Here is what readers are saying about recent posts on Heat Treat Today. As is our policy, we allowed the original author to preview and respond to this reader feedback. See Greg Odenthal’s response at the bottom of this post.
Submit your reader feedback comments to editor@heattreattoday.com.
William (Bill) Jones of Solar Atmospheres Inc. on the Heat Treat Radio podcast interview with Greg Odenthal of ITC Coatings. Click here for the podcast (transcript here):
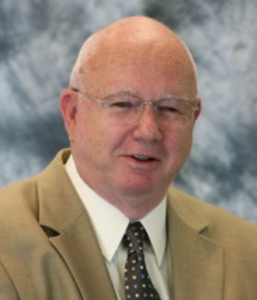
Re: Heat Treat Radio: ITC Coatings
This would be a poor selection for a vacuum furnace as it is well known that ceramic coatings and the like are hydroscopic and will absorb water from the atmosphere when opening the furnace to air for work unloading and reloading, with adverse effects on following vacuum pump down, i.e., to pump out the absorbed water vapor.
With respect to ceramic lined refractory insulated atmospheric furnaces: I can respect the coating for sealing an older furnace lining for porosity and lining leaks to the outer furnace wall and for improving re-radiation to the work load with well-known surface emissivity improvement. This is not an easy coating to apply and will require maintenance “man-hours”. So one has to balance the coating time and coating cost compared to furnace out of production cost. Furnaces are like airplanes, when sitting on the ground for any purpose, they lose money.
Now, when looking at furnace hot zone efficiency, one has to review power losses both before and after changes such as coatings. With an electric furnace a totalizing wattmeter or with a gas totalizing gas meter similar to our utility company meters. Such data needs to be presented for both furnace before and after coatings on an exact furnace and production cycle.
William R. Jones, FASM
Solar Atmospheres Inc.
We offered Greg Odenthal of ITC Coatings the opportunity to respond:
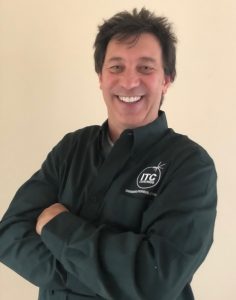
Mr. Jones,
I cannot agree or disagree with you regarding your opinion that ITC Coatings are a poor selection for vacuum furnaces as we have never tested in nor targeted this industry. It is true that ceramic coatings are hydroscopic; however, I’m not sure just how much water/moisture a layer of ceramic coating only 1 to 2 mils thick will absorb. With that being said, any moisture absorbed would wick away in a very short period of time. Whether or not they are good for the vacuum heat treating industry is still up for discussion.
As for your comment regarding that this is not an easy coating to apply, I must tell you that you are wrong. I have been onsite on just about every installation that we have done and our crew size can be very small. For an average size heat treat or forge furnace — for example, 32’ L x 16’ H x 15’ W with a new ceramic fiber lining — a crew of two men can and have coated the entire square foot surface area in an eight (8) hour shift. The cost of the coatings and labor to install is pennies on the dollar compared to the cost of regularly scheduled downturns every 3 to 4 months to pack joints and cracks with new fiber, trying to prevent heat loss and increasing fuel consumption. We have current customers that have not done any refractory maintenance in four to five years and now only have one outage per year for their yearly furnace inspection. Once installed, the ITC Coatings increase a furnace’s efficiency by reducing refractory maintenance, reducing fuel consumption, improving temperature uniformity, improving product quality, improving turnaround times, along with a host of additional benefits, thus preventing the furnace from costing the customer money, unlike your grounded airplane analogy.
In regard to hot zone efficiency and gas/power reduction, we have been working with the gas supply companies in Canada who are currently monitoring our customers’ fuel usage and see the reductions. They are now beginning to give current and potential customers money for this type of upgrade, upwards of 50% of the cost to install ITC Coatings. We do not just sell ceramic coatings, we provide the customer with a complete engineered solution along with a total Btu savings analysis for each furnace we quote. Each Btu savings analysis is unique to that furnace and based on operational data supplied by the customer. We have also provided before and after thermal imaging of the furnace as proof that the heat transfer/loss through the refractory and to the shell is less, so you do not necessarily need totalizing meters to prove energy savings.
If you would like to learn more about ITC Coatings and our technology, I encourage you to contact me and discuss this topic in greater detail.
Regards,
Greg Odenthal
Director of Engineering & Technical Operations
ITC| International Technical Ceramics, LLC
We welcome your inquiries to and feedback on Heat Treat Today articles. Submit your questions/comments to editor@heattreattoday.com.