Auto Supplier Expands Heat Treating Capabilities with New Oven
A leading automotive supplier in the U.S. recently received a large oven for its operations. This furnace was customized with a heavy duty cast work tray which sits on the floor of the chamber inside the liner area to support the workload and protect the floor brick.
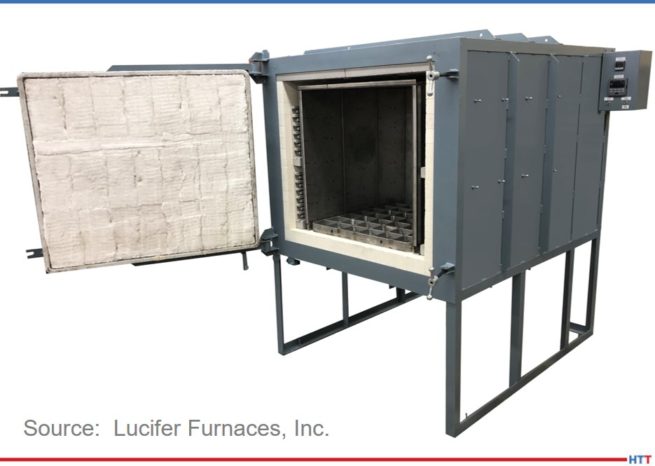
The 4000 series oven from Lucifer Furnaces is a Model 42-T36 and has a chamber size of 30″H x 30″W x 36″L, heating to 1200°F with 35 KW of power.
This model is complete with a high CFM rear mounted fan assembly to recirculate the heated air uniformly throughout the chamber. A stainless-steel liner isolates the heating elements from the work area and directs air forward over the heating elements and back through the chamber in a horizontal pattern for uniform heating.
The horizontal swing door is lined with lightweight pyroblock insulation with a ceramic fiber gasket to reduce heat loss around the chamber opening. A safety microswitch automatically shuts off power to heating elements and fan when door is opened, eliminating electric shock and heat blast hazards to oven operator. Controls include a Honeywell digital time proportioning temperature controller accessorized with a high limit controller for safety in the event of a high temp excursion.
Auto Supplier Expands Heat Treating Capabilities with New Oven Read More »