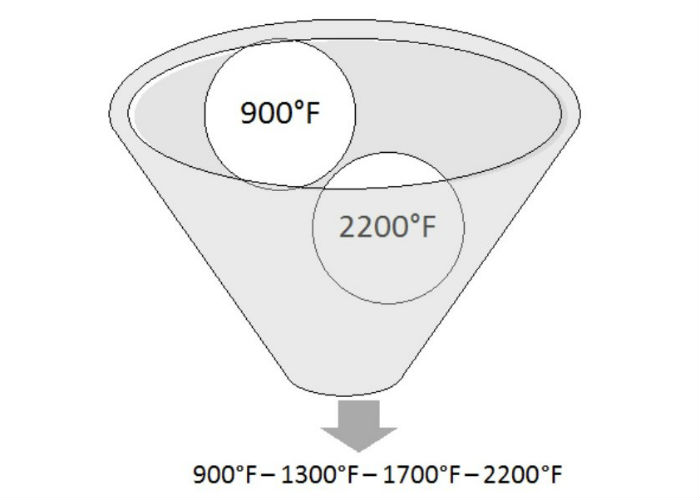
We’ve covered the requirements of an initial TUS; we will now address the conditions when an initial TUS is required. Initial TUSs are required when a) the furnace is installed (new or used) and b) when any modifications are made that can alter the temperature uniformity characteristics. You could dispute this by stating if a TUS fails (and the furnace is then repaired to be put back in service), if the qualified work zone is expanded, if a thicker control thermocouple is installed, etc. a new initial TUS is required. I would agree, but these would all fall under “B”.
Periodic Temperature Uniformity Surveys
Periodic TUSs are performed for single operating ranges greater than 600°F. In this case, the temperatures are selected must be 300°F from the minimum- and 300°F from the maximum-qualified operating range. If there is a gap of greater than 600°F, additional temperatures must be selected so there is no gap greater than 600°F. Using the example above, we could select temperatures as stated in Figure 2 below.
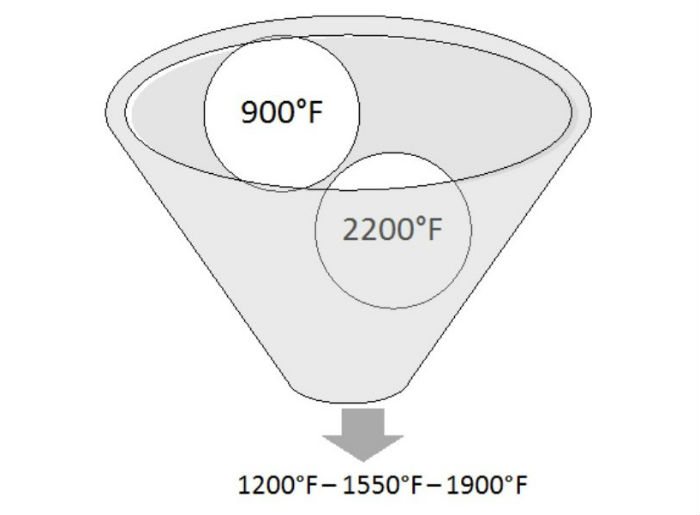
It is required that at least once each calendar year the minimum and maximum temperatures of the qualified operating range (in our example, it would be 900°F and 2200°F) are tested. Some suppliers may choose to perform an initial TUS once per year to ensure they capture the minimum and maximum.
Initial and Periodic Test Frequency
Tables 8 and 9 within AMS2750E describe the TUS frequency which is based both on furnace Class and Instrumentation Type. As an example, if our furnace referenced previously was identified as a Class 3 (±15°F), Type A instrumentation, the initial survey frequency would be quarterly. After two successful consecutive surveys, the frequency of testing could then be extended to being done annually.
It is important to recognize the difference between initial and periodic TUS temperatures and initial and periodic TUS frequency. Let’s use our example to expand on this. The supplier would perform a TUS using initial temperatures shown in Figure 1. If the TUS passes, the supplier would then, three months later, perform a TUS using the temperatures shown in Figure 2. This would then count as two successful consecutive TUSs. The next TUS could then be performed annually using the temperatures stated in Figure 2.
Conclusion
Understanding initial and periodic TUS requirements is imperative to ensure conformance to AMS2750E and Nadcap. In the next installment, we will discuss TUS data collection, relocation of hot and cold thermocouples, as well as quality requirements.
Submit Your Questions
Please feel free to submit your questions, and I will answer appropriately in future articles. Send your questions to editor@heattreattoday.com.
Jason Schulze on AMS2750E: Initial and Periodic Temperature Uniformity Surveys Read More »