AM Solutions Supplier Plans EBAM® System for Aerospace Applications
A leading metal additive manufacturing (AM) group based in Chicago recently announced that it will deliver large-scale metal 3D printing system to a supplier of highly engineered AM solutions.
Sciaky, Inc., a subsidiary of Phillips Service Industries, Inc. (PSI) will deliver an industry-leading Electron Beam Additive Manufacturing (EBAM®) 110 System to Burloak Technologies, a division of Samuel, Son and Co., Limited, which delivers high quality, lightweight, fully functional additive manufactured parts for a range of industries including space, aerospace, defense, energy, medical, automotive, and transportation.
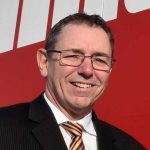
“Using traditional subtractive processes, such as forging and machining, the production of titanium parts of this size could take one year while generating a significant amount of waste,” said Peter Adams, co-founder and president of Burloak Technologies. “Our EBAM 110 system will allow us to manufacture the same large-scale titanium structural parts in a matter of days. We are already engaged with several aerospace end-users who have started the qualification process with us.”
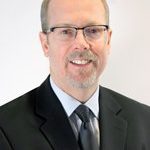
“Sciaky’s EBAM systems are the most widely sold large-scale metal 3D printing system in the world, having qualified parts on land, sea, air, and space applications,” said Scott Phillips, president and CEO of Sciaky, Inc. “The innovators at Burloak Technologies will leverage the numerous benefits of EBAM to produce faster and cheaper parts for their customers all across the globe.”
A July 2019 delivery is scheduled for this EBAM system.
AM Solutions Supplier Plans EBAM® System for Aerospace Applications Read More »