Aerospace Tech Provider Refines Focus with Acquisition, Spin Offs
In one of the largest acquisitions in aerospace history, a high technology product and service provider to the building and aerospace industries recently announced the completion of its purchase of a company that provides avionics and information technology systems and services to government agencies and aerospace manufacturers.
United Technologies Corporation’s (UTC) acquisition brings together Rockwell Collins and UTC Aerospace Systems to create Collins Aerospace Systems.
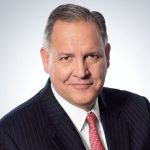
“Collins Aerospace brings together two great companies with unmatched expertise in developing electrical, mechanical and software solutions,” said Gregory Hayes, United Technologies Chairman and Chief Executive Officer. “We will have a laser focus on developing innovative solutions for customers and generating strong returns for shareowners.”
In addition, the Farmington, Connecticut-based, UTC announced its intention to spin off its commercial businesses, Otis and Carrier (renamed, formerly Climate, Controls & Security), into independent entities. The acquisition and separation will result in three global companies:
- United Technologies, comprised of Collins Aerospace Systems and Pratt & Whitney, to be a systems supplier to the aerospace and defense industry; Collins Aerospace was formed through the combination of UTC Aerospace Systems and Rockwell Collins;
- Otis, the world’s leading manufacturer of elevators, escalators and moving walkways; and
- Carrier, a global provider of HVAC, refrigeration, building automation, fire safety, and security products.
“Our decision to separate United Technologies is a pivotal moment in our history and will best position each independent company to drive sustained growth, lead its industry in innovation and customer focus, and maximize value creation,” said Hayes. “Our products make modern life possible for billions of people. I’m confident that each company will continue our proud history of performance, excellence, and innovation while building an even brighter future. As standalone companies, United Technologies, Otis and Carrier will be ready to solve our customers’ biggest challenges, provide rewarding career opportunities, and contribute positively to communities around the world.”
Aerospace Tech Provider Refines Focus with Acquisition, Spin Offs Read More »