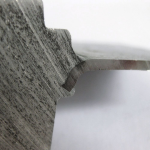
Groundbreaking research on a forging process in Hanover, Germany, has taken place in which bulk aluminum parts can be bonded with steel sheets during the forming process, eliminating the usual joining step. This would contribute to a faster and more efficient production of load-optimized components.
The Institute of Welding and Machining (ISAF) of TU Clausthal cooperated with the Institut für Integrierte Produktion Hannover (IPH) gGmbH in releasing their joint research aiming to be the first to combine two lightweight materials and construction approaches to make the process more efficient. The project, known as hybrid compound forging, focused on the challenge of integrating steel and aluminum with a third material to avoid brittle intermetallic phases.
The researchers’ idea is to form and join a steel sheet and a solid aluminum stud in one process step. In the past, the individual parts have been formed first and then joined in a second step, for example using stud welding. The idea of hybrid compound forging is to eliminate the subsequent joining step.
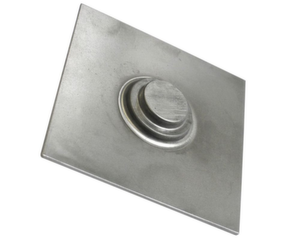
Since aluminum has a considerably lower melting point than steel, the joint forming process is more complicated. Moreover, the mixing of steel and aluminum creates brittle intermetallic phases, a material bond which is not strong enough and thus unsuitable for car manufacture. For this reason, the researchers employ zinc-plated steel sheets and aluminum studs: Zinc firmly bonds to aluminum as well as to steel without creating brittle phases.
Within the scope of the research project, the researchers are tasked with determining the most suitable process conditions – i.e. optimal temperature, pressure and speed for successfully forming and joining the two parts. They also try to identify the suitability of the novel process with respect to different types of sheet thicknesses and stud shapes and to determine the joining zone’s capacity to withstand load as well as the machinability of the hybrid part after joining. The researchers have already succeeded in combining sheet and bulk metal parts of different materials in one single forming step – but only as a prototypic form-fit connection between steel sheet and aluminum stud. In the current research project “Hybrid Compound Forging”, the researchers are going for a material bond using zinc as filler material which also offers advantages as to contact corrosion in the steel-aluminum material combination.
In the future, hybrid compound forging could be used in the automotive and aerospace industry to produce components, such as longitudinal beams, tail lamp mounts or cargo tie-down rings.