Canadian Centers of Excellence Established for Helicopter Airframe, Engine MRO Services
An independent provider of engine and airframe services recently announced a 12-18 month company restructuring of its primary Canadian MRO facilities to create three different Centers of Excellence (COEs) specifically for supporting Helicopter Airframe/Component MRO services, Helicopter Engine MRO services and Turboprop Engine MRO services at facilities located in Langley, British Columbia; Winnipeg, Manitoba; and Summerside, Prince Edward Island.
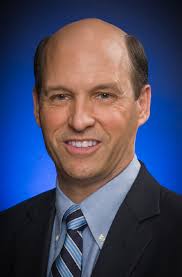
In addition, StandardAero intends to wind down its operations at its Richmond, B.C. facility by June of 2019 as part of the restructuring plans. Helicopter engine MRO services currently performed at Richmond will be relocated to StandardAero’s Winnipeg facility, including all Safran Arriel 1&2, Rolls-Royce M250, GE T700 and Pratt & Whitney Canada (P&WC) PT6T helicopter engine MRO services. Winnipeg will serve as the company’s COE for all Helicopter Engine MRO services. Helicopter dynamic components, currently located in Richmond, will be relocated to the company’s Langley facility which will serve as the COE for Helicopter Airframes/Component MRO services moving forward.
In order to accommodate all of the helicopter engine MRO capabilities in Winnipeg, StandardAero is moving its Winnipeg P&WC PW100 MRO engine services and as well as the existing P&WC PT6A work to its facility in Summerside – which will become the company’s COE for Turboprop Engine MRO.
“Over the past several months, our team has been working carefully to drive integration activities and program management to combine our legacy StandardAero and Vector Aerospace facilities,” said Russell Ford, CEO of StandardAero. “A big part of our overall acquisition strategy is to ensure we establish these Centers of Excellence (COEs) and combine or consolidate relevant engine platforms to eliminate duplicate operations, while also freeing up capacity to accommodate our growth programs.”
StandardAero services include engine and airframe maintenance, repair and overhaul, engine component repair, engineering services, interior completions and paint applications to a diverse array of customers in business and general aviation, airline, military, helicopter, components, and energy markets.
Photo credit: StandardAero
Canadian Centers of Excellence Established for Helicopter Airframe, Engine MRO Services Read More »